Contact | Subscribe | Media centre
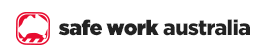
- Lifting, pushing and pulling
- Psychosocial hazards
- Working at heights
- Crystalline silica and silicosis

Managing health and safety
- Identify, assess and control hazards
- Safety data sheets
- Personal protective equipment
- Emergency plans and procedures
- Incident reporting
Industry and business
- Construction
- Small business
- Agriculture
- Gig economy
The Commonwealth, states and territories regulate and enforce WHS laws.
Find your Regulator
Model WHS Laws
We created the model WHS laws in 2011.
- Model WHS Act
- Model WHS Regulations
- Duties under Model WHS laws
- Codes of Practice
- Legislation
WHS laws in your jurisdiction
Contact your regulator
Data and Research
We collect, analyse and publish data and information on work health and safety and workers' compensation.
See our data
- Work-related fatalities
- Work-related injuries
- Work-related diseases
- Return to Work
- Explore our data
- About our data
- Industry benchmarking
- Research by industry or topic
See our latest Key work health and safety statistics
explore our data
Workers' Compensation
We develop national policy and strategy about workers' compensation.
- Workers’ compensation
- Comparing workers' compensation in Australia
- National Return to Work Strategy
- Deemed diseases
- Permanent impairment
- Workers' compensation for psychological injury
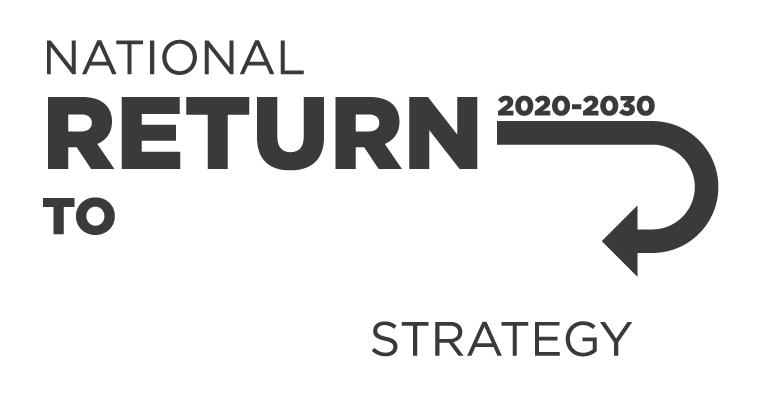
Read the Strategy
Resources and Publications
We publish a wide range of resources covering many work health and safety topics.
- Codes of practice
- Video and audio
- Corporate publications
Media centre
- Media releases
- News update
Read our Codes of Practice
read the codes
Slips, trips and falls
- Know your duties - a tool for working safely
- Hazards information
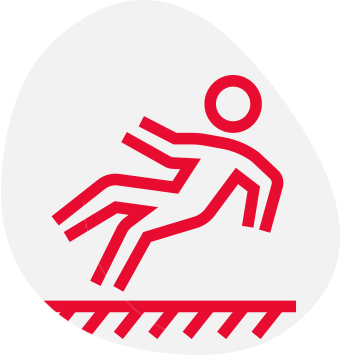
You don’t have to be high off the ground for a fall to cause significant injury or death. Falls can occur in many different ways including through slips and trips, or falls from height, at level, or into holes or voids.
Each year slips, trips and falls cause injuries and fatalities in the construction industry, such as when:
- Working from height
- There is insufficient lighting
- Being hit by falling objects
- Ground surface, floors or other building surface are slippery, uneven or cluttered with building materials, power tools or equipment.
Slips occur when a person’s foot loses traction with the ground surface.
Trips occur when a person unexpectedly catches their foot on an object or surface.
Falls can result from a slip or trip but many also occur during falls from low heights such as on steps, stairs and curbs, into a hole or a ditch.
Consulting with workers can help you find better and easier ways to identify and minimise risks. You should also review control measures to ensure they are working as planned.
Note : If high risk construction work is being carried out that involves a risk of a person falling more than two metres, a safe work method statement (SWMS) needs to be prepared. For more information on safe work method statements, please click here . Alternatively, you can also use the interactive SWMS tool to learn how to complete a SWMS.
Risk management
Identify and assess hazards .
You must identify and assess the workplace for any slip, trip and falls hazards. Think about work areas, work procedures, tools and equipment.
Control measures
If you can’t eliminate the risks from slips, trips and falls, you must minimise them as much as possible, including by:
- Ensuring all areas are well lit.
- Having good drainage and slip resistant grates.
- Positioning yard and gates to avoid having to move through muddy areas.
- Installing extra power points to avoid trip hazards from trailing cords.
- Having clear procedures for workers to return equipment, tools and other items to their storage areas after use.
- Having clear procedures for workers to report and clean spills.
- Providing training to workers to become more aware of slip and trip hazards.
- Wearing slip-resistant footwear.
Review control measures
The last step of the risk management process is to review the effectiveness of the implemented control measures to check they are working as planned. If a control measure is not working well, it must be changed or replaced.
See Part 3.1 of the Model WHS Regulations for more information on risk management.
For more information
Model Codes of Practice
- How to manage work health and safety risks
- Managing the work environment and facilities
Other resources
- Managing the risk of a fall - infographic
- Slips and trips - fact sheet
- The interactive safe work method statement (SWMS) tool provides information on preparing, using and reviewing SWMS for high risk construction work.

Did you know
The WHS regulator in your state or territory can provide practical advice, resources and tools to help you be safe when working in construction. They can also let you know which WHS laws apply to you.
- I would like to start again
- I would like to re-select my role
- This tool is only available for selected industries at this stage. If you are looking for information relating to industries not covered by this tool, check out our industry and business information.
Industry and business information
Share your feedback
This tool is a pilot. Share your feedback so we can improve it.
Further Advice
SWA is not a regulator and cannot advise you about WHS issues in the workplace. If you need help please contact your state or territory work health and safety authority .
We develop national policy relating to WHS and workers' compensation.
- Skip to content
- Skip to navigation
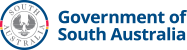
SafeWork SA
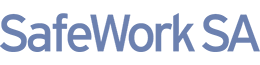
- Compliments and feedback
- Contact our WHS Advisory Service
- Independent Review
- Advisory Service
- Information disclosure
- WHS Inspectors
- Strategic Plan
- Annual Activity Report
- Freedom of information
- Past winners
- Who was Augusta Zadow?
- Body Worn Cameras
- Farmers' guidebook to work health and safety
- Farm safety video series
- Farm chemical safety video series
- Plant, tools & vehicles
- Work tasks & projects
- Chemicals & substances
- Marine distress flares
- Personal flotation devices
- Snorkel safety
- Tuna farm diving
- Bow ladders
- Domestic commercial vessels
- Grain silos
- Livestock handling guidelines
- Portable field bins
- Vineyards & Wine
- Safety in the automotive industry
- Hazardous manual tasks in automotive workshops
- Vehicle hoists, jacks, ramps and stands
- Traffic management in automotive workshops
- Plant, tools and vehicles in the automotive industry
- Machinery and equipment in automotive workshops
- Hazardous chemicals in automotive workshops
- Roadside maintenance
- Service pits in automotive workshops
- Safety in construction
- Engineered stone prohibition
- Safe Work Method Statements
- Abolishment of electricity supply
- Confined spaces
- Principal contractors and construction projects
- Residential building site induction
- Scaffolding work
- Scaffolds - Access and egress
- Edge protection for roof work (guardrail systems)
- Respirable crystalline silica in construction and demolition work
- Hose whip on concrete pumps
- Site security
- Drill-in anchors
- Precast tilt up & concrete elements
- Transporting of pre-cast panels/elements
- Operating cranes in protected air space
- Construction work toilet facilities
- Home & community care
- Electrical safety of power-assisted beds
- Hazardous and cytotoxic drugs
- Height adjustable treatment tables or beds
- Coronavirus (COVID-19)
- Safety in the hospitality industry
- Burns and scalds
- Food catering - Events
- Hospitality managers guide to WHS
- Safety in the manufacturing industry
- Hand sanitiser
- Pallet racking
- Sexual harassment, discrimination and violence in mines
- Safety in the mining industry
- Safety management systems
- Mining regulations
- Mine manager competencies
- Information, training and instruction (Mining)
- Blasters & explosives licences
- Mine emergency
- Recordkeeping
- Health monitoring
- Opal field shafts
- Mining news
- Event safety
- Gymnasiums & Trampoline centres
- Amusement devices (Plant)
- Inflatable amusement devices
- Upcoming fireworks displays
- Safety in the retail industry
- Retail trading hours
- Christmas and Easter trading arrangements
- Customer aggression and violence in retail
- Escalator and moving walkway void in-fills
- Shopping trolley collection
- Supermarkets
- Tenancy agreements
- Vending machines
- Safety in stevedoring
- Road transport
- Transport of dangerous goods
- Apply / renew
- High Risk Work licences
- HRWL Client Portal
- Pay a licence or fine
- Licence holder registers
- Automatic mutual recognition of licences
- Licence Portal
- Accredited assessor / Training provider portal
- Change of contact details
- Workplace incidents
- Asbestos removal
- Demolition work
- Firework display
- Intent to import explosives
- Lead risk work
- Major hazard facilities
- Mine holder/operator
- What is a HSR?
- Notification of elected HSRs
- HSR Portal information for PCBUs
- HSR portal information for HSRs
- HSR portal information for Training Providers
- HSR training
- Approved HSR training courses
- HSRs for work groups of multiple businesses
- Provisional Improvement Notices
- Stopping unsafe work
- Report a workplace concern
- Employer responsibilities
- Primary duty of care
Worker responsibilities
- Apprentices & Trainees
- Contractors
- Kitchen workers
- Labour hire
- Mature age workers
- WHS for new and young workers
- Understanding your responsibilities at work
- Overseas workers
- Probation, work experience and trial work
- Health & Safety Committees
- Healthy workers & workplaces
- Air pollution and bushfire smoke
- Alcohol & Drugs
- Challenging behaviour
- Contact dermatitis
- Discrimination
- Grievance and complaint resolution
- Heat & UV
- Noise exposure
- Physical activity
- Sexual harassment - Advice for employers
- Sexual harassment - Advice for workers
Slips, trips & falls
- Work life balance
- Personal protective equipment
- Respiratory Protective Equipment
- Using RPE to minimise risk of exposure
- RPE as a control measure
- Fit testing and fit checking of RPE
- Training in the correct use and maintenance of RPE
- Monitoring the health of RPE users
- Inspecting, maintaining, repairing and storage of RPE
- Keeping records
- Discriminatory, coercive and misleading conduct
- Who is entitled to long service leave?
- Accruing leave
- Calculating long service leave
- Requesting and taking leave
- Pro-rata entitlement
- Payment of entitlement
- Transfer of business
- Resolving disputes
- Long service leave FAQs
- Download our Guide to Long Service Leave
- Minimum wage
- Minimum working age
- Enterprise agreements
- Industrial relations
- WHS issue resolution
- Employer and Employee responsibilities
- Managing the risk of family and domestic violence at workplaces
- Creating a workplace response to domestic and family violence
- Family and domestic violence leave
- Workers who use or may use violence and aggression
- If you need more help
- Managing health and safety risks
- Work from home
- Electrical risks at the workplace
- Electrical work
- Working in ceiling spaces
- Inspection and testing of electrical equipment
- Electrical installations or services
- Safe Electrical Practices on Construction and Demolition Sites
- Emergency response
- Work environment
- Cold storage facilities
- Cooling towers
- Lift emergency phones
- Abrasive blasting
- Excavation work
- Fragile roofing
- Hazardous manual tasks
- Installing prefabricated timber roof trusses
- Installing roof battens
- Managing risk of falls for solar panel installations
- Spray painting and powder coating
- Stairwells, atriums and voids
- Tree felling
- Working near utility services
- Angle grinders
- Circular saws
- Diesel exhaust
- Earthmoving equipment
- Elevating work platforms
- Firewood saws
- Hand & power tools
- Hardened steel tools
- Hydraulic fluid and fittings
- Isolation procedures
- Lifts & lift design (commercial)
- Lift registration (private residences)
- Mobile plant
- Multipurpose tool carriers
- Pressure plant & equipment
- Plant hydraulic systems
- Synthetic fibre slings
- Tyres, compressed air and split rims
- Wood chippers
- Vehicles as a workplace
- Simple Steps to Safety
- Codes of Practice
- What is an EPH?
- Obtaining an entry permit
- Entry permit holders policies
- Notice of entry to PCBU
- Exercising a right of entry
- Entry for a suspected contravention
- Entry to consult with workers
- Access to records or documents
- Appropriate behaviours for PCBUs and EPHs
- Revocation of entry permit
- WHS civil penalty provision
- Adhesives and sealants
- Airborne contaminants
- Carbon monoxide
- Chemical labelling
- Chemical storage, handling & security
- Dry ice and cryogenics
- Fibreglass reinforced products
- Flammable liquid storage and transport
- Hazardous chemicals
- Lead acid batteries
- LPG bottle labelling
- Polychlorinated Biphenyls
- Refrigerants
- Respirable crystalline silica
- Safety data sheets
- Workplace incident investigation
- Anxiety & Depression
- Bullying & Inappropriate behaviours
- Mental health
- Psychosocial hazards
- Psychological health for small business
- Psychosocial risk assessment
- Focus group guide
- Examining workplace data
- Mentally healthy workplaces documents
- Investigations
- Prosecutions
- Industrial manslaughter
- Enforceable undertakings
- Review of decisions
- Right of entry
- Compliance Program Audit Reports
- Safety alerts
- Let's Talk Safety
- Public Consultation on amendments to the Construction Industry Long Service Leave Act
- Subscribe to news
- Introduction to safety tutorial
- Organise your own workplace activity
- Registration form
- Promotional resources
- Schedule of activities
- Public holidays
- Toolbox safety talks
- Legislation
- Library services
- Free resources
Did you know half of all falls that resulted in a fatality involved heights of 3 metres or less? Slips, trips and falls are the second leading cause of workplace injury, after hazardous manual tasks.
These incidents are a significant problem affecting every workplace, from the factory floor to the office and quite often can result in serious injury and lengthy amounts of time off work.
Industries which experience the highest proportion of slips and trips are:
- manufacturing
- health and community services
- construction
- retail trade.
PCBUs, employers, managers and workers should refer to the Managing the risk of falls in the workplace - Code of practice .
Hazards and risks
Commons slip and trip hazards often arise from:
- the type and stability of the floor or ground surfaces such as uneven or broken concrete and sloping ground
- slippery floor surfaces caused by water, fluid spillage and oil
- equipment, boxes and materials blocking walkways
- stairs or steps
- carrying things that obscure the view ahead
- poor lighting
- inadequate or improper footwear
- incorrect use of ladders
- falling or moving objects
- distraction.
Fall hazards are often found where work is undertaken at heights such as:
- stacking shelves
- working on a roof
- unloading a large truck
- accessing a silo.
Falls can also occur at a ground level as a result of a slip or trip or falling into a hole such as a service pit or open hatch.
Employers and PCBUs have a duty of care to provide a safe workplace and systems of work, information, instruction and training. Additionally, they have to give workers an opportunity to consult about work health and safety, whilst being responsible for identifying hazards, assessing risks and managing the hazards also.
- contribute to a safe workplace by taking responsibility for your safety and the safety of people you work with
- follow all safe work instructions and procedures
- report safety issues
- use safety gear (PPE) where required.
Falls from height
To minimise the risk of a fall from height a PCBU / employer must:
- be familiar with the Managing the risks of falls in the workplace - Code of Practice
- provide a safe means of access/egress to/from any area that involves the risk of a fall
- for the construction industry, prepare and implement a site specific High Risk Construction Work prepare a Safe Work Method Statement (for work at heights above 3 metres)
- ensure that any work that involves the risk of a fall is carried out on the ground or on a solid construction, so far as is reasonably practicable
- eliminate, where possible, or minimise the risk of a fall by providing adequate control measures
- temporary work platforms
- training in relation to the risks involved in work at the workplace
- safe work procedures including safe sequencing of work, safe use of ladders, permit systems and appropriate signs
- where a fall prevention device is not reasonably practicable, provide a work positioning system
- fall arrest systems must be accompanied by an emergency and rescue procedure in relation to the use of the system.
Use a combination of controls to minimise risks if a single control is not sufficient for the purpose.
2022 snapshot - Falls from heights in the construction industry
Download snapshot in PDF

Risk assessment
A risk assessment should be undertaken to determine the level of risk and appropriate controls. This gives the PCBU the opportunity to discuss issues and negotiate suitable arrangements for reducing slips, trips and falls.
An important part of the risk management process is to have good communication and consultation between PCBUs, workers, health and safety representatives and committees. Doing so will help to identify hazards before any injury, illness or incident can occur. This then leads to developing measures to eliminate or reduce the associated risks.
As workers, you have a responsibility to protect your own health and safety along with others affected by the work, whilst also abiding by procedures and policies in relation to workplace safety. It is necessary for all workers to have important information and training to allow them to fulfil this obligation.
Risk control measures
Often, it is the little things that cause slipping, tripping and falling to happen in the first place, so it is important to remember to work together. There are several ways to help minimise these incidents occurring, such as:
- maintaining good house-keeping protocols, including rubbish removal
- storing equipment correctly
- using ladders and steps correctly
- reporting damage to floors and surfaces
- clearly identifying and staying on marked walkways
- implementing a clean and clear walkway policy
- affixing mats to the floor surface
- restricting access to areas that are potentially hazardous
- providing ramps instead of steps where the height of floor levels change
- restricting tasks to suitably trained workers
- providing adequate aisle width and lighting
- using warning signs.
Managing risk of falls video series
Our four-part educational video series will help business operators manage the risk when working at heights and assist them to comply with their work health and safety responsibilities.
Remember, controlling falls risks is the only option.
Falls from heights
Managing the risk of fall from one level to another that is likely to cause injury in line with the hierarchy of risk controls.
Hierarchy of risk controls
Sets out the order of managing risks when working from heights and the equipment and systems to match.
Safe use of portable ladders
Practical tips on how to use portable ladders correctly.

Training and supervision
The importance of training and supervision to ensure safe work practises are being followed.
Further information
- Slips, Trips and Falls Safety Scan – Auto Workshops
- Guide to managing risks of industrial rope access systems - Safe Work Australia
- Service pits - auto workshops
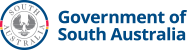
Australia’s leading manufacturer of safety cable covers and protectors
- Find a Dealer
- Gift Certificates
- Sign in or Create an account
- Your Cart :
Cable Covers and Protectors by TripSafe
- SATISFACTION GUARANTEE
- FREE SHIPPING*
- SECURE SHOPPING
- 1300-137-875 Contact Us
- TRIPSAFE PRODUCTS
- TESTIMONIALS
- Shipping & Returns
Identifying and controlling trip hazards
Posted on 30th Jul 2018
Trip hazards can be found in the office, home or commercial and public areas. It’s always important to adopt the prevention rather than cure approach by identifying trip hazards before someone becomes injured. Using a hazard identification and risk management process which identifies the hierarchy of controls can mitigate risks involved with slips, trips and falls.
Between 2003 and 2015 23% of serious work cover claims were a result of injuries caused by slips, trips and falls (source: safeworkaustralia.gov.au). The most common injuries are musculoskeletal, fractures, dislocations, cuts and bruises. More serious injuries can also happen.
For the elderly, a simple trip can result in serious injury and sometimes death from broken bones, in particular hips through to head injuries.
For Office Managers and Safety Officers it is imperative that trips hazards are controlled in order to ensure a safe work environment for employees.
Below are some suggestions on how to identify and also control these hazards.
Where appropriate, workplace staff should be encouraged to identify any trip hazards and if possible remove them immediately or isolate the area and then report it to key personnel. Additionally, it could be useful to ensure staff are trained properly to understand how slips or trips can occur. Ensuring staff are aware of what a safe work environment looks like will help increase the precautions they take. If employees are involved at all levels when looking at risks and agreeing to safety measures it is more likely that a hazard will be tackled successfully and with a higher level of compliance.
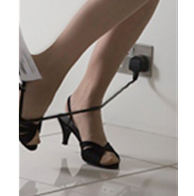
SHIPPING PARTNERS

SECURE ONLINE SHOPPING
Whether you are looking at reducing the risk of tripping from loose cables in the office or want to organise untidy electrical cords in your home study, TripSafeTM provide an effective and yet affordable cable management solution.
Using the TripSafe safety cable holders, you can easily secure loose and untidy cables to carpeted floors. Thanks to their low profile, TripSafe will minimise trip hazards and keep your home or office tidy.
Supplying to:
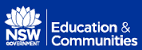

School operations
Slips, Trips and Falls Prevention
- 1. Ongoing management of slips, trips and falls prevention
- 2. Identifying and assessing slip, trip and fall risks and hazards
- 3. Controlling the risks
- 4. Hazard, incident and near miss reporting
This policy:
- outlines the health, safety and wellbeing requirements relating to the prevention and management of slips, trips and falls in schools
- supports the implementation of the department’s leadership commitment to health, safety and wellbeing (PDF) External Link .
Slips, trips and falls can place employees at risk of injury including sprains, strains, fractures and soft-tissue injuries.
This policy does not cover situations that involve working at heights of 2 metres or above (measured from the soles of your feet to the ground) or circumstances where a person could fall into a hole, trench or pit. Refer to the Prevention of Falls when Working at Heights policy for this information.
Roles and responsibilities in preventing slips, trips and falls
Under the Occupational Health and Safety (OHS) Act 2004 (Vic) External Link , managing the risk of slips, trips and falls is a shared responsibility between the department, the principal and/or their delegate and school employees.
- The department must maintain, so far as is reasonably practicable, a safe and healthy working environment for employees to avoid injuries from slips, trips and falls while working.
- The principal and/or their delegate, in consultation with the health and safety representative (HSR) and employees, must identify, assess and control the risks that are associated with slips, trips and falls.
- School employees must take reasonable care for their own health and safety and the safety of others who may be affected by their actions or omissions while at work, which includes managing slips, trips and falls.
Safety is a shared responsibility, and everyone including students has a role to play.
Key requirements for schools to prevent and manage slips, trips and falls
Schools must:
- consult with school staff and HSRs to identify, manage and prevent slip, trip and fall hazards
- identify slips, trips and falls hazards through observation, workplace inspections and incident reports
- assess new or complex hazards using a risk assessment
- report and manage incidents when they occur
- ensure that staff undergo appropriate training
- incorporate slips, trips and falls risk prevention into an ongoing management approach that promotes health, safety and wellbeing.
The Slips, Trips and Falls Procedure (in the Procedure tab) contains detailed, step-by-step information about how schools can meet these key requirements.
Department supports for schools
Central and regional offices provide a range of supports and services to assist principals and employees to be safe and well. These include access to the OHS Advisory Service and regional OHS support officers who can provide free advice in relation to managing slips, trips and falls.
Related definitions
Slips Slips occur when a person’s foot loses traction with the ground due to unsuitable footwear or walking on surfaces that are highly polished, wet or greasy.
Trips Trips occur when a person’s foot catches on an object or surface. In most cases people trip on low obstacles that are hard to spot such as uneven edges in flooring, loose mats, open drawers, untidy tools or electrical cables.
Falls Falls (under 2 metres) can result from a slip or trip but many occur during falls from low heights such as steps, stairs, and curbs, or falling into a hole, ditch or water.
Related policies
- Employee Health Safety and Wellbeing
- Managing and Reporting School Incidents (including emergencies)
- OHS Consultation and Communication
- OHS Planning
- OHS Risk Management
- Records Management — School Records
- Workers Compensation
- Workplace Inspection
Relevant legislation
- Compliance code: Workplace amenities and work environment External Link
- Occupational Health and Safety Act 2004 (Vic) External Link
- Occupational Health and Safety Regulations 2017 (Vic) External Link
Reviewed 24 June 2022
- Print whole topic
Policy last updated
24 June 2022
- School councils
OHS Advisory Service
- Worker Assist (Opens in an external website)
- WorkCover Connect (Opens in an external website)
- Provider Connect (Opens in an external website)
- High risk work assessor portal (Opens in an external website)
- High risk work applicant/licencee services (Opens in an external website)
- Electrical licensing office course package and online assessment (Opens in an external website)
- Organisational systems benchmarking (Opens in an external website)
- Workers' Compensation Regulatory Services online services (Opens in an external website)
Design considerations
Steps, stairs, ramps, and flooring design and selection can impact on safety. This page has information and advice on design considerations and how to reduce risk and stay safe.
Assess the risk
The areas that have the highest injury rates from slips, trips and falls, and those that require the most careful assessment are:
- entrances from outside and foyer areas
- wet areas and walking surfaces with high levels of contaminants
- steps, stairs and ramps
- thresholds between areas
- areas used by people who are at highest risk of slips, trips and falls given their age, health, mobility restrictions etc.
Some of the key design features to assess in these high risk areas are provided below:
Poorly designed steps and stairs
- stair riser (height) and stair going (depth of tread) measurements not consistent or sufficient
- step nosing (leading edge or front of step) hard to see, rounded, damaged or slippery
- insufficient or poor lighting
- lack of handrails.
Poorly designed ramps
- ramps that are too steep
- ramps with no handrails
- lighting that is insufficient to see edges clearly
- no edging or toe boards.
Poor flooring/ground surface selection
- floor surfaces that lack slip resistance, especially if wet.
Decide on control measures
The design features that have been found to reduce slips, trips and falls are listed below, and detailed guidance is provided in the relevant Australian Standards (e.g. AS 1657 & 1428).
Well-designed steps and stairs
- steps are consistent size and height for secure use
- step nosings (leading edge or front of steps) are clear to see and non-slip
- rails and balustrades are a suitable design and height
- rails are continuous, with sufficient hand clearance
- rails continue past the steps, parallel to the ground or floor surface.
Well-designed ramps
- have a gentle slope
- clearly marked start and finish
- fitted with handrail
- handrails are continuous with sufficient hand clearance
- fitted with toe board or kickboard where required
- suited to the users (e.g. walking unaided, using a wheelchair etc.).
Where ramps may be used by people with mobility restrictions, there is more specific guidance regarding design features including:
- landings at the top and bottom
- unobstructed widths
- no steeper than 1 in 8 for short ramps (up to 1520mm)
- no steeper than 1 in 14 for longer ramps
- fitted with toe board or edging to provide a barrier to wheeled devices.
Well-designed and selected flooring
When selecting flooring and ground surfaces, ensure the most appropriate surface is installed, with particular attention to wet areas and those areas likely to be exposed to contaminants. Assistance can be obtained from:
- flooring suppliers – request comparative data on the slip resistant properties of the flooring options suited to the work tasks, with consideration of wear characteristics; and
- guidance from Standards Australia, such as the 'Guide to the specification and testing of slip resistance of pedestrian surfaces'
- use the table in Flooring types – characteristics & applications to compare characteristics of common types of flooring.
For example, when selecting flooring products, the above guide advises that in addition to slip resistance, people who specify or select flooring should consider these product characteristics:
- trip avoidance
- abrasion resistance
- ability to be cleaned and maintained
- permeability
- susceptibility to pooling water
- structural integrity of the material.
Other important design features
Studies have identified that some additional and often simple design changes will further lower slips, trips and falls risk and these include:
- recessing or rebating structural trip hazards such as door frames on sliding doors, shower hobs, and shower door frames
- designing work flows to be logical and streamlined, as this minimises exposure to potential slips, trips and falls hazards
- providing workstation space that is suited to the typical tasks
- providing storage for all items for workers and others at the workplace (e.g. patients, customers, etc.) to keep items off the floor.
Rate your experience

IMAGES
COMMENTS
Common trip hazards include: • ridges in floors or carpets. • worn floor coverings or broken tiles. • potholes and cracks in floors.
Falls can occur in many different ways including through slips and trips, or falls from height, at level, or into holes or voids. Each year slips, trips and falls cause injuries and fatalities in the construction industry, such as when: Working from height. There is insufficient lighting. Being hit by falling objects.
Slipping, tripping and ultimately falling from any height, can result in short to long-term injuries, even death. A fact sheet on slips, trips and falls and how to minimise them in the workplace. Slips, trips and falls are the most common cause of serious injuries at work in NSW after hazardous manual tasks, with both contributing to ...
Fall hazards are often found where work is undertaken at heights such as: stacking shelves; working on a roof; unloading a large truck; accessing a silo. Falls can also occur at a ground level as a result of a slip or trip or falling into a hole such as a service pit or open hatch.
Falling from one level to another is a major workplace hazard and is the most common cause of death from traumatic injuries in construction. Fall hazards occur in all industries and most fatalities occur from a relatively low height.
Below are some suggestions on how to identify and also control these hazards. Where appropriate, workplace staff should be encouraged to identify any trip hazards and if possible remove them immediately or isolate the area and then report it to key personnel.
Eliminating the hazard creating the risk. Remove slip, trip or fall on the same level hazards at the planning and design stage, or when renovating a facility. Install more power outlets and eliminate split level fl ooring. Substituting the hazard creating the risk with a hazard that gives rise to a lesser risk. Resurface fl oors.
Key requirements for schools to prevent and manage slips, trips and falls. Schools must: consult with school staff and HSRs to identify, manage and prevent slip, trip and fall hazards. identify slips, trips and falls hazards through observation, workplace inspections and incident reports.
Well-designed steps and stairs. steps are consistent size and height for secure use. step nosings (leading edge or front of steps) are clear to see and non-slip. rails and balustrades are a suitable design and height. rails are continuous, with sufficient hand clearance. rails continue past the steps, parallel to the ground or floor surface.