- Mark Forums Read
- Who's Online
- Thanks / Like Statistics
- Hottest Threads / Posts
- Contracting Business
- Advanced Search

- The ARPA Zone/Open Membership Discussion Forums
- Tech to Tech Chat - Commercial

Trane Voyager Troubleshooting Help
- Cookie Consent We use cookies to improve your website experience. To learn about our use of cookies and how you can manage your cookie settings, please see our Cookie Policy . By continuing to use the website, you consent to our use of cookies.
- Gain access to our free AOP (Ask a Professional) Section to get real answers for your questions. All this and much more is available to you absolutely free when you register ; for an account, so join our community today today! We suggest not registering using an AT&T, BellSouth, AOL or Yahoo email address. If you have any problems with the registration process or your account login, please contact support .

- Jump to page:
Thread: Trane Voyager Troubleshooting Help
Thread tools.
- Show Printable Version
- View Profile
- View Forum Posts
- View Forum Threads

Hello everyone, I recently started working on Trane units and Ive been running into a couple of issues. I was working on a train voyager and ran it in test mode. The unit runs perfectly in test mode but as soon as I try to run it by using the thermostat it doesn't work. The only thing that works is the blower motor. This unit in particular has a faded wiring diagram m. Any ideas on what could be the issue or on what I should check? Thanks for any help.

rule the thermostat out first, if that doesn't work look carefully on the back of the reliatel board for dark/burnt resistors or sections
Originally Posted by Dalton92 rule the thermostat out first, if that doesn't work look carefully on the back of the reliatel board for dark/burnt resistors or sections I'll definitely do that. The thermostat I verified is working so I already ruled that out.
How do you know the thermostat is working? Did you verify a heating or cooling call at the rtrm? Did you try jumpering any input at the rtrm to make it run? If it runs when jumpered up there you have a bad thermostat or faulty wiring. Sent from my SM-G930V using Tapatalk
Set the stat for heat. Confirm a visual W1 call by whatever indication shows "heat" on the stat. Sometimes it is the word "heat," and sometimes an icon of a flame, etc. Now, go to the unit and measure voltage at thew W1 terminal of the RTRM board. If you have it, then see if you have voltage to the combustion fan motor.
[Avatar photo from a Florida training accident. Everyone walked away.] 2 Tim 3:16-17 RSES CMS, HVAC Electrical Specialist Member, IAEI AOP Forum Rules: Rules For Equipment Owners. Equipment Owners Find a Contractor HERE! Rules For Professional Members * To get your (*), Click Here. How to become a Professional Member.

Do the Voyager units use that special Trane stat (I forgot what it is called but varies voltage I think). If you use a normal stat you new an interface board? Been a long time since I worked on one of these.
Don't confuse the Microtel board with the Reliable board.
I confirmed voltage at the RTRM. Thermostat is working.
I tried to jump in the unit at the RTRM but that wouldn't work also. The CTI board allows the unit to use any conventional thermostat.
Wouldnt be the first bad CTI board. Sent from my SM-G930V using Tapatalk
If it has an RTRM board then it has Reliatel controls and doesn't require a CTI board. Reliatel control boards have "Trane" terminals 1-12 or so as well as "conventional" terminals R-G-Y-W etc directly on the board. Older Voyager units have Voyager or "black book" controls which require a "CTI" or Conventioal Thermostat Interface board to use a regular 24v stat. Post a pic of what you're working on, it would help greatly.
Saving the world...one service call at a time.

I had a similar issue to this but it was on a UCP not an RTRM. RTRM's have terminals for a conventional thermostat as well as the Trane zone sensor. If you have a conventional thermostat interface I would imagine you have Micro controls and a UCP rather than Reliatel and an RTRM. If it runs in test mode and you verified the thermostat works properly my assumption would be the CTI, is there another RTU you could swap with to verify? Another thing, did you cycle through all the test modes and verify operation? I once had a UCP that wouldn't respond at all to the zone sensor and would run cool in test mode but when I would advance the test to heating mode it would not operate, failed UCP. If you're going to be doing a lot of work on these types of units I suggest you get or make yourself a decade box. Makes life a little easier, especially in winter when you'd rather not be banging compressors on and off.
- Visit Homepage

Did I miss the model # somewhere? Is this a voyager or a prescedent? make sure the machine DOES NOT have a heat & cool call simultanously.
It`s better to be silent and thought the fool; than speak and remove all doubt.
I had that twice this past season. Originally Posted by dandyme Did I miss the model # somewhere? Is this a voyager or a prescedent? make sure the machine DOES NOT have a heat & cool call simultanously.
I do a triple evac with nitro to remove non condensables.
Are there any other similar units on the roof? If so, swap the CTI boards. Rinse and repeat. Originally Posted by Skilleg Hello everyone, I recently started working on Trane units and Ive been running into a couple of issues. I was working on a train voyager and ran it in test mode. The unit runs perfectly in test mode but as soon as I try to run it by using the thermostat it doesn't work. The only thing that works is the blower motor. This unit in particular has a faded wiring diagram m. Any ideas on what could be the issue or on what I should check? Thanks for any help.

If this unit has a CTI board, look at the front of the CTI board and make sure none of the components are leaning over and touching another component. CTI boards parts are soldered very high on the board for some reason and can easily be bent over. I had one that drove me crazy. It was just some capacitor looking thing barely touching another capacitor thing. I bent it back and everything worked.
Dude, I work on Trane RTUs on the daily. I carry 2 RTRM boards on my van at all times. Theyll usually go into test mode fine but wont respond to a call. Sounds like you may have troubleshooting a no heat? Anyway, 9 times out of ten its a failed RTRM board. Make sure theres no alarms present, the green led on the RTRM board should be solid. If its blinking you have an active alarm. There is no diagnostic code and a very convoluted way of measuring voltage at pins and cross referencing them. Its easier to just check the safeties and limits then to try and find what alarm its throwing trust me, call Trane (if your company has a Trane technical service account, if not youre screwed there too). So, if you have a solid green led on the RTRM board and no alarms on the ignition board and 24 Vac coming back to the W1 or Y1 terminal but no operation besides fan. I can almost guarantee its a failed RTRM board. Theyll usually run fine in test mode and other modes theyll just fail in either heat or cool modes. I have a lot of experience with this specific failure to the RTRM boards. They update these boards constantly. I think theyre on version 24 or 25 by now and hopefully your local Trane Supply has them in stock as these boards seem to fail more than any other rtu circuit board out there. If you have to order it and wait you can easily bypass the RTRM board. For cooling take wire from Y1(and Y2 if equipped) to the out wire for each set of pressure switches. For heat just need to take the W ( and W2 if equipped) and connect it to the corresponding heat 1 and 2 wires. This will get you by until a new board arrives but dont leave the unit like this long term. I have never had to bypass RTRM board in heat mode as I live in New Orleans. But you should be pretty easy depending on your experience. Order a few extra RTRM boards if you will continue working on these units. I probably replaced 6-8 in 2018 so far.

He said it had a CTI board so that would rule out a RTRM.

Last edited by VTP99; 10-09-2018 at 05:07 AM .
bump....you get this figured out?
Originally Posted by Dalton92 bump....you get this figured out? Sorry for the late reply reply but it was a faulty CTI board
- Private Messages
- Subscriptions
- Search Forums
- Forums Home
- The #1 question asked by NEW MEMBERS. Please read this...
- Questions About Becoming A Professional Member? Step Inside...
- SITE Software Issues? Post Them Here
- RULES for AOP - Owner Assistance and Contractors
- AOP Residential HVAC (Beenthere Zone)
- AOP Commercial HVAC
- General Discussion
- Job Wanted/Needed Discussion
- Industry and Forum News
- Webinars and Virtual Events
- Tech to Tech Chat - Residential
- Refrigeration & Ice Making
- Members Inventions **NEW
- Test & Balancing Forum NEW
- Control Sales Forum
- Professional Controls Forum
- Control Jobs Forum
- Chillers Open Forum
- Energy Efficiency and Building Performance Discussion NEW
- Commercial Food Service Equipment
- Residential Geo Thermal / Water Source
- Commercial Geo Thermal / Water Source
- Indoor Air Quality
- Tools & Test Equipment
- Food and Grill Forum
- "Wall of Pride" - Pictures
- "Wall of Shame" - Pictures
- How To Become a Pro and Rules For Pro Members
- Pro's Forum: General Discussion
- Charlie's Corner (Icemeister)
- HVAC Basics **NEW
- Pro Forum: Refrigerants and EPA regulations **NEW
- Pro's Forum: Business & Marketing
- Pro Forum: Residential Refrigeration and Appliances **NEW
- Pro's Forum: Sales
- Pro Forum: Equipment Recalls and Bulletins **NEW
- Pro's Forum: Residential
- Pro's Forum: Commercial
- Pro's Forum: Geo Thermal / Water Source
- Pro's Forum: Refrigeration & Ice
- Pro's Forum: Chillers
- Pro's Forum: Oil Burners
- Pro's Forum: Hydronics/Boilers
- Pro's Forum: Building Science Discussions
- Pro's Forum: Training and Education
- Pro's Forum: Instructors Forum NEW
- Pro's Forum: Tips 'n Tricks of the Trade
- Pro's Forum:The Gun Enthusiast
- Frequently Asked Questions About Submissions
- Manufacturers' Technical Information
- Articles Authored by Others
- Self-Authored Articles
- Submit Quiz Questions
- About the Suggestion Box
- Voice Your Opinions
- Share Ideas
- Report Problems
- Educational, Training & Reference Information
- Manufacturer's Technical Information Links
- Quiz Questions
- Open Forum Discussion
- Split Systems, Package Units, Furnaces
- Geothermal / Water Source Heat Pumps
- Specialty Systems
- Boilers Hydronic, Steam
- Accessories Humidifiers, Air Cleaners, HRUs, Fans, Filters, etc
- Components Coils, Heaters, Motors, etc.
- Compressors
- Oil Burners
- Systems - General
- Accessories Pumps, Cooling Towers, Evap Condensers, etc
- Components Valves, Motors, Condensers, Evaporators, etc
- Refrigeration Systems
- Evaporators, Condensers, Etc.
- Valves, Regulators, Filters, Etc.
- Walk-Ins, Cold Storage
- Food Service Equipment, Display Cases
- Supermarket Cases & Compressor Systems
- Ice Machines
- Controls, Motors, Etc
- HVAC Load Calc Software
- Refrigeration Load Calc Software
- HVACR Software & Online Training
- HVACR Calculators & Apps
- Formulas and Calculations
- In Memoriam
- Licensing, Laws, Codes and Certification
- Jokes, Quotations, Humor, Wisdom Pills
- Practice, Testing Area
- Plumbing Forum Rules
- Plumbing General Open Forum
- Pro's Forum: Plumbing Discussion
- Electrical Forum Rules
- Open Discussion Electrical
- Photovoltaic
- New Products
- Bonding & Grounding
- Motors & Motor Controls
- Test & Measurement
- Tools & Equipment
- Code Violations
- Pro's Forum: Power Quality
- Pro's Forum: Calculations & Electrical Theory
- Pro's Forum: Electrical Business & Marketing
- Pro's Forum: Estimating
- Job Postings
vBulletin Message
The following errors occurred with your submission, quick reply, register now.
Please enter the name by which you would like to log-in and be known on this site.
- Confirm Password:
Please enter a password for your user account. Note that passwords are case-sensitive.
- Email Address:
Please enter a valid email address for yourself.
- HVAC/R Contractor
- HVAC/R Technician/Installer
- HVAC/R Wholesaler/Distributor
- HVAC/R Manufacturer
- Manufacturer Rep
- HVAC/R Consultant
- HVAC/R Engineer
- Facilities manager/Mechanical Engineer
- Homeowner or Building/Equipment Owner (We welcome homeowners and Building owners. Help us customize your experience) Please post in the AOP Section
- Residential HVAC
- Light Commercial HVAC (up to 25 tons)
- Commercial HVAC (over 25 tons)
- Refrigeration
- Hydronic Heating
- Building Automation/Controls
Posting Permissions
- You may post new threads
- You may post replies
- You may not post attachments
- You may not edit your posts
- BB code is On
- Smilies are On
- [IMG] code is On
- [VIDEO] code is On
- HTML code is Off
Forum Rules
- HVAC-Talk.com
© VerticalScope Inc. All Rights Reserved.
Smart AC Solutions
Talked About Air Conditioners
Trane Defrost Control Board LED Codes | Solve Common Issue!
If your Trane furnace is equipped with a defrost control board , you can use the LED codes to help troubleshoot any problems that may arise. The most common code is the “red flash” which indicates that the board is in defrost mode.
Other codes include the “green flash” which means that the furnace is operating normally, and the “amber flash” which indicates a problem with the igniter.
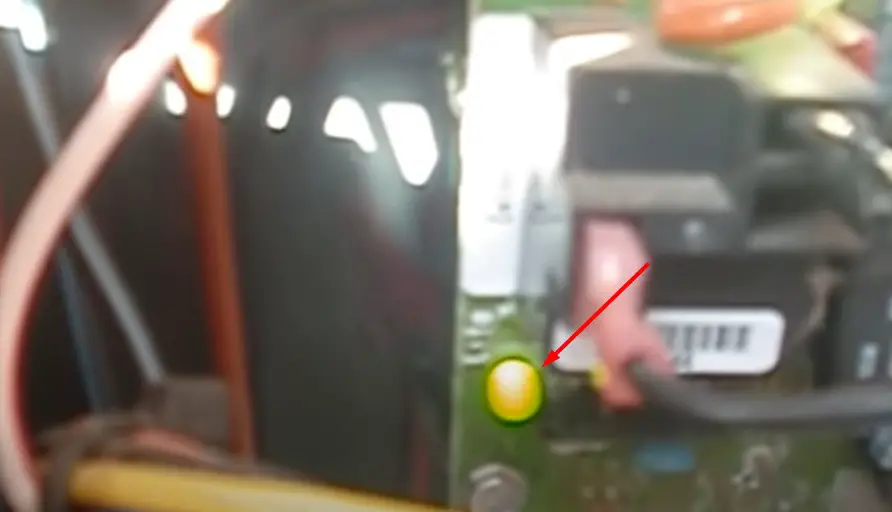
Page Contents
Trane Defrost Control Board LED Codes
The Trane Defrost Control Board is a crucial component of HVAC systems that helps to regulate the defrost cycle, ensuring the efficient functioning of the system. The board is equipped with LED codes that allow troubleshooting and identification of issues that could arise during operation.
The codes and their meanings are as follows:
- Steady Green LED – The system is operating normally.
- Steady Red LED – The defrost control board has detected a fault and is in lockout mode.
- Flashing Red LED – The sensor is not detecting proper temperature, indicating a possible faulty sensor or a wiring issue.
- Flashing Green LED – The system is in defrost mode, and the board is actively monitoring the process.
- Steady On – Power is present
- Flashing Slowly – Normal operation
- Flashing Rapidly – Defrost is active
- Two Flashes – High-pressure switch open
- Three Flashes – Low-pressure switch open
- Four Flashes – Auxiliary limit switch open
- Five Flashes – Outdoor temperature sensor fault
- Six Flashes – Reversing valve fault
- Seven Flashes – Defrost control board fault
Understanding these LED codes is crucial for HVAC technicians to identify and resolve any issues that may arise in the Trane Defrost Control Board.
What are the Codes for a Trane Furnace?
There is no one-size-fits-all answer to this question, as the codes for a Trane furnace will vary depending on the model and year of your furnace. However, you can generally find the code information for your furnace in the owner’s manual or by contacting Trane customer service.
How Do You Test a Trane Defrost Board?
There are a few things that you need to do in order to test a Trane defrost board. The first thing that you will need to do is locate the board. Once you have found the board, you will want to remove it from the unit. Next, you will want to check for any visual damage on the board. If there is any damage, you will want to replace the board. If there is no visual damage, you will then want to connect a multimeter to the board. You will want to set the multimeter to ohms and check for continuity between the two terminals on the board. If there is continuity, then the board is good. However, if there is no continuity, then the board needs to be replaced.
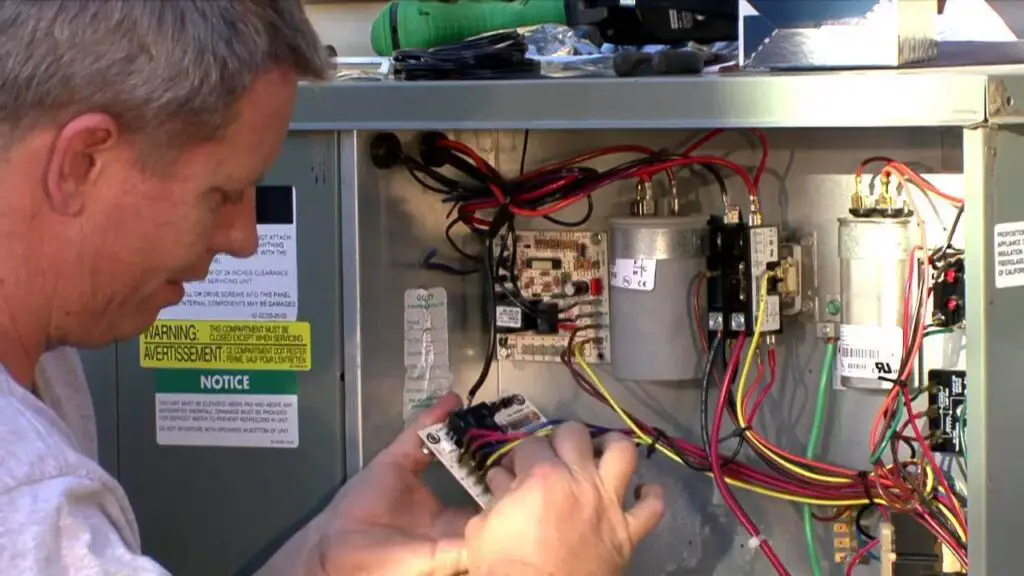
What Causes a Hard Lockout on a Heat Pump?
A hard lockout on a heat pump is caused by a number of different things. The most common cause is when the outdoor temperature drops below the minimum set point for the heat pump. This can be caused by a number of different things, including a cold front moving in, or simply the temperature dropping at night. When this happens, the heat pump will shut off completely in order to prevent damage from happening to the unit. Another common cause of a hard lockout is when the indoor temperature sensor fails. This can cause the heat pump to think that the indoor temperature is too low, even when it isn’t, and as a result, it will shut off. Finally, if there is a problem with the outdoor fan, this can also cause a hard lockout. If the fan isn’t able to turn on, then the heat pump won’t be able to circulate air properly and it will shut down in order to prevent overheating.
What Does Hard Lockout Mean on a Trane Heat Pump?
If your Trane heat pump is locked out, it means that the system has been turned off and can’t be restarted until a qualified technician resets it. This usually happens when the system detects a problem that could cause damage or harm, such as an overheating condition.
Once the problem has been resolved, the lockout can be reset and the heat pump will operate normally again.
Trane 4Twr4 Fault Codes
If you’re a Trane 4TWR4 owner, you know that these units are some of the most reliable and durable on the market. But even the best units can develop faults over time. If your 4TWR4 is displaying a fault code, it’s important to know what that code means so you can take steps to fix the problem. There are four main fault codes that your 4TWR4 may display:
• Code 01: This indicates that there is a problem with the unit’s condenser fan. The most likely cause is a dirty or damaged fan blade. You’ll need to clean or replace the blade to fix this problem.
• Code 02: This indicates that there is a problem with the unit’s evaporator fan. The most likely cause is a dirty or damaged fan blade. You’ll need to clean or replace the blade to fix this problem.
• Code 03: This indicates that there is a problem with the unit’s compressor. The most likely cause is a blown fuse or tripped breaker.
Trane LED Codes
If you have a Trane furnace, you may be wondering what the different LED codes mean. Here is a list of the most common codes and their meanings:
Blinking Green Light: This indicates that the furnace is in standby mode and waiting for a call for heat. Solid Green Light: This means that the furnace is operating normally.
Flashing Red Light : This code indicates that there is an error with the furnace. The specific error will be displayed on the control panel. Consult your owner’s manual for troubleshooting steps.
Continuous Red Light: This means that the limit switch has been activated and the furnace needs to be serviced by a qualified technician.
Trane Furnace Error Codes
Trane furnace error codes are an essential diagnostic tool for identifying issues with your heating system. These codes not only help technicians identify problems quickly but also provide homeowners with the necessary information to troubleshoot issues before calling a professional.
Here are the most common Trane furnace error codes and their meanings:
- 2 flashes: Indicates a problem with the pressure switch.
- 3 flashes: Indicates an issue with the draft inducer motor.
- 4 flashes: Indicates an open limit switch.
- 5 flashes: Indicates a problem with the flame sensor.
- 6 flashes: Indicates an issue with the rollout switch.
- 7 flashes: Indicates a problem with the gas valve.
- 8 flashes: Indicates a problem with Low flame sense signal.
- 9 flashes: Indicates a problem with Igniter.
By familiarizing yourself with these codes, you’ll be better equipped to handle any furnace issues that arise.
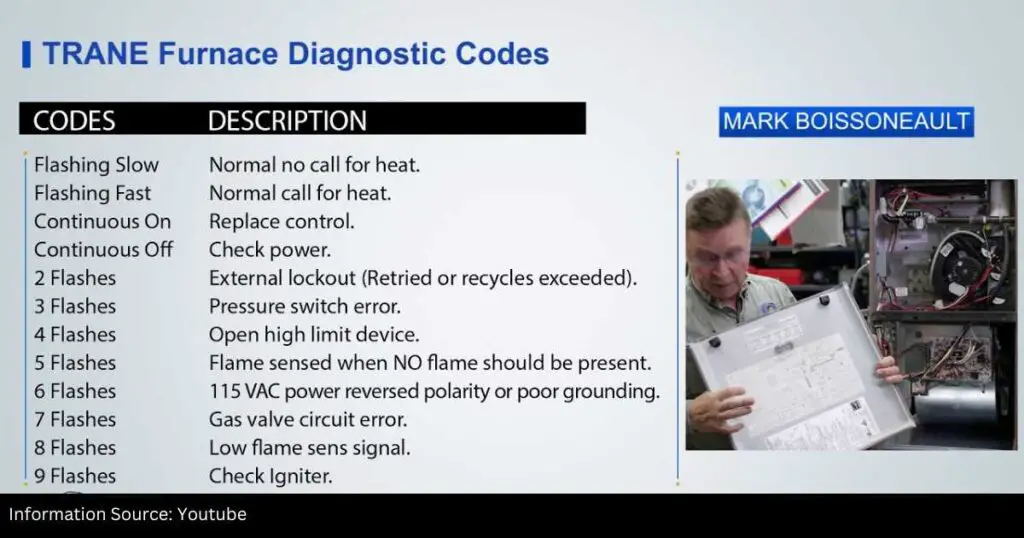
Besides the above, you may also find the following error codes for Trane Furnace:
- 126: Internal control fault
- 131: Ignition failure
- 132: Flame sensor failure
- 133: Limit circuit fault
- 147: Low flame signal
- 151: Blower motor fault
- 161: AC power loss
- 164: Open high-limit device
These error codes can help a technician quickly identify the issue and provide a solution, ensuring that your Trane furnace runs smoothly and efficiently.
Trane Troubleshooting Guide
If your Trane unit isn’t working properly, you may be able to troubleshoot and fix the problem yourself. This Trane Troubleshooting Guide will help you identify common issues and provide solutions. First, check the thermostat to make sure it is set correctly. If the thermostat is set too low, the unit won’t run. If the thermostat is set too high, the unit will run continuously without cooling the home. Next, check for power failures. The circuit breaker may have tripped or a fuse may have blown. Reset the breaker or replace the fuse and see if that fixes the problem. If your unit still isn’t running, there could be an issue with the actual unit itself. First, check to see if there is debris blocking the air intake or exhaust vents. If so, remove the debris and try again. Next, check for freezing coils. Ice can build up on the coils and prevent proper airflow. Turn off your unit and let it thaw for several hours before restarting it again. Finally, if all else fails, call a professional for assistance.
Trane Air Handler Blinking Lights
If you have a Trane air handler in your home, you may have noticed that the lights on the unit are blinking. While this may be alarming at first, it’s actually a normal part of the unit’s operation. The blinking lights indicate that the air handler is in standby mode and is waiting for a command from the thermostat. Once the thermostat tells the air handler to start, the lights will stop blinking and the unit will begin heating or cooling your home as needed.
Trane Voyager Error Codes
If you’re getting error codes on your Trane Voyager, it means there’s a problem with the unit. Here are some common error codes and what they mean:
E01 – This indicates that the evaporator temperature is too high. Check to make sure that the coils are clean and that the air filter isn’t clogged.
E02 – This code means that the condenser temperature is too high. Again, check the coils and air filter. Make sure the unit has proper ventilation.
E03 – The third code stands for “freeze protection.” This means that the unit is sensing a potential for freezing temperatures and is shutting down to prevent damage. Check your thermostat settings and make sure the unit is in heating mode. If it still doesn’t work, call a technician. These are just a few of the most common Trane Voyager error codes . If you’re experiencing problems with your unit, don’t hesitate to call a technician or reference your owner’s manual for more information.
Trane Ac Blinking Green Light
If you have a Trane air conditioner , you may have noticed that the green light is blinking. This is normal and indicates that the unit is in standby mode. The green light will blink when the unit is first turned on, and then it will remain lit when the unit is running. If the green light starts blinking again, it means that the unit has been turned off and is in standby mode once again.
Trane Eev Control Board Troubleshooting
If you have a Trane EEV control board that is giving you trouble, there are some things you can do to troubleshoot the problem. First, check all of the connections to make sure they are tight and secure. Next, check the circuit breaker to see if it has tripped. If neither of these solutions solves the problem, you may need to replace the control board.
Heat Pump Defrost Board: Diagnostic Procedures
The Trane Defrost Control Board is responsible for managing the defrost cycle of your Trane AC unit. If there is a problem with the board, it will display an error code on the LED display.
This article lists the codes and what they mean, so you can troubleshoot the issue and get your AC unit up and running again.
Related Articles:
- Mitsubishi Msz-Fh12Na Troubleshooting | Solve Common Issues
- Carrier APU AC Not Working: Identify and Fix the Issue!
- P6 Error Code on Your Air Conditioner
- Trane Ac Unit Fan Not Spinning
My name is Aris, and I am a certified HVAC technician. I have been working in this field for over 5 years and have a lot of experience with different AC units. I write here to help people solve their Air Conditioning problems and find the best solutions for their needs.
If you are having any issues with your air conditioner or are thinking about buying a new one, be sure to check out my blog!
Leave a Reply Cancel reply
Your email address will not be published. Required fields are marked *
Save my name, email, and website in this browser for the next time I comment.
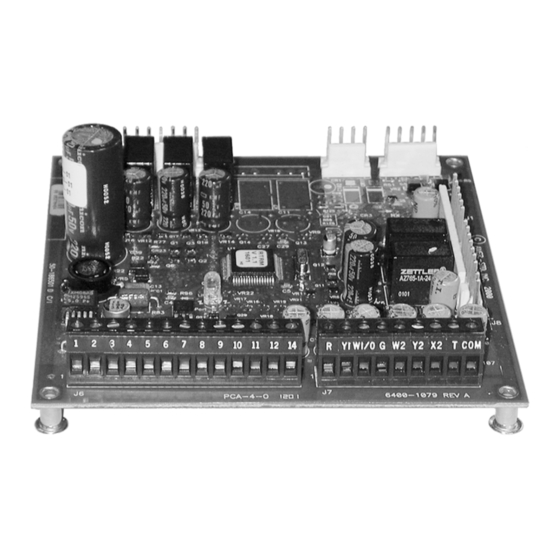
- Trane Manuals
- Diagnostic manual
Trane ReliaTel Diagnostic Manual
- Installation manual (29 pages)
- page of 168 Go / 168
Table of Contents
Troubleshooting.
- Introduction
- Reliatel Introduction
- General Information
- Reliatel Vs. Electromechanical
- Reliatel - Module Descriptions
- Module Flow Diagram
- Low Voltage Terminal Strip
- Typical Control Box Layout
- Reliatel Refrigeration Module (RTRM)
- RTRM Diagnostics
- 27½ to 50 Ton Unit Additional Diagnostics (VAV Only)
- Default Operations
- Reliatel Option Module (RTOM)
- RTOM Layout
- RTOM Inputs
- Setpoint Potentiometers
- Reliatel Ventilation Module (RTVM)
- RTVM Layout
- RTVM Inputs
- Reliatel Dehumidification Module (RTDM)
- RTDM Layout
- RTDM Inputs
- Verifying Proper Air Flow
- Units with Direct Drive Indoor Fan with MMC
- Reliatel LED Functions
- Green System LED
- Green Transmit LED
- Yellow Receive LED
- Reliatel Options Module (RTOM)
- Reliatel Air Handling Module (RTAM)
- Economizer Actuator Module (ECA)
- Ignition Control (IGN)
- TCI COMM3/4 Interface (Tracer, Varitrac)
- Yellow RX (Receive) LED
- Green TX (Transmit) LED
- LCI (Lontalk)
- LED1 Green MODBUS LED
- LED4 Green LCI Status LED
- LED2 Red Service LED
- LED3 Yellow Comm RX
- Reliatel Test Mode
- Protocol of Communications
- Service Test Mode
- Auto-Cycle Test
- Resistance Test
- Service Tips
- Thermostats and Sensors
- High Temperature Sensor Diagram
- Operation with a Conventional Thermostat (Constant Volume)
- Zone Sensor Module Testing
- Mechanical Zone Sensor Module
- Temperature Input
- Setpoint Input
- Programmable Zone Sensor BAYSENS119A and BAYSENS019C (Obsolete)
- RTRM/RTOM (Temperature Inputs)
- Outdoor Air Sensor, Discharge Air Sensor, Coil Temperature Sensor
- Zone Sensor Averaging
- COMM3/4 Interface Operation & Troubleshooting
- Communication Problems
- Direct Spark Ignition Control (Texas Instruments, 3-10 Ton Units Only)
- Direct Spark Ignition Control (Sequence of Operation, 3-10 Ton Units Only)
- 1-Stage Units
- Reliatel Hot Surface Ignition Control (12.5 - 50 Ton 1 Stage, 2 Stage, and Mod- Ulating Gas Heat)
- Ignition Control Module Diagnostics
- Sequence of Operations (1 and 2 Heat Units)
- Heat Pump Demand Defrost
- Defrost Service Test
- Defrost Mode Operation
- Sequence of Operation
- Emergency Heat Operation
- Diagnostic Information
- Independent Circuit Defrost Operation
- Reliatel Economizer Module Layout (Honeywell)
- Reliatel Economizer Layout (RTEM)
- Reliatel Economizer Actuator Layout
- Reliatel Economizer Operation
- Customer Benefit
- VAV Economizer Cooling Operation
- Economizer Operation with Zone Sensor, Programmable Zone Sensor or ICS
- Economizer Operation with Conventional Thermostat (CV Only)
- Barometric Relief
- Power Exhaust
- Economizer Control Methods
- Thermostat Notes
- Economizer Damper Enthalpy Layout
- Economizer Operation Enthalpy Changeover
- Dry Bulb/Reference Point Selections
- Comparative Enthalpy Method
- Reference Enthalpy Method
- Reference Dry Bulb Method
- Internal Calculations
- Reliatel Economizer Operation & Inputs
- Reliatel Economizer Inputs
- Economizer Actuator Module W7340A1004 (Used Prior to 08/1/05)
- Economizer Actuator Module W7340B1002 (08/01/05 and Later)
- Reliatel Economizer Control Actuator (LED Fault Code Info.)
- Actuator Fault (Honeywell)
- Actuator Fault (RTEM)
- Sensor Faults
- Reliatel Humidity Sensors
- To Test Humidity Sensors
- Space Pressure Control with Statitrac (27.5-50 Tons)
- Description of Function
- Exhaust Fan Control
- Sensor and Setpoint Arbitration
- Space Pressure Zero Function
- Exhaust Damper Output Control
- Failure and Override Modes of Operation
- Electromechanical Economizer Functions
- Electromechanical Economizer Testing
- Electromechanical Mixed Air Sensor
- Electromechanical Economizer (3 Position Damper)
- Reliatel Control Temporary Operation 3-25 Tons
- Reliatel Supply Air Tempering Control
- Enable Supply Air Tempering
- Constant Volume Units with Staged Heat
- Variable Air Volume Units
- Discharge Air Sensing with TCI Comm3/4
- 3-25 Ton Units
- 27.5-50 Tons Units
- CO Sensor Connections
- (Reliatel Units with Demand Controlled Ventilation)
- Demand Controlled Ventilation (DCV)
- RTEM Operation
- RTEM W/ RTRM V8.0 and Later
- RTEM W/ RTRM V7.0 and Earlier
- Honeywell Operation
- Voyager 27.5 - 50 Tons VAV Notes
- Reliatel Ventilation Override
- Dehumidification with Hot Gas Reheat (3-25 Tons)
- Sequence of Events
- Modulating Dehumidification with Hot Gas Reheat (27.5-50 Tons)
- Controls Overview
- Heating/Cooling Changeover
- Low Ambient Mechanical Cooling Operation (3-25 Ton Units)
- Evaporator Defrost Control (EDC) Function
- Reliatel Condenser Fan Control Logic
- 12.5 - 25 Ton
- Condenser Fan Sequencing Control
- Odyssey Independent Circuit Heat Pump Condenser Fan Control
- Phase Monitor
- 3 - 25 Ton Reliatel Units
- Electromechanical Time Delay Relay
- Time Delay Relay
- Fan "Off" Delay Solid State Timer
- Snubber Circuits
- Transformer Troubleshooting
- High Pressure and Low Pressure Lockout Circuits
- LPC Sequence of Operation
- LPC Operation for 27.5-50T Units with Modulating Reheat
- HPC Sequence of Operation
- Novar Controls (Sequence of Operation)
- Cooling with an Economizer
- Cooling Without an Economizer
- Economizer Set-Up
- Novar Controls Checkout/Troubleshooting Procedure
- Checkout Procedure
- Voyager Commercial 27½ to 50 Tons CV and VAV
- Constant Volume (CV)
- Variable Air Volume (VAV)
- RTRM - Reliatel Refrigeration Module - (Standard)
- RTOM - Reliatel Options Module - (Standard)
- RTAM - Reliatel Air Handler Module - (Standard on VAV)
- ECA - Economizer Actuator - (Optional)
- TCI - Trane Communication Interface - (Optional)
- LCI - Lontalk Communication Interface (Optional)
- IGN - Ignition Control Module (YC* Only)
- Configuration Input
- Supply Duct Static Pressure Control
- Modes of Operation
- Troubleshooting Tips
- Application Notes
- BAYSENS021A Setpoint Input
- Remote Setpoint Inputs on RTAM J7
- Outdoor Air Flow Compensation for VAV Units
- Outdoor Airflow Compensation (27½ - 50 Ton VAV Only)
- Operation for RTRM 8.0 and Later with RTEM
- Software Change History
Advertisement
Quick Links
- 1 Low Voltage Terminal Strip
- 2 Reliatel Refrigeration Module (Rtrm)
- 3 Rtrm Diagnostics
- Download this manual
- COMM3/4 Interface Operation & Troubleshooting 86
- Transformer Troubleshooting 138
- Economizer Set-up 143
- Troubleshooting Tips 152
Related Manuals for Trane ReliaTel

Summary of Contents for Trane ReliaTel
- Page 1 Diagnostic Manual ReliaTel™ Microprocessor Controls RT-SVD03G-EN November 2010...

Page 2: Introduction
Page 3: table of contents.
- Page 4 ReliaTel Air Handling Module (RTAM) ....... 45 Green system LED ..........45 ReliaTel Dehumidification Module (RTDM) .
- Page 5 2-stage units ..........89 ReliaTel Hot Surface Ignition Control (12.5 - 50 Ton 1 Stage, 2 Stage, and Mod- ulating Gas Heat) .
- Page 6 ReliaTel Economizer Inputs ........106 Economizer Actuator Module W7340A1004 (used prior to 08/1/05) . . . 106 Service Tips .
- Page 7 ............135 3 – 25 Ton ReliaTel Units .
- Page 8 RTRM - ReliaTel Refrigeration Module - (standard) ....146 RTOM - ReliaTel Options Module - (standard) ....147 RTAM - ReliaTel Air Handler Module - (standard on VAV) .
Page 9: General Information
- Page 10 VariTrac™ 1 (Comfort Manager) • VariTrac™ 2 (Central Control Panel) LonTalk® Communication Interface Allows Building Management System (BMS) communication to a ReliaTel unit. There are 2 LCI versions, one for SCC control (constant volume units) and one for DAC control (VAV units). RT-SVD03G-EN...
Page 11: Module Flow Diagram
- Page 12 Module Flow Diagram RTRM Figure 2. Refrigeration Module (RTRM) Gas Heating Unit Control, Select one YS/H Refrigeration Module 4 Zone Sensor Inputs (AIP) Gas Heat Zone Sensor Module 4 Outputs 1200 BPS Comm Mechanical (IGN) LED or indications Non Heat Pump Config (BIP) 1 Compressor Config (BIP) Thermostat G Y1 Y2 W1...
- Page 13 Module Flow Diagram RTRM Figure 3. Refrigeration Module (RTRM) Heat Pump Unit Control, Select one WS Refrigeration Module 4 Zone Sensor Inputs (AIP) Zone Sensor 4 Outputs Mechanical LED or indications No Electric Heat Configuration (BIP) (open when heaters installed) 1 Stage Electric Heat Config.
- Page 14 Module Flow Diagram RTOM Figure 4. Options Module (RTOM) Refrigeration Module Options Module Economizer Modbus Communication Actuator Module 24 VAC Voyager 3 Configuration Condenser Fan Cycling (27 .5 - 50 ton) Modulating Gas Heat Configuration Supply Air Tempering Config (BIP) Heat Pump Low Ambient Limit Config.
- Page 15 Module Flow Diagram Figure 5. Honeywell Economizer Module (ECA) Honeywell Economizer Module Power Exhaust Refrigeration relay Module ModBus Communication 24 VAC Status LED 24 VAC Enthalpy/Temperature Setpoint Pot. 0-50% Minimum Position Pot. Setpoint Adjustment (500-1500 ppm) MA Sensor Mixed Air Temp (AIP) 10K 25C Neg Coeff RH Sensor Return Air Relative Humidity (AIP)
- Page 16 Module Flow Diagram RTEM Figure 6. Economizer Module (RTEM) ReliaTel Economizer Module DCV Mode Power Exhaust Refrigeration relay Module ModBus Communication 24 VAC Status LED 24 VAC 24 VAC DCV Min Pos 0-40/50% Design Min Pos 0-10/50% Enthalpy/Temperature Setpoint Pot.
- Page 17 Module Flow Diagram LCI/TCI Figure 7. COMM 3/4 Module for ICS Communication/ LonTalk Communication Interface (LCI/TCI) Refrigeration Module Options COMM 3/4 Module/LCI Module Modbus Communication 24 VAC RTAM (VAV) Must be configured for COMM3 or COMM4 depending on input device. LCI is self-configured.
- Page 18 Module Flow Diagram RTAM Figure 8. Air Control Module (RTAM) Options TCI/LCI RTAM Module Module Refrigeration Static Pressure Setpoint Module Static Pressure Deadband VAV Box Relay Reset Remote Static Setpoint Pressure Setpoint Reset Duct Static Pressure Transducer Remote Static Amount Pressure Deadband Morning Remote Reset...
- Page 19 Module Flow Diagram RTVM Figure 9. ReliaTel Ventilation Module (RTVM) Options Module Ventilation Module Modbus Communication 24 VAC Statitrac Config Exhaust Damper Output Bldg. Pressure Transducer Calibration Output Bldg. Pressure Transducer Bldg. Pressure Setpoint Bldg. Pressure Setpoint Deadband RT-SVD03G-EN...
Page 20: Low Voltage Terminal Strip
Page 21: typical control box layout.
- Page 22 Typical Control Box Layout Figure 13. Typical Control Box Layout (T/YSC072-102E, T/YHC048-072E, & WSC060-090E) Ignition Module (IGN) ReliaTel Refrigeration Module (RTRM) TCI (COMM3/4) or LCI Interface Fan Relay Compressor Contactors Inducer Transformer (460/575 only) OD Fan Capacitor Zone Sensor or...
- Page 23 Typical Control Box Layout Figure 14. Typical Control Box Layout (T/YSC120E, T/YHC092-120E, & WSC120E) RT-SVD03G-EN...
- Page 24 Typical Control Box Layout Figure 15. Typical Control Box Layout (12½ - 25 tons) Ignition Module Fan Relay Compressor Contactors RTOM (Options Module) RTRM (Refrigeration Module) Zone Sensor or Thermostat Connections TCI (or LCI) Communication Module 24 VAC Control Transformer Low Voltage Terminal Block Test Terminals...
Page 25: Reliatel Refrigeration Module (Rtrm)
Page 26: rtrm diagnostics.
- Page 27 ReliaTel Refrigeration Module (RTRM) Froststat Active Outdoor Air Temperature Sensor Failure Smoke Detector Active Entering Evaporator Temp. Failure (On Modulating Reheat Units) RTOM Comm. Failure RTDM Comm. Failure (On Modulating Reheat Units) RTVM Comm. Failure Space Pressure Sensor Failure Dehumidification Mis-Configuration Reheat Circuit Entering Evaporator Temperature Failure 27½...
- Page 28 ReliaTel Refrigeration Module (RTRM) Service Diagnostic What the readings mean Service- RTRM-J6-10. ON - Clogged filter switch has been closed for at least 2 minutes, indicating a clogged filter. This example illustrates what would be seen if the unit did not have a zone sensor with indicator LEDs, such as would be the case with an ICS system.
- Page 29 ReliaTel Refrigeration Module (RTRM) System Diagnostic What the readings mean System- RTRM-J6-9. ON – System is powered up. This output should be on whenever the green RTRM System LED is on. Incidentally, this LED may flicker as part of its normal function on older version boards.
- Page 30 ReliaTel Refrigeration Module (RTRM) Cool Diagnostic What the readings mean Cooling-RTRM-J6-8. ON – System is in the cooling mode and actively cooling. The unit could be economizing or have one or both compressors on. If the unit is a heat pump, the reversing valve is energized as well.
- Page 31 ReliaTel Refrigeration Module (RTRM) Heat Diagnostic What the readings mean Heating-RTRM-J6-7. ON – System is actively heating. OFF – System is not actively heating. PULSING – See below: Gas heat If any failure occurs such as loss of flame, limit switch trip, flame rollout etc, this indication is present.
- Page 32 ReliaTel Refrigeration Module (RTRM) Heat Fail - Cool Fail Diagnostic What the readings mean HEAT FAIL and COOL FAIL at the same time, RTRM-J6-7 & 8 pulsing voltage: 1. Coil temperature sensor is open or shorted. (Heat Pump) 2. Unit has failed to defrost properly. See Heat Pump section for further details.
Page 33: 27½ To 50 Ton Unit Additional Diagnostics (Vav Only)
Page 34: default operations.
- Page 35 ReliaTel Refrigeration Module (RTRM) Note: Version 1.1 and 1.3 RTRM do not provide Heat, Cool, Service, Cool Fail, Heat Fail indications for Programmable ZSM. Later versions (with a higher number) do. COMM3/4 and COMM5 Communication Interface Module use MODBUS communication directly with the RTRM.
Page 36: Reliatel Option Module (Rtom)
Page 37: rtom inputs, page 38: setpoint potentiometers.
- Page 39 ReliaTel Option Module (RTOM) Table 7. RTOM Discharge Air Heat Setpoint Voltage (Vdc) Setpoint (ºF) Voltage (Vdc) Setpoint (ºF) Voltage (Vdc) Setpoint (ºF) 0.00 1.46 2.23 0.09 1.48 2.24 0.13 1.51 2.25 0.16 1.53 2.26 0.20 1.56 2.28 0.24 1.58 2.29...
- Page 40 ReliaTel Option Module (RTOM) Table 8. RTOM Supply Air Reheat Setpoint Voltage (Vdc) Setpoint (ºF) Voltage (Vdc) Setpoint (ºF) 0.002 1.683 0.169 65.5 1.766 73.5 0.317 1.822 0.395 66.5 1.887 74.5 0.552 1.940 0.672 67.5 1.998 75.5 0.785 2.064 0.915 68.5...
Page 41: Reliatel Ventilation Module (Rtvm)
Page 42: setpoint potentiometers, page 43: reliatel dehumidification module (rtdm), page 44: verifying proper air flow, page 45: reliatel led functions, page 46: reliatel dehumidification module (rtdm), page 47: tci comm3/4 interface (tracer, varitrac), page 48: reliatel test mode, page 49: resistance test, page 50: test mode.
- Page 51 ReliaTel Test Mode ECA Minimum Position Adjustment During the economizer step (step 2 of test mode), the "Min pos" on the ECA Module is disabled. It can only be adjusted during step 1 of the test when the fan is on.
- Page 52 ReliaTel Test Mode Table 14. Odyssey Independent Circuit Heat Pump Units 15-20 Ton Step Mode Econ CPR1 CPR2 SOV 1 SOV 2 ODM1 ODM2 Fan On Econ. Open Cool 1 Cool 2 Heat 1 Heat 2 Heat 3 Heat 4 Defrost Em.
- Page 53 ReliaTel Test Mode Table 16. Voyager Commercial VAV Service Test with Reheat and Statitrac COOL IN CON- STAGE ON(5) ON(6) 100% OFF(8) TROL COOL IN CON- ON(4) STAGE ON(5) OFF(4) 100% ON(8) TROL COOL IN CON- STAGE ON(6) ON(6) 100%...
- Page 54 ReliaTel Test Mode Table 18. CV Test modes 27 ½ - 50 Ton with Reheat POWER COOL REHEAT TEST ECON DAMPER HEAT HEAT VALVE REHEAT PUMP STEP MODE COMP 1 COMP 2 HEAT* VALVE* OUT* OHMS MINIMUM VENTILA 100% 2.2k...
Page 55: Thermostats And Sensors
- Page 56 Thermostats and Sensors Table 19. Thermostat and Sensor Descriptions Required # Accessory Model # Zone Sensor Module Description Conductors Terminal Connections at J6 Heat/Cool BAYSENS106* Single Set Point 1,2,3,4 ASYSTAT106* Manual change Over BAYSENS108* Dual Set Point 1,2,3,4,5 Manual/Auto Change Over BAYSENS110* Dual Set Point with LEDs Manual/Auto 1,2,3,4,5,6,7,8,9,10...
- Page 57 Thermostats and Sensors BAYSENS006B/ASYSTAT661B (obsolete) Accessory Heat / Cool Zone Sensor Module (ZSM) single set point, manual change over. Figure 23. BAYSENS006B/ ASYSTAT661B layout Component Description BAYSENS006B ASYSTAT661B BAYSENS007B/ASYSTAT662B (obsolete) Accessory Heat Pump Zone Sensor Module (ZSM), single set point, manual change over. Figure 24.
- Page 58 Thermostats and Sensors BAYSENS008B/ASYSTAT663B (obsolete) Accessory Heat / Cool Zone Sensor Module (ZSM), dual set point, manual / auto change over. Figure 25. BAYSENS008B/ASYSTAT663B Component Description BAYSENS008B ASYSTAT663B BAYSENS009B/ ASYSTAT664B (obsolete) Accessory Heat Pump Zone Sensor Module (ZSM), dual set point, manual/ auto changeover. Figure 26.
- Page 59 Thermostats and Sensors BAYSENS010B (obsolete) Accessory Heat / Cool Zone Sensor Module (ZSM), dual set point with LEDs, manual/ auto change over. Figure 27. BAYSENS010B Layout Component Description BAYSENS010B BAYSENS011B (obsolete) Accessory Heat Pump Zone Sensor Module (ZSM), dual set point with LEDs, manual/ auto changeover.
- Page 60 Thermostats and Sensors BAYSENS013C (obsolete) Accessory ICS (Tracer/Tracker/ComforTrac) Zone Sensor Module (ZSM), with override button, and override cancel button. Figure 29. BAYSENS013C Layout Component Description BAYSENS013C BAYSENS014C (obsolete) Accessory ICS (Tracer/Tracker/ComforTrac) Zone Sensor Module (ZSM), with override button, set point, and override cancel button. Three conductors required. Manufactured by Sunne, introduced 08/ 95.
- Page 61 SAS, RAS, CTS) Outdoor Air Sensor: Located in the condenser section, lower left corner. The compressor access panel has a slotted opening to provide airflow across the sensor. Standard with all ReliaTel controlled units. Return Air Sensor: Field or factory installed accessory. Located on the return air damper of the economizer, used with comparative enthalpy control only.
- Page 62 Thermostats and Sensors BAYSENS019*/ASYSTAT666* (CV 3-50 Ton) (Obsolete) Accessory Heat/Cool, programmable night set back Zone Sensor Module (ZSM), with LCD status / diagnostic indicators. Figure 33. Programmable night set back Sensor Module (ZSM) PROGRAM TIME MODE HEAT COOL COOL OCCUPIED ERASE AUTO ROOM TEMP...
- Page 63 Thermostats and Sensors BAYSENS0032A (CV 3-50 Ton) (obsolete) Accessory Averaging, Remote Zone Sensor, Dual Thermistors, Two conductors required. Figure 35. BAYSENS0032A Layout Component Description BAYSENS032A BAYSENS035A/AYSTAT709A (Obsolete) Accessory Digital Heat/Cool Zone Sensor Module (ZSM), Dual SetPoint, Manual/Auto Changeover. Figure 36. BAYSENS035A/AYSTAT709A Layout Component Description BAYSENS035A ASYSTAT709A...
- Page 64 Thermostats and Sensors BAYSENS106*/ASYSTAT106* Accessory Heat / Cool Zone Sensor Module (ZSM) single set point, manual changeover. Four conductors required. Figure 37. BAYSENS106A/ASYSTAT106A RT1 thermistor, Zone 10 k at 25°C R11, zero temperature Signal common Note 1: Temperature Calibration Pot 1 is setpoint Cool setpoint (CSP) Pot 1 (see...
- Page 65 Thermostats and Sensors BAYSENS108A/ASYSTAT108A Accessory Heat / Cool Zone Sensor Module (ZSM) dual set point, manual / auto changeover. Five conductors required. Figure 39. BAYSENS108A/ASYSTAT108A RT1 thermistor, Zone R11, zero 10 k at 25°C temperature 1 Signal common Calibration Note 1: Cool setpoint Cool setpoint (CSP) Pot 1 (see...
- Page 66 Thermostats and Sensors BAYSENS110A Accessory Heat / Cool Zone Sensor Module (ZSM) dual set point with LEDs, manual / auto changeover. Ten conductors required. Figure 41. BAYSENS110A RT1 thermistor, Zone 10 k at 25°C R9, zero temperature Signal common Note 1: Calibration Pot 1 and Cool setpoint...
- Page 67 Thermostats and Sensors BAYSENS073A Accessory ICS (Tracker/Tracer) Zone Sensor Module (ZSM), with override button, and override cancel button. Two conductors required. Figure 43. BAYSENS073A R1, 1.5K OHM Timed Override On SW1 Zone Temperature Timed Override RT1 thermistor, Cancel SW2 10K OHM AT 25 DEG C Signal Common Part Number –...
- Page 68 BAYSENS019C but also has improved thermistors that increases sensing accuracy and is still compatible with all equipment using either UCP or Reliatel micro controls. The BAYSENS119A can be used with VAV, constant volume or heat pump equipment.
- Page 69 Table 20. Programmable zone sensor wiring diagram 3–25 ton packaged 3–20 split 27.5–50 ton packaged rooftops system units rooftops *CD/*CH/*SC/*HC TTA/TWA YC*/TC*/TE* control ReliaTel ReliaTel Control control ReliaTel Sensor Control J6 LTB1 Control J6 REMOTE SENSOR Optional remote sensor INPUT REMOTE SENSOR Optional remote sensor...
- Page 70 Thermostats and Sensors Error Codes An error code indicates that technical assistance may be required. Note: On the display, error codes toggle with the clock. Heat failure Indicates that there is an error in the heating system. Cool failure Indicates that there is an error in the cooling system. Test mode Indicates that the system is operating in test mode.
- Page 71 Thermostats and Sensors Table 21. Reliatel and UCP wiring locations Feature Reliatel RTRM terminal UCP LTB screw description BAYSENS135A block (J6) position terminal position Zone temperature 5 volt common cooling setpoint System/Fan Mode Heating setpoint 6 (not used) COMM+ 7 (not used)
- Page 72 Thermostats and Sensors Error Codes Main processor error Replace sensor. Software version conflict Replace sensor. Communication error Replace sensor. Temperature input outside valid Replace sensor if space temperature is operating range (32ºF–122ºF [0ºC–50ºC]) within valid range. Lock Symbol Indicates that the keypad is locked The lock symbol appears if you try to adjust a setting that cannot be changed.
Page 73: High Temperature Sensor Diagram
Page 74: operation with a conventional thermostat (constant volume).
- Page 75 Operation with a Conventional Thermostat (Constant Volume) Table 22. Thermostat signals 24VAC power to thermostat Call for compressor 1 or first stage cooling Call for compressor 2 or 2 stage cooling Call for supply fan Call for heat 1 (for modulating gas, see Figure 50, p.
- Page 76 Operation with a Conventional Thermostat (Constant Volume) a field applied time clock with relay contacts connected to J6-11 and J6-12 can initiate an unoccupied mode as follows: Contacts open: Normal occupied operation. Contacts closed: Unoccupied operation as follows - Fan in auto mode regardless of fan switch position.
- Page 77 Operation with a Conventional Thermostat (Constant Volume) Figure 50. Modulating Gas Heat Control Process RT-SVD03G-EN...
Page 78: Zone Sensor Module Testing
Page 79: setpoint input, page 80: mode input, page 81: programmable zone sensor baysens119a and baysens019c (obsolete).
- Page 82 Zone Sensor Module Testing Table 30. Troubleshooting Symptom Probable Cause and solution Display does not come on. Check for 24 vac on terminals 11 and 12 of the sensor. Verify a varying voltage per step 2 of testing the sensor. If no No communication with unit.
Page 83: Rtrm/Rtom (Temperature Inputs)
- Page 84 RTRM/RTOM (Temperature Inputs) Table 31. Temperature Input (continued) Temp Resistance Temp Resistance Temp Resistance Temp Resistance °F (K ohms) DC Volts °F (K ohms) DC Volts °F (K ohms) DC Volts °F (K ohms) DC Volts 25.383 3.585 8.206 2.253 3.104 1.185 1.331...
Page 85: Zone Sensor Averaging
Page 86: comm3/4 interface operation & troubleshooting.
- Page 87 COMM3/4 Interface Operation & Troubleshooting Won’t communicate with Tracer SUMMIT: • Harness, labeled 4366-1151, must be plugged into RTRM correctly – see above. • Com Link board must be in “NON ISOLATED COMM3 or COMM4” position. If it is in the wrong position or not installed, the unit will not communicate.
Page 88: Direct Spark Ignition Control (Texas Instruments, 3-10 Ton Units Only)
Page 89: direct spark ignition control (sequence of operation, 3-10 ton units only), page 90: reliatel hot surface ignition control (12.5 - 50 ton 1 stage, 2 stage, and mod- ulating gas heat), page 91: sequence of operations (1 and 2 heat units).
- Page 92 ReliaTel Hot Surface Ignition Control (12.5 - 50 Ton 1 Stage, 2 Stage, and Modulating Gas Heat) Modulating heat units utilize a variable speed combustion blower motor that enables the motor to operate at the necessary speed required to provide the amount of heat required to satisfy the current heating load of the building.
Page 93: Heat Pump Demand Defrost
Page 94: sequence of operation, page 95: independent circuit defrost operation, page 96: reliatel economizer module layout (honeywell), page 97: reliatel economizer layout (rtem), page 98: reliatel economizer actuator layout, page 99: reliatel economizer operation, page 100: economizer operation with zone sensor, programmable zone sensor or ics, page 101: power exhaust.
- Page 102 ReliaTel Economizer Operation • Night Setback — During NSTS, the damper drives to full closed position. If there is a call for cooling, the damper opens to satisfy the cooling requirement. The damper stays closed during heating mode. During unoccupied mode, the minimum position is 0%...
Page 103: Economizer Damper Enthalpy Layout
Page 104: economizer operation enthalpy changeover, page 105: reference dry bulb method, page 106: reliatel economizer operation & inputs, page 107: economizer actuator module w7340b1002 (08/01/05 and later), page 108: reliatel economizer control actuator (led fault code info.), page 109: reliatel humidity sensors.
- Page 110 ReliaTel Humidity Sensors ECA Module Voltages W7340A1004 (Production part prior to 8/1/2005) - 20.0 VDC W7340B1002 (Production part since 8/1/2005) - 15.0 VDC RTEM Module Voltage X13651513 - 23Vdc Table 41. DCma DCma DCma 100% 20.000 52.6 12.414 31.2 9.000 97.7...
Page 111: Space Pressure Control With Statitrac (27.5-50 Tons)
Page 112: failure and override modes of operation, page 113: electromechanical economizer functions, page 114: electromechanical economizer testing, page 115: electromechanical economizer (3 position damper), page 116: reliatel control temporary operation 3-25 tons, page 117: reliatel supply air tempering control, page 118: discharge air sensing with tci comm3/4, page 119: co sensor connections.
- Page 120 Sensor Connections (ReliaTel Units with Demand Controlled Ventilation) compromise the 100 ppm differential, the Lower Limit CO Setpoint will be pushed down in order to enforce the 100 ppm differential and to allow the Upper Limit CO Setpoint to be set as desired.
Page 121: Rtem W/ Rtrm V7.0 And Earlier
Page 122: honeywell operation.
- Page 123 Sensor Connections (ReliaTel Units with Demand Controlled Ventilation) Figure 70. Wiring Connections using CO Accessory INSET A - DUCT MOUNT INSET A - DUCT MOUNT Setpoint 0% 100% - WALL MOUNT - WALL MOUNT RT-SVD03G-EN...
Page 124: Reliatel Ventilation Override
Page 125: dehumidification with hot gas reheat (3-25 tons).
- Page 126 Dehumidification with Hot Gas Reheat (3-25 Tons) If the unit has been in cooling mode for 90 minutes, the purge sequence will switch to the dehumidification mode for three minutes. If there is still a call for cooling, the unit will once again switch back to cooling.
- Page 127 Dehumidification with Hot Gas Reheat (3-25 Tons) To measure the mA input current from the humidity sensor, disconnect sensor wire that is connected to terminal 18 of LTB. Connect amp meter in series with the wire and terminal 18 of the LTB.
Page 128: Modulating Dehumidification With Hot Gas Reheat (27.5-50 Tons)
- Page 129 Modulating Dehumidification with Hot Gas Reheat (27.5-50 Tons) Figure 72. Voyager Commercial Modulating Hot Gas Reheat Time Delayed TXV bulb 0.1” Bleed line Modulating Valves Check Valve • RTRM handles the main dehumidification logic. • RTOM contains the humidity and supply air set point. •...
- Page 130 Modulating Dehumidification with Hot Gas Reheat (27.5-50 Tons) Figure 73. Modulating Hot Gas Reheat Control Boards SETPOINT LEGEND 1.Discharge Air Heat SP - 50-150 F 2.Exhaust Fan Enable SP - 0 to 100% 3.Supply Air Reheat SP - 65-80 F 4.Dehumidifica on SP (%) - 40 to 65% RH RT-SVD03G-EN...
Page 131: Heating/Cooling Changeover
Page 132: low ambient mechanical cooling operation (3-25 ton units), page 133: reliatel condenser fan control logic, page 134: odyssey independent circuit heat pump condenser fan control, page 135: phase monitor, page 136: electromechanical time delay relay, page 137: snubber circuits, page 138: transformer troubleshooting, page 139: high pressure and low pressure lockout circuits.
- Page 140 High Pressure and Low Pressure Lockout Circuits • If Active on a Dual Circuit Unit, only Circuit 2 will de-energize during Active Cooling. Both Circuits will de-energize after the appropriate delays during Active Reheat (Circuit 1 after its minimum on timer expires). •...
Page 141: Hpc Logic
Page 142: novar controls (sequence of operation), page 143: economizer set-up.
- Page 144 ON steady and blink OFF during communications if in Scheduled ON mode. The status lights on the main ReliaTel control modules will be on steady if the boards are powered up and properly communicating on the inter-module bus.
- Page 145 Thermostat-Y1 input on the RTRM and that compressor circuit 1 is properly connected according to the Reliatel Installation guide. Verify the compressor(s) has properly connected line power and that all in-line safety limits and contactors are functioning correctly.
Page 146: Voyager Commercial 27½ To 50 Tons Cv And Vav
Page 147: rtom - reliatel options module - (standard), page 148: configuration input, page 149: supply duct static pressure control.
- Page 150 Voyager Commercial 27½ to 50 Tons CV and VAV Figure 83. Supply Duct Static Pressure Control Figure 84. RTAM Module I G V - O F F O F F V F D - O N O F F O F F O N VAV w / o I G V O N O N Static...
Page 151: Vhr Relay
Page 152: troubleshooting tips, page 153: remote setpoint inputs on rtam j7.
- Page 154 Voyager Commercial 27½ to 50 Tons CV and VAV Figure 86. RTAM module LTB-S Changeover input (VAV only) I GV - OFF OFF V FD - ON OFF OFF ON VAV w/ o I GV ON ON Static Static pressure pressure No Reset OFF OFF...
- Page 155 Voyager Commercial 27½ to 50 Tons CV and VAV Table 50. VAV Setpoints Supply Air Supply Supply Supply Air Reset RTAM Supply Air Supply Air Morning Reset Setpoint Supply Air Pressure Cooling Reset Pressure Warm-up Setpoint Zone or Heat Setpoint Setpoint Amount Deadband...
- Page 156 Voyager Commercial 27½ to 50 Tons CV and VAV Table 50. VAV Setpoints Supply Air Supply Supply Supply Air Reset RTAM Supply Air Supply Air Morning Reset Setpoint Supply Air Pressure Cooling Reset Pressure Warm-up Setpoint Zone or Heat Setpoint Setpoint Amount Deadband...
- Page 157 Voyager Commercial 27½ to 50 Tons CV and VAV Table 50. VAV Setpoints Supply Air Supply Supply Supply Air Reset RTAM Supply Air Supply Air Morning Reset Setpoint Supply Air Pressure Cooling Reset Pressure Warm-up Setpoint Zone or Heat Setpoint Setpoint Amount Deadband...
Page 158: Outdoor Air Flow Compensation For Vav Units
Page 159: operation for rtrm 8.0 and later with rtem, page 160: software change history.
- Page 161 Software Change History Feature Enhancement: -Add Voyager III control functions. -Added two flash diagnostic code and steady light. Bug fixes: -Fix service test to lock out after power reset with resistance. V4.0 1/13/04 X13650867040 -Fix outdoor fan operation on one compressor unit during Service Test with dehumidification/reset.
- Page 162 Software Change History -Odyssey Only Release. -Independent Circuit Heat Pump control for Odyssey: Includes operation as two-step mechanical heat unit with independent defrost control per circuit as well as new outdoor fan control; ODF B on with C1 and ODF A on with C2 except during Defrost. -The SOV control is changed to be ON anytime the thermostat “O”...
- Page 163 Software Change History V1.05 4/12/01 X13650878020 -Initial production release - W7399A, W7340A. V2.05 7/15/02 X13650878020 -Fixed 60 seconds communication loss. -Changed to Masked chip. V2.07 10/21/03 X13650878060 -Fixed comparative enthalpy. V2.08 8/25/04 X13650878080 -Went back to OTP chip to resolve Masked chip problems. V1.0 4/1/05 X13651082010...
Page 164: Index
- Page 165 Novar Controls 143 Protocol of Communications 48 Programmable Zone Sensor 81 ReliaTel 50 Reference Enthalpy 96 Transducer 152 Transformer 138 ReliaTel Controls 9 ReliaTel Refrigeration Module – (RTRM) 9 Variable Air Volume (VAV) 158 Return Air Humidity Sensor 10 BAYSENS021A Setpoint...
- Page 168 The manufacturer has a policy of continuous product and product data improvement and reserves the right to change design and specifications without notice. © 2010 Trane All rights reserved RT-SVD03G-EN 03 Nov 2010 Supersedes RT-SVD03F-EN (Sep 2009)
Rename the bookmark
Delete bookmark, delete from my manuals, upload manual.

IMAGES
VIDEO
COMMENTS
Evaporator Defrost Control can be initiated through two means, based on the FroStat input. FroStat Installed (default): • A FroStat input can also be used to directly request the Evaporator Defrost Control function. • When the unit is running in an effective "Cool" mode, the FroStat input will directly control the. FroStat diagnostic.
Reliatel control boards have "Trane" terminals 1-12 or so as well as "conventional" terminals R-G-Y-W etc directly on the board. Older Voyager units have Voyager or "black book" controls which require a "CTI" or Conventioal Thermostat Interface board to use a regular 24v stat. Post a pic of what you're working on, it would help greatly.
Heat pump control (Independent defrost, Dual fuel) 22 Operation with a conventional thermostat 23 ... COIL TEMP 2 COMMON/CONFIG COMMON OUTDOOR COIL TEMP 2 Signal INDEPENDENT CIRCUIT/ MOD DEHUMID CONFIG FAN PROVING Input RTRM FAN FAIL CONFIG Config - Extended Heat Config - EDC Disable 3-Step Cooling Input ... (Voyager III) Voyager III Con ...
Voyager ™ Commercial ... YC*275B, 305B, 350B, 400B, 500B ©2021 Trane RT-SVX34U-EN Introduction Read this manual thoroughly before operating or servicing this unit. Warnings, Cautions, and Notices Safety advisories appear throughout this manual as ... Failure to follow code could result in death or serious injury.
Just going over where the defrost components are on a Trane heat pump. Also how to do a simple jumper test on the defrost control board to see if its working...
Trane Voyager 12½- to 25-ton units are built to provide not only ultimate indoor ... • High temperature input open • Heat failure limit open • Outdoor air sensor failure ... • Local cool/heat setpoint failure • Minimum position Potentiometer failure • Defrost control failure • Compressor lockout • Clogged filter • Supply fan ...
To combat this problem, your heat pump has a built-in defrost cycle. The defrost control has two sensors: one inputs the outdoor temperature and one inputs the coil temperature to the defrost control. After that, a microprocessor control determines the correct defrost cycle to utilize, which then clears the frost from your coil to address the ...
Failure to follow recommendations could result in death or serious injury. WARNING Follow EHS Policies! Failure to follow instructions below could result in death or serious injury. • All Trane personnel must follow the company's Environmental, Health and Safety (EHS) policies when performing work such as hot work, electrical,
Steady Red LED - The defrost control board has detected a fault and is in lockout mode. Flashing Red LED - The sensor is not detecting proper temperature, indicating a possible faulty sensor or a wiring issue. Flashing Green LED - The system is in defrost mode, and the board is actively monitoring the process. Steady On - Power is present.
HEAT FAIL and COOL FAIL at the Same Time, RTRM-J6-7 and 8 Pulsing Voltage • Coil temperature sensor is open or shorted (heat pump only). • Unit has failed to defrost properly (see heat pump section for further details). • Outdoor air sensor is open or shorted (RTRM version 4.0 or greater).
2. Zone temperature sensor input failure on CV units. 3. Programmable ZSM communication failure. 4. Manual compressor lockout (one or both circuits) 5. Outdoor coil temp sensor failure (heat pumps only) 6. Defrost fault condition (heat pumps only) 7. Gas heat failure. 8. Discharge air temperature failure on modulating heat and modulating reheat ...
The Trane Voyager™ rooftop has by far the best efficiency in its class. All performances are Eurovent certified which provides the assurance of accurate performance and common comparison criteria. ReliaTel™ Micro Controls † The Micro provides unit control for heating, cooling and ventilating utilizing input from sensors that
No Power/Failure/ Internal Failure Steady ON: Normal - No Call for heat Slow Flash Rate Normal, call for heat (¾ second on, ¼ second off) 1 Flash : Loss of Communication 2 Flashes: System Lockout: Failed to detect or sustain a flame. (failure to ignite, no spark, low/ no gas pressure, etc.) 3 Flashes: Pressure switch problem detected.
ReliaTel Condenser Fan Control Logic 12.5 - 25 Ton For units that have two condenser fans, special control logic is designed to provide proper condenser head pressure control at different ambient conditions. With normal operation, either one or both fans will be operating depending on the outdoor temperature.
Zone temperature input failure after a successful input. Both heating and cooling setpoint inputs have failed or are not attached (such as when using a 2 - wire sensor on terminals 1 & 2). Programmable ZSM. The ZSM has failed to communicate for 15 consecutive minutes after successful communication has occurred. Heating-RTRM-J6-7.
©2023 Trane BAS-APG048B-EN Introduction Read this manual thoroughly before operating or servicing this unit. Warnings, Cautions, and Notices Safety advisories appear throughout this manual as required.
4 flashes is a hard lockout, either due to high or low pressure issues. Most likely a low pressure lockout. Can't remember off the top of my head what 5 flashes is. Sounds to me like you probably have a bad defrost board and/or coil/ambient temperature sensor issues. These sensors rarely, if ever, actually go bad.
Press up or down arrows or Set Parameter 0-23 to Display Digital Inputs. Binary # Corresponds to Digital Inputs. MSB = Term. 18. LSB = Term. 33. Digital Inputs. If Input State is not Displayed Correctly, Measure Voltage at Terminal. Reference Meter on Terminal. 20. Digital Inputs Must be 10-28VDC to be High (Logic 1)