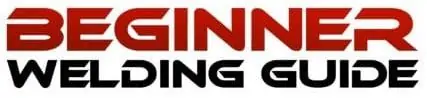

MIG Welding Wire Speed + Voltage Chart
Written By: Liam Bryant
Reviewed By: Russell Egan
As an Amazon Associate I earn from qualifying purchases.
A MIG welding wire speed chart offers insights into appropriate wire speeds for various material thicknesses and types in MIG welding. It aids in the optimal setting of your MIG welder for effective, high-quality welds.
Table of Contents
Table of Wire Speed for MIG Welding
This table is a general guide; actual settings can vary based on specific conditions, welding machine, and type of wire used.
What Impacts MIG Welding Wire Speed?
Several factors influence the speed of the MIG welding wire. Material thickness is a primary factor – the thicker the material, the higher the wire speed and amperage setting required. The type of metal (e.g., stainless steel, mild steel) and wire (e.g., solid wire, flux cored wire) also affects the wire speed. Lastly, the welding position and your own welding technique can alter optimal settings.
From my years of experience, these variables make every welding job unique. A slight change in any of them can significantly affect the quality of your weld, so always keep them in mind when adjusting your wire speed.
This is the most commonly welded metal and often used as a benchmark for setting the wire speed in MIG welding. Mild steel has a relatively lower melting point than other metals, which usually requires a moderate wire speed.
Stainless Steel
Stainless steel has a higher melting point than mild steel. Consequently, it generally requires a lower wire speed to maintain a steady, controlled weld pool and prevent burn-through.
Aluminum conducts heat very effectively and has a lower melting point, leading to its base metal heating up quickly during welding. This requires a higher wire speed to compensate for the quick heating and melting, often making aluminum more challenging to weld than steel.

How to Set the Wire Speed for MIG Welding?
Setting the wire speed for MIG welding involves understanding the correlation between wire speed, voltage, and amperage. A higher wire speed requires a higher voltage to maintain a stable arc.
Consult your MIG welder’s chart for a rough guide on wire feed speed and voltage settings according to material thickness. From there, it’s fine-tuning based on your specific scenario and welder’s feel. A too slow wire speed might result in a weak weld, while a too fast speed may cause the wire to burn back towards the contact tip.
Wire Speeds for Common Welding Scenarios
- Welding Thin Material: You’ll need lower wire speeds when welding thin materials like sheet metal . It prevents the risk of burn-through.
- Welding Thick Material: A higher wire speed is required to achieve good penetration for welding thicker materials.
- Vertical Welding: A slower wire speed helps prevent the weld pool from sagging when welding vertically.
In my own experience, welding stainless steel requires a particularly fine balance. It’s less forgiving than mild steel and needs careful wire speed adjustment to get just the right penetration without burning through.
How to Control the Wire Speed on a MIG Welding Machine
Most MIG welders come with a wire feed speed dial. This knob or button allows you to increase or decrease the speed at which the wire is fed into the weld joint .
If you’re new to welding, start with your machine’s suggested settings and make incremental adjustments. Be sure to practice on some scrap metal first. Over time, you’ll understand how adjustments affect your weld quality.

Tips for Selecting the Correct MIG Welding Wire Speed
- Use a Welding Calculator: A welding calculator is a valuable tool for beginners. It calculates appropriate settings based on the type of metal, thickness, and wire type.
- Practice on Scrap Material: Before starting your project, practice on a scrap piece of the same material. This way, you can fine-tune your settings without affecting your project.
- Listen to Your Weld: A good weld sounds like sizzling bacon. If it pops and spatters, your wire speed might be too high.
Some welding machines give you a wire speed in terms of 1,2,3 out of 10. This will relate to a specific inches per minute speed. It is good to understand what your particular welding machine uses so when you move from machine t machine you can adjust more asily.
As an experienced welder, I’ve learned that there’s a certain art to selecting the correct wire speed. It takes practice, patience, and willingness to make and learn from mistakes.
Understanding your MIG welding wire speed chart and how to manipulate the wire speed according to your welding scenario is key to achieving high-quality welds. Whether you’re a novice or a seasoned welder, the chart, combined with your experience and judgment, is an indispensable tool.
Remember, practice makes perfect, and every piece of metal has a story to tell.
MIG welder settings explained – Amperage & Wire Speed
There might be affiliate links in this post. Buying through them can earn us a small commission at no cost to you. This covers our wages and keeps our resources free to use.
MIG welding process is one of the most straightforward processes to master, but beginners often have issues getting the settings right. You can purchase the most expensive MIG welding machine on the market, but the results may still vary.
To help you dial in your machine, we will thoroughly explain each set’s representation. Keep in mind that there are some universal rules, but most differ from a device.
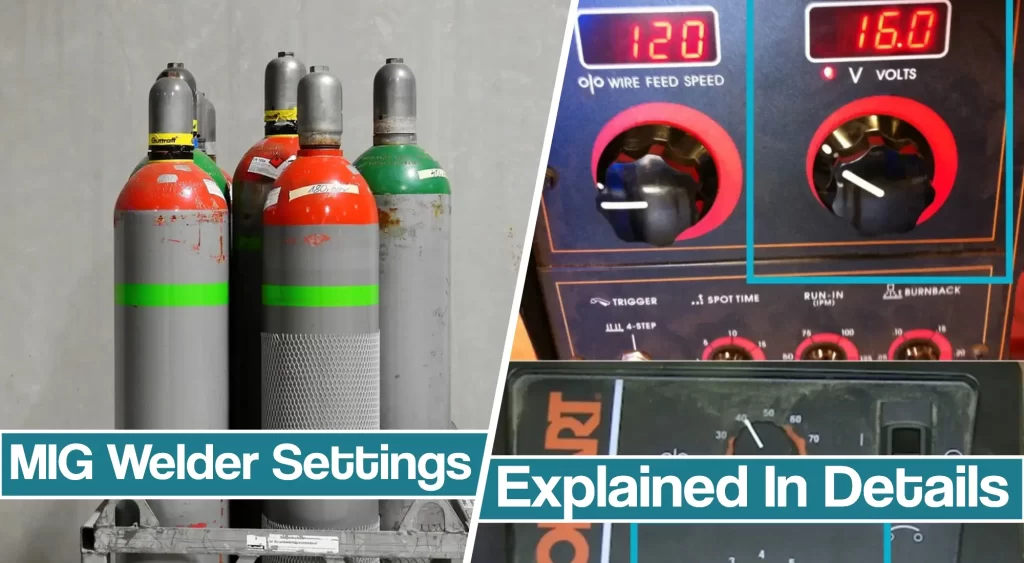
However, by understanding the basics we explained in the article, you will be able to diagnose the issue.
First Things First – Material Choice and Thickness
Before you start banging your head with MIG welder settings, you should first ask yourself – What and how thick material will you be welding?
Each material type has its unique mechanical properties.
For example, different metal alloys have different melting temperatures, tensile strength, and hold that heat differently. Therefore, there are no universal settings applicable to all material types.
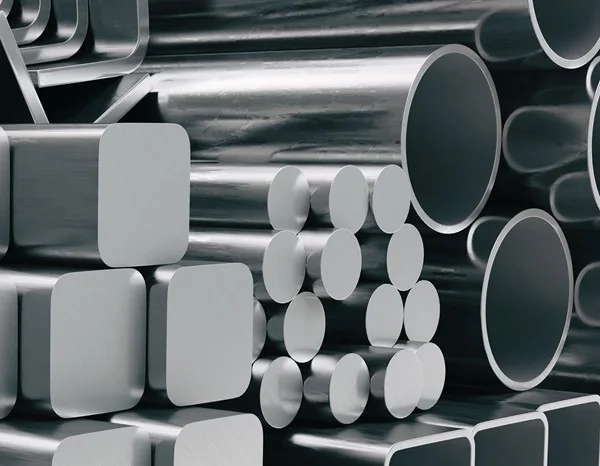
Mild steel is the most common metal, and as a hobbyist, it is most likely you will deal with it. The 0.25% carbon content is lower than medium and high carbon steels, which makes it a highly machinable metal.
On the other hand, seasoned welders might occasionally weld aluminum or work with stainless steel. Aluminum has many positive characteristics like being non-corrosive, lightweight, and is visually appealing. Unfortunately, all the positive sides of aluminum are what make it difficult for fabrication.
So before you start welding, you should consider the material you will be welding and its thickness.
How Does Material Thickness Affect MIG Welder Settings(Metal Inert Gas Welding)?
The thickness of the material might be one of the crucial things you should consider when setting up your machine.
When welding Stick or TIG, you can use nearly similar settings with different thicknesses, but with MIG, it gets tricky.
The general rule, also known as the thumb rule, states you should use 1 amp for .001 inch of material thickness . So, for example, if you are welding 1/8″ mild steel (0.125 inches thick), you should provide 125 amps.
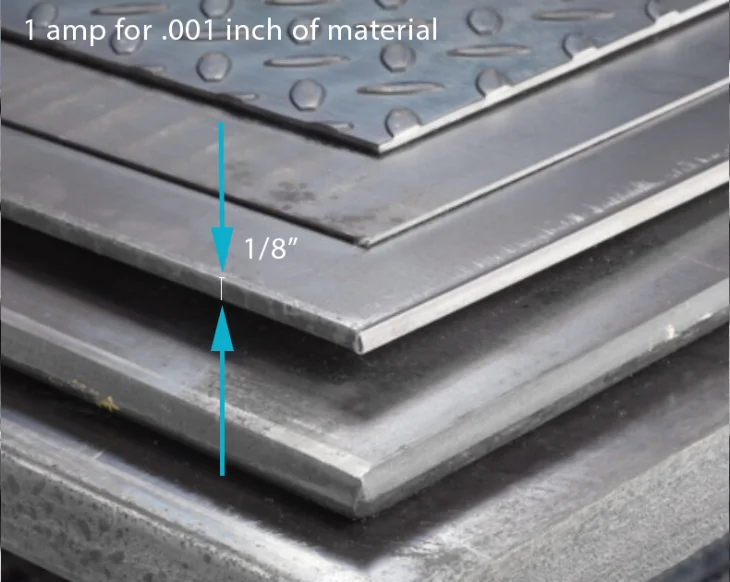
However, this rule applies to mild steel, while you will have to provide about 10-15% less current for stainless steel or 25% more current for aluminum.
In addition, there are a couple of flaws when it comes to thicker metals. So, when dealing with 1/2″ thick metals, you should provide 500 amps while following the rule. However, some manufacturers claim you can use their machines rated at 200-250 amps to do it, while the recommendation says otherwise.
Therefore, you should use the rule as a guideline for optimal performance and follow the manufacturer’s recommendations.
Shielding Gas and MIG Welding Wire
Shielding gas plays a crucial role in protecting your weld bead from defects. So before you start your welding, you will have to choose a mixture of inert gases according to a type of metal and adjust the flow according to welding conditions.
In MIG welding, you will be mostly using Argon, Helium, CO2, or a touch of Oxygen. In addition, the wire types (filler material) should suit the base metal, and here are some recommendations.
- If you are welding mild steel (carbon steel), the best choices are C25 gas type (75% Argon and 25% Carbon Dioxide) and ER70s electrode.
- As for stainless steel, C2 gas (98% Argon and 2% Carbon Dioxide) and ER308L wire type are your choices.
- Aluminum is tricky, as you will have to provide ER4043 wire with 100% Argon gas.
A high percentage of Argon or Helium added to a mix creates a hotter arc in the weld area. Besides choosing the proper type of wire, you should use an adequate filler thickness. Select one for your most commonly used thicknesses since you don’t want to change the wire.
- 30-130 amps: .023 inch
- 40-145 amps: .030 inch
- 50-180 amps: .035 inch
- 75-250 amps: .045 inch
Weld Preparation
Welding preparation is no mystery as the clean welding surfaces will produce clean welds. Welder settings may differ if you work with oily, rusty, or dirty steel, so you want to ensure a clean weld.
In addition, dirty joints spatter a lot! So if you fail to clean a joint, excessive spatter may burn you or cause a fire. Settings don’t create good welds; they make good welds possible. But only if you do the rest.
That’s why you should always clean, de-scale, grind and degrease the work material before you start welding.
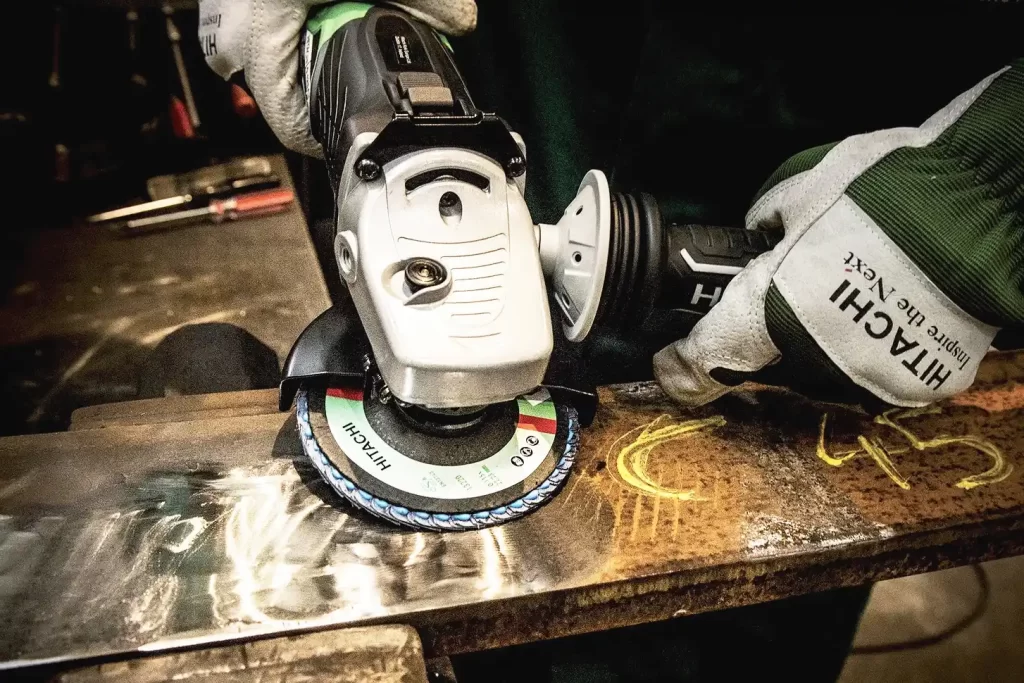
MIG Welding Settings: What Do They Mean?
After you have determined the thickness and type of material, selected a proper shielding gas and electrode, and cleaned the surface, it is time to set up your machine. This section will examine the voltage and wire speed and shielding gas flow.
MIG Welding Voltage Setting
MIG welding almost always uses a DC+ polarity type. The most straightforward explanation states that the voltage determines the height and width of the bead. In addition, there is a relationship between arc voltage and arc length.
A short arc (low voltage settings) yields a narrow, ropey bead with a possibility of poor arc starts. A longer arc (more voltage) produces a flatter, wider bead.
Too much arc length makes a very flat bead and the undercut possibility.
To get the voltage straight, you should follow the manufacturer’s recommendations. For example, instruction manual or side door charts usually feature only guidelines.
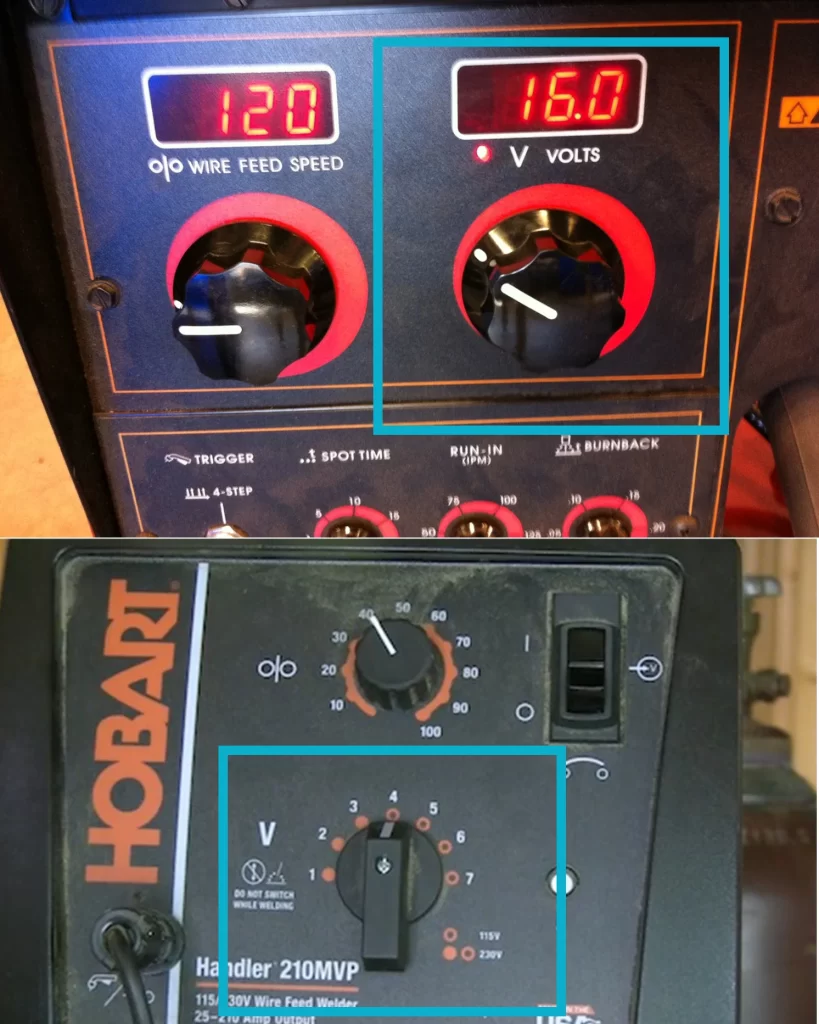
However, if there are no recommendations whatsoever (which is rare today), you should practice independently. Use a piece of scrap metal that is thick as the part you will weld, and start experimenting. Slowly turn the values up or down, until you get decent results.
You can use a sound to determine the proper voltage. Adjust the voltage until you get a nice bacon frying sound. Too little voltage and it will snub and sound like a drive-by. Too much voltage and the wire will try to burn back, or you’ll get the sound of a rattle or hiss.
Wire Feed Speed
Wire-speed controls amperage, as well as the amount of weld penetration. If you turn the wire speed up, you might have to deal with a burn-through. On the contrary, a narrow, often convex bead with poor tie-in at the toes will occur if the feed is too slow due to insufficient penetration.
Some experienced welders like to adjust wire feed speed to their preferences for different transfer type (e.g., short circuit transfer).
The instruction manual and side door chat should give you recommendations for each material thickness. If there are no guidelines, you can use our chart to serve as a starting point. For example, for .030-inch wire, multiply by 2 inches per amp, while for .023, multiply it 3.5 times.
For wire size multiply by Ex. using 1/8 inch (125 amps)
Gas Flow Settings
Once you set up your machine to produce fine weld quality, you should set the shielding gas flow to protect it from defects. The primary purpose of the gases and mixtures we described above is to prevent contamination of your weld. Gas flow is measured in cubic feet per minute CFM.
As for the other settings, you should experiment since the amount of flow depends on current welding conditions. For example, if you are welding in the shop or other indoor conditions, 15-20 CFM will do just fine.
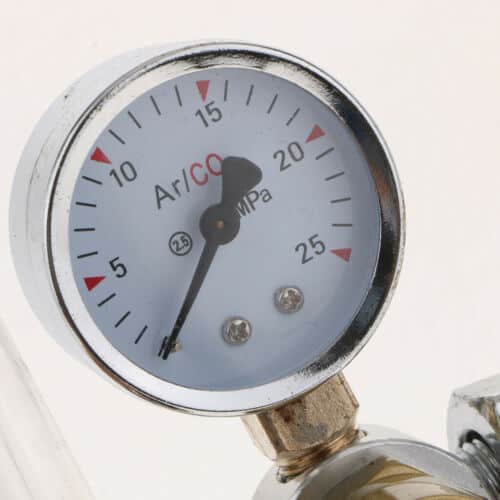
However, if you open the door or a draft present, you should turn it up to 35-40 CFM. But, keep in mind that too much gas pressure can cause turbulence and suck in air to contaminate the weld.
MIG Welding Charts
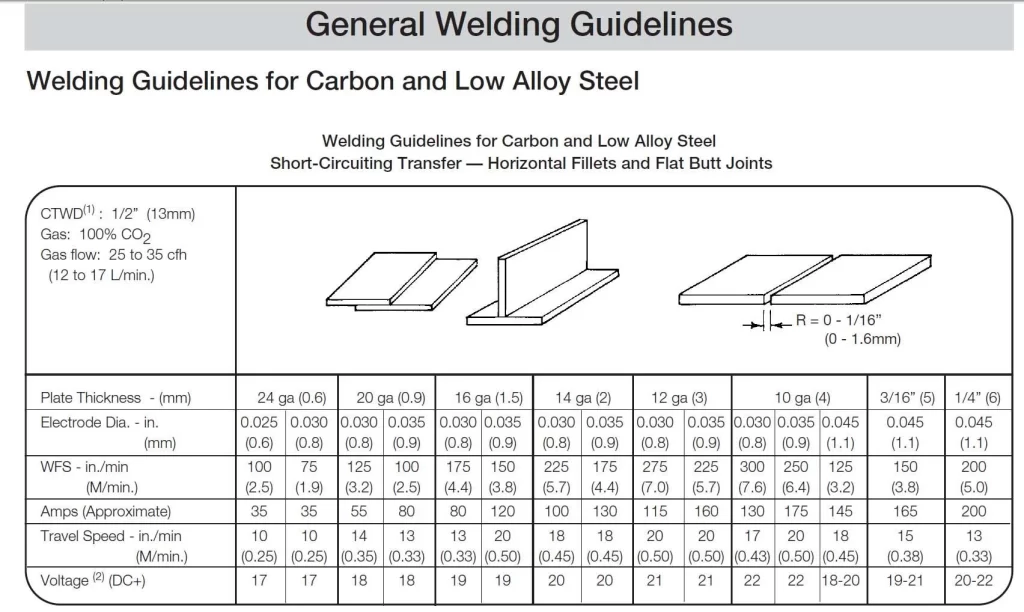
The welding chart that comes with your machine undoubtedly provides the best guidelines for the welding start. However, state-of-the-art hobbyist MIG welders such as Miller Millermatic or YesWelder MIG 205 DS feature intelligent settings.
With synergic or auto-set settings, you have to input the material thickness and MIG wire diameter, and the machine will do the rest. Auto-set is an excellent feature for beginners, so if you are tired of trying to figure out the machine settings, you should look for a MIG welder that provides it.
However, nothing beats the manual settings, as recommendations might be too hot or cold. That’s why you should always use charts and synergic settings as a guideline.
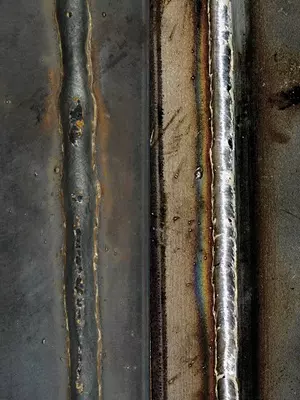
Wrapping Things Up:
First, you should consider the material type and thickness and adjust the accessories and equipment. Then you will have to clean your weld. Finally, voltage, wire speed, and gas flow settings come at last, where you combine everything you learned in this article.
To keep it as simple as possible, we pointed up many times that there are no universal settings that you can use on welding machines. So even though it might sound disappointing, understanding the controls is crucial.
Remember that setting the machine is a trial and error process. You will burn through the metal with too much heat, burn your MIG gun nozzle, or achieve poor penetration until you get it right.
If your hobby is turning into a passion, you can always consider one of the welding technician programs.
- MIG welder settings by Miller Electric https://www.millerwelds.com/resources/article-library/miggmaw-101-setting-the-correct-parameters
- Adjusting power settings by MIG welding UK https://www.mig-welding.co.uk/power-settings.htm
- MIG welder considiration by Tulsa Welding School https://www.tws.edu/blog/welding/mig-welder-setup-considerations/
- Tips for settings MIG parameters by Hobart Brothers https://www.hobartbrothers.com/2021/09/tips-for-setting-mig-welding-parameters-for-thin-materials/
- Welding parameters by ESAB https://www.esabna.com/euweb/mig_handbook/592mig7_1.htm
Leave a Comment Cancel reply
WeLDingpros.net
Mentioned On:

Welding Machines
TIG Welders
MIG Welders
SMAW Welders
Plasma Cutters
Flux Core Welders
Multi Process Welders
Welding Guides
Welding Symbols PDF
How to MIG Weld
TIG Welding (GTAW)
Welding Joints
Best Welding Schools
Welding Stainless
Welding Helmets
1/1/1/1 VS 1/1/1/2
Change The Battery
Underwater Welding Helmet
Welding Gloves
Lens Shade Guide
Disclaimer Weldingpros.net is a participant in the Amazon Services LLC Associates Program, an affiliate advertising program designed to provide a means for sites to earn advertising fees by advertising and linking to amazon.com.
Amazon, the Amazon logo, AmazonSupply, and the AmazonSupply logo are trademarks of Amazon.com, Inc. or its affiliates.
As a YesWelder affiliate, I earn commissions for qualifying purchases.
Copyright © 2021 Weldingpros.net

How to Calculate Travel Speed in Mig Welding: A Comprehensive Guide
How to calculate travel speed in mig welding.
To calculate travel speed in MIG welding, you need to use the Travel Speed calculator.
This calculator uses the time taken to complete the weld, the weld length, welding amps, and volts to determine the travel speed.
It utilizes two formulas to calculate the heat input.
It is important to calculate the travel speed accurately to ensure proper feed speed in MIG welding.
Improper feed speed can result in weak weld joints or burn holes in the metal.
MIG welding machines automatically feed wire through the torch head to the weld site, and the wire acts as the electrode to create the weld bead and filler material.
The MIG wire must be fed at the appropriate speed to ensure a proper joint is created.
Did You Know?
1. The speed of travel in MIG welding is typically measured in inches per minute (IPM) or centimeters per minute (CPM). However, did you know that the optimal travel speed can vary depending on the material being welded? For example, when welding aluminum, the travel speed should be slower compared to welding steel or stainless steel.
2. One factor that can affect travel speed in MIG welding is the welding position. It is generally easier and faster to weld in the flat or horizontal positions compared to vertical or overhead positions. So, if you’re looking to increase your travel speed, try to weld in a favorable position whenever possible.
3. Travel speed can have a significant impact on the quality of the weld. Welding too slowly can result in excessive heat input, leading to distortion, burn-through, or lack of fusion. Conversely, welding too fast can result in insufficient heat input, causing poor penetration and weak welds. Therefore, finding the right balance and maintaining a consistent travel speed is crucial for achieving high-quality welds.
4. The type and size of the welding wire you use can also influence the travel speed in MIG welding. Thicker wires typically require higher travel speeds, while thinner wires require slower travel speeds. Additionally, selecting the proper wire feed speed and voltage settings for your specific wire diameter can help optimize travel speed and overall welding performance.
5. It’s important to note that travel speed is not the sole determinant of productivity in MIG welding. Other factors, such as proper joint preparation, suitable shielding gas, and appropriate welding techniques, also play a significant role. Keeping these aspects in mind and adjusting the travel speed accordingly can help you achieve efficient and high-quality MIG welds.
Introduction To Travel Speed Calculator In Mig Welding
MIG welding , also known as Gas Metal Arc Welding (GMAW) , is a versatile welding process widely used in various industries. The travel speed calculator is an essential tool that aids in determining the optimal travel speed for MIG welding.
By finding the right travel speed , welders can ensure the creation of strong and durable weld joints. The calculator requires specific inputs, including:
- The time taken to complete the weld
- The length of the weld
- Welding amps
With this information, the calculator employs two formulas to calculate the heat input , which is a crucial factor in determining the travel speed.
Required Inputs For Travel Speed Calculation
To effectively utilize the travel speed calculator, the following key inputs must be provided:
- Time taken to complete the weld : This refers to the duration it takes to finish the welding process.
- Length of the weld : It is the distance that needs to be covered during welding.
- Welding amps and volts : These represent the electrical parameters set on the welding machine. These values directly impact the heat input and consequently determine the travel speed.
Accurate measurements and data are crucial for the calculator to provide reliable results.
The Importance Of Heat Input Calculation In Mig Welding
The heat input calculation in MIG welding is crucial for ensuring the quality and integrity of the weld joint. It refers to the total amount of heat energy transferred to the weld, and is a critical parameter in determining the proper travel speed needed to achieve a sound weld .
Accurate heat input calculation is vital to ensure that the weld metal is adequately melted and fused together. Incorrect calculations can result in incomplete fusion or overheating , leading to weak weld joints and potential failure under stress.
The travel speed calculator utilizes the heat input calculation to determine the optimal travel speed , which greatly contributes to the overall success and durability of the welded joint.
– Importance of heat input in MIG welding:
- Determines quality and integrity of weld joint
- Critical for achieving a sound weld
- Ensures adequate melt and fusion of weld metal
– Consequences of incorrect heat input calculation:
- Incomplete fusion or overheating
- Weak weld joints
- Potential failure under stress
– Utilization of travel speed calculator:
- Determines optimal travel speed
- Enhances overall success and durability of weld joint
“The heat input calculation in MIG welding is of utmost importance as it directly affects the quality and integrity of the weld joint.”
Effects Of Improper Feed Speed In Mig Welding
Proper feed speed is crucial in MIG welding as improper feeding can have detrimental effects on the resulting weld joint. Inadequate wire feed speed , either too slow or too fast , can lead to various issues such as weak weld joints or burn holes in the metal.
Insufficient wire feed speed can result in a lack of proper fusion between the weld metal and the base metal. This can lead to weak weld joints that are prone to failure under stress . On the other hand, excessive wire feed speed can create excessive heat , causing burn holes in the metal.
It is essential to ensure that the wire feed speed is at an appropriate level to guarantee the creation of a sound and durable weld joint . The travel speed calculator aids in determining the suitable wire feed speed by considering the specific parameters and requirements of the welding process.
Understanding The Role Of Mig Wire In Creating Weld Joints
In MIG welding , the wire acts as the electrode , creating the weld bead and serving as the filler material to join metal pieces. The MIG wire plays a critical role in the welding process, as it determines the composition and strength of the weld joint.
The MIG wire must be carefully selected based on the materials being welded and the desired mechanical properties. Different types of MIG wires, such as solid wires and flux-cored wires , have various applications and advantages. Solid wires are commonly used for welding mild steel , while flux-cored wires are suitable for welding in outdoor or windy conditions .
Understanding the role of the MIG wire allows welders to select the appropriate wire for the job at hand, ensuring optimal performance and strong weld joints .
- MIG welding uses the wire as the electrode, weld bead, and filler material.
- The composition and strength of the weld joint depend on the MIG wire selected.
- Different types of MIG wires, such as solid and flux-cored wires, have specific applications.
- Solid wires are suitable for welding mild steel, while flux-cored wires are ideal for outdoor or windy conditions.
“The MIG wire determines the composition and strength of the weld joint.”
Significance Of Proper Wire Feed Speed In Mig Welding
Proper wire feed speed is crucial in MIG welding as it directly impacts the quality and strength of the weld joint. The wire must be fed at the correct speed to ensure the creation of a proper joint.
If the wire feed speed is too slow , there may be insufficient filler material to adequately fill the weld joint, resulting in weak or incomplete fusion . Conversely, if the wire feed speed is too fast , excessive heat may be produced, potentially leading to burn-through or distortion .
By utilizing the travel speed calculator , welders can determine the appropriate wire feed speed needed for a particular welding project. This ensures the creation of strong, durable, and high-quality weld joints that meet industry standards and requirements .
In conclusion , the travel speed calculator plays a vital role in MIG welding by helping calculate the optimal travel speed . Accurate inputs and calculations aid in determining the appropriate heat input , which directly influences the quality and strength of the weld joint. By understanding the significance of proper wire feed speed and selecting the appropriate MIG wire , welders can ensure the creation of sound and durable weld joints .
Frequently Asked Questions
How do you calculate mig welding speed.
To calculate MIG welding speed, you need to multiply the required amperage of the weld by the burn rate associated with the wire’s diameter. For instance, if the required amperage is 125 amps and the wire’s burn rate is 2 inches, the feed speed can be calculated as 250 inches per minute. This formula helps determine the appropriate feed speed for achieving the desired welding result.
What is the formula for travel speed in welding?
The formula for travel speed in welding can be determined by dividing the length traveled (l) by the time taken (t) to travel that length. In this case, with a length (l) of 150 mm and a time (t) of 68 s, the travel speed can be calculated as 150 mm / 68 s = ~2.2 mm/s or 132 mm/min. Therefore, the formula for travel speed in welding is l / t.
What is the formula for travel speed?
The formula for calculating travel speed is derived from the relationship between distance travelled and the time taken. By dividing the distance by the time, we can determine the average speed at which an object has traveled. This relationship is represented in the formula: speed = distance ÷ time. By applying this formula, we can quantify and understand the speed at which objects move in relation to the distance covered and the time it took.
How do you calculate MIG welding parameters?
To calculate MIG welding parameters, it is crucial to understand the relation between material thickness and required output amperage. As a rule of thumb, for every .001 inch of material thickness, 1 amp of output is needed. For instance, a .125 inch thickness warrants 125 amps for optimum welding performance. Thus, determining the appropriate wire size becomes pivotal and should be chosen accordingly to match the designated amperage for a successful MIG welding operation.
Related Articles
How to explain gas welding: an easy, stepbystep guide, how to flatten a welding table: essential steps, how to close down welding equipment safely and efficiently, what welding techniques for sheet metal fabrication exist, adblock detected.

Gas Metal Arc Welding Basics, Part 2: CTWD and Travel Speed Variables
Part 1 in our GMAW series, Gas Metal Arc Welding Basics, Part 1: Welding Current and Voltage , discussed how variations in both welding current and welding voltage affect the penetration profile and bead profile of a weld. In this installment, the variables of travel speed and contact tip to work distance (CTWD) will be discussed in the same fashion.
These topics cover the four main variables of the gas metal arc welding (GMAW) process that affect both the penetration profile into the base material and weld bead profile that lies above the base material for a given weld:
- Welding Current
- Welding Voltage
- Contact Tip to Work Distance
- Travel Speed
Also known as metal inert gas (MIG) welding, basic GMAW processes allow for wide-ranging adaptability to ensure desired outcomes. Let’s see how these final two variables impact results .
The Effect of Travel Speed in Welding
In most cases, weld penetration into a base material is increased when the travel speed of a weld is increased, and vice versa. At slower travel speeds, the arc is directly above the center of the molten weld pool. Consequently, the metal that is transferred from the melting filler metal to the weld pool is deposited into the center of the weld pool. When the metal transfer happens in this centered fashion, the weld pool acts as a large cushion to the incoming metal droplets and reduces the degree to which the droplets penetrate into the base material.
Conversely, at faster travel speeds, the arc is typically at the leading edge of the weld pool resulting in the metal transfer droplets directly impacting some of the base material instead of just the weld pool. This more direct impacting into the base material results in deeper weld penetration as it limits the cushioning effects of the weld pool.
The welds show in Figure 1 & 2 show the relationship between travel speed and weld penetration into the base material. The welds were made at incrementally increased travel speeds yet at the relative same heat input. This was done in attempt to keep the weld deposit size of each weld bead relatively the same. Weld 30 through Weld 34 had increased travel speeds and consequently increased penetration into the base metal. The weld data for these welds is shown in Table 1.
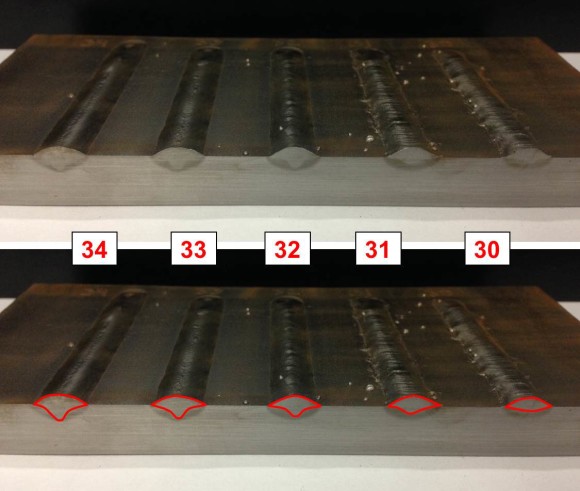
Slower travel speeds result in a solidification pattern that is circular or oval. Faster travel speeds result in a solidification patter that is circular on the leading edge but V-shaped on the trailing edge of the weld pool. Note the variation in solidification pattern of each bead outlined in red on Figure 2.
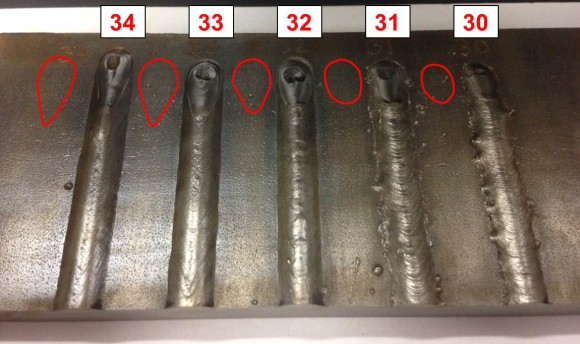
GMAW Contact Tip to Work Distance
As discussed in Part 1 of this series , GMAW process commonly uses a constant voltage power source (GMAW-CV) that allows for a relatively constant welding voltage output over a range of welding currents. For GMAW-CV, the welder selects the wire feed speed (WFS) on the wire feeder unit and an appropriate voltage on the welding power supply. The internal circuitry of the power supply then supplies an appropriate amount of welding current necessary to maintain a stable arc. The GMAW process variables of current and wire feed speeds are interrelated so one cannot be independently adjusted without affecting the other by just altering the WFS selector setting on the power supply itself.
One common way to independently manipulate the welding current from the WFS is by adjusting the contact tip to work distance (CTWD). This phenomenon understood by applying Ohm’s law, V=IR (V=voltage, I=current, and R=resistance), to the electric extension segment of the welding wire, Figure 3.
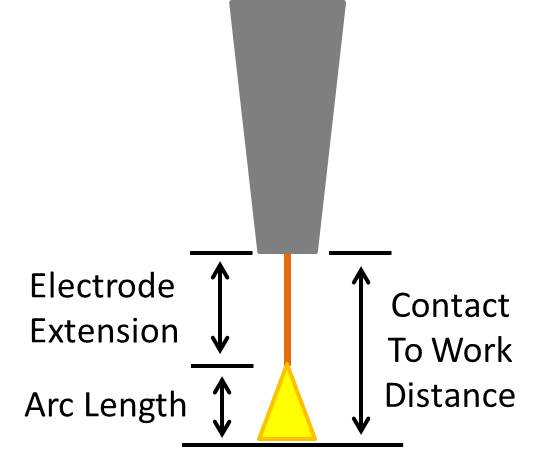
Since we want to see the effect of CTWD variations on welding current, let’s rearrange the equation to I=V/R. Assuming the use of a constant voltage power supply the V (volts) will remain a constant in this equation. The diagram on the left of Figure 4 suggests a baseline CTWD. If then, the CTWD is increased the electrode extension will also increase since the constant voltage power supply will maintain a consistent arc length despite the change in the CTWD. The increase in electrode extension length has an associated increase in resistance as the effective ‘conductor’ length has increased. According to Ohm’s law, assuming a constant voltage, current and resistance are inversely proportional to each other so the increase in resistance will result in a decrease in current.
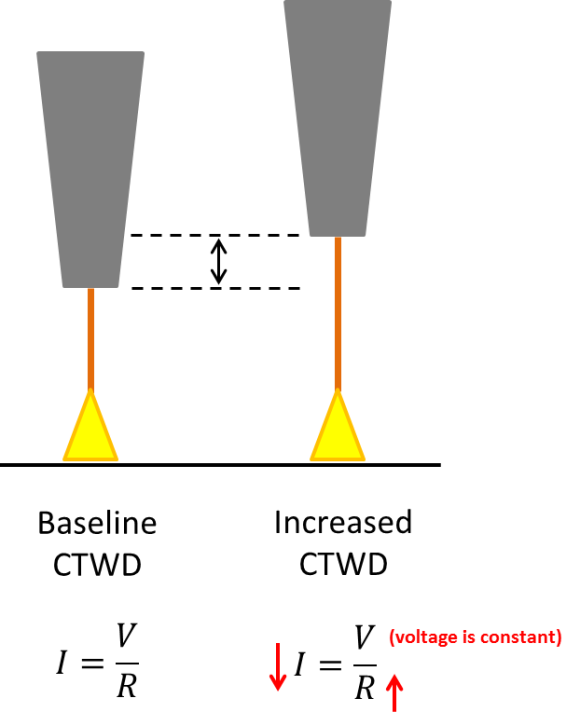
CTWD should follow Ohm’s Law, and this is exactly what was seen in Welds 13 – 18. As the CTWD was incrementally increased for each weld, the welding current decreased, all the while maintaining the same WFS. The weld data from these trials is shown in Table 2.
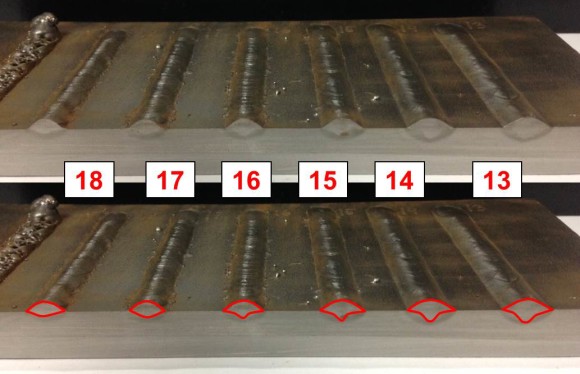
Take a Closer Look with EWI
From GMAW basics to pioneering joining solutions, EWI customers and members get the support and insight they need to improve manufacturing results. Ready to learn more about GMAW at EWI?
MORE ARC WELDING INFORMATION
Questions? Contact Michael Carney, EWI Senior Engineer, at [email protected] .
Privacy Overview

GMAW Travel Speed & Deposition Rate Calculator
How to use this calculator.
The below GMAW / MIG welding calculator is designed to help welding professionals quickly and accurately estimate weld travel speeds and deposition rates. Simply select the desired fillet weld size, material type, welding wire diameter, transfer method, and wire feed speed being used. Once you click the calculate button, the required travel speed will be displayed in inches per minute. The deposition rate will also be displayed below the travel speed in lbs. per hour. The tool can be used to quickly setup automated or semi-automated GMAW / MIG welding equipment.
WeldGallery.Com
Offering comprehensive solutions
MIG Welding Wire Speed And Voltage Chart: Optimize Your Welds
A MIG welding wire speed and voltage chart provide essential settings based on material thickness and wire diameter. Adjusting them optimizes welding performance and quality.
Navigating the complexities of MIG welding requires a deep understanding of its two pivotal parameters: wire speed and voltage. These settings can significantly impact your welds’ penetration, bead shape, and overall quality. Novice and seasoned welders rely on a MIG welding wire speed and voltage chart as a vital reference to ensure that their setup matches the job’s demands.
Factors such as the type of metal being welded, its thickness, and the welding position come into play when consulting the chart. Knowing the correct values to set on your MIG welder can be the difference between a mediocre joint and a superior weld, guaranteeing strength and durability in your metalwork projects. Let’s delve into how you can optimize your MIG welding process by accurately interpreting a comprehensive wire speed and voltage chart.
Table of Contents
Importance Of Wire Speed And Voltage
Mastering MIG welding involves understanding the precise balance between wire speed and voltage. These settings are pivotal in defining the welded joint’s quality, efficiency, and strength. The wire speed sets the pace of the electrode, which provides the filler metal needed for the weld. Voltage, on the other hand, controls the arc’s heat and overall width. Perfect harmony between these factors is crucial for achieving optimal weld consistency and penetration.
Significance Of Correct Wire Speed And Voltage
Finding the correct settings on a MIG welding wire speed and voltage chart is not just about following instructions but understanding their significance in welding. Achieving the right balance:
- Enhances Arc Stability: Steady wire feed and appropriate voltage ensure a stable arc, which is crucial for a clean weld pool.
- Reduces Spatter: Incorrect settings can lead to excessive spatter, implying additional cleanup and wasted material.
- Improves Penetration and Fusion: Optimized settings enable the weld to penetrate the base material correctly, creating a solid bond.
The welder must adjust these settings based on the material thickness, joint configuration, and the desired weld bead profile . Generally, a higher wire speed requires increased voltage to maintain the arc, but balances must be tweaked for precision.
Impact On Weld Quality And Appearance
The collaboration between wire speed and voltage goes beyond technical settings, significantly affecting the final appearance and integrity of the weld:
- Cold Welding: Low voltage or slow wire speed can result in a weak, cold weld with poor adhesion.
- Burn Through: Conversely, too high a voltage or fast wire speed might cause excessive penetration and burn through, especially on thinner materials.
- Aesthetic Finish: Aesthetics may be crucial in visible welds, with balanced settings producing a smooth, even bead.
Factors such as material type, gas mix, and even welding positions influence the ideal wire speed and voltage. Adhering to a MIG welding wire speed and voltage chart is often the starting point for these adjustments. Nonetheless, skill and experience play a significant role in fine-tuning these settings to the specific task.
Here is an example of what a basic MIG Welding Wire Speed and Voltage Chart might look like for a beginner to reference:
This chart serves as a guideline, but the welder must still make incremental adjustments to account for the specific conditions of each welding situation.
In summary, correctly managing wire speed and voltage is essential for achieving superior weld quality and appearance . It is a blend of science and skill that highlights the significance of precision in welding practices.
Variables Affecting Wire Speed And Voltage
The quest for the perfect MIG weld involves a delicate balance of wire speed and voltage, with various factors playing pivotal roles in achieving this equilibrium. Understanding these variables can vastly improve welding performance and results. Let’s explore the key elements every welder must consider when setting up their MIG welding machine.
Material Thickness
The thickness of the welded material is a primary determinant of the appropriate wire speed and voltage settings. Thicker materials require a higher voltage to ensure proper penetration and a more incredible wire speed to fill the joint adequately. Here’s a simplified guideline:
- Thin materials (<1/8 inch): Lower wire speed and voltage to prevent burn-through.
- Medium thickness (1/8 inch to 1/2 inch): Moderate settings to balance penetration with filler deposition.
- Thick materials (>1/2 inch): Increased settings to achieve deep penetration and adequate filler material.
Welding Position
The gravitational pull on the molten weld pool significantly affects which settings to use. Different welding positions require wire speed and voltage adjustments to counteract gravity’s influence. Consider the following:
- Flat and Horizontal: Standard settings based on material thickness.
- Vertical: Lower wire speed and voltage to avoid sagging or dripping.
- Overhead: Further reduced settings to control the weld pool and minimize spatter.
Joint configuration dictates the amount of filler material needed and the ease of access to the joint. Common joint types such as butt, fillet, and lap joints alter the appropriate settings due to differences in joint geometry:
Each joint type may necessitate fine-tuning the wire speed and voltage beyond the initial suggested settings to achieve optimal weld quality.
By considering these factors, welders can dial in their MIG welding settings to achieve more robust, more consistent welds. However, experience and testing are invaluable for refining these parameters for your specific welding situation.
Determining The Right Wire Speed And Voltage
Determining the Right Wire Speed and Voltage in MIG welding is crucial for achieving the best weld quality and efficiency. This balance impacts penetration, bead shape, and overall weld strength. While MIG welding wire speed and voltage charts are helpful starting points, several factors may necessitate adjustments to these settings. Optimizing wire speed and voltage contributes to a smoother welding experience and reduces the likelihood of common welding issues, such as spatter or poor penetration. Let’s delve into how to establish these essential parameters.
Manufacturer’s Recommendations
Finding an appropriate starting point for your MIG welding settings begins with the manufacturer’s recommendations . These guidelines provide a solid foundation for initial wire speed and voltage settings. Usually found in the welder manual or delivered on a chart attached to the welding machine, these recommendations are based on the machine’s capabilities and tested combinations of wire diameters, materials, and gas types. Remember that while helpful, these suggestions should be tailored to your specific welding conditions.
Welding Process
Different welding processes come with their unique demands. For instance, a short circuit transfer method will use different settings than a globular or spray transfer. The material’s thickness and the weld’s position (overhead, horizontal, or vertical) also play pivotal roles. Heavier fabrics and different welding positions require wire speed and voltage adjustments to ensure proper penetration and weld bead quality. Examining these aspects to determine the precise requirements for your welding process is essential.
Adjusting For Specific Conditions
Even with the best starting points, real-world conditions often demand fine-tuning of the wire speed and voltage . Factors such as variations in material thickness, joint design, or even the ambient temperature can influence the optimal settings. When you encounter these variables, a systematic approach works best:
- Begin with small increments : Adjust either wire speed or voltage in slight modifications to avoid drastic changes in weld quality.
- Observe weld behavior : Pay attention to the arc stability and bead appearance with each adjustment. Look for consistency and smoothness.
- Test welds : Before beginning the project, perform test welds on scrap materials similar to your workpiece to verify the settings.
Consistent practice and attention to changes in your welding environment will enhance your ability to quickly identify and implement the optimal wire speed and voltage settings.
Expected Wire Speed And Voltage Settings
Mastering your MIG welding wire speed and voltage settings is essential for achieving solid, high-quality welds. As you become more involved in welding, these settings become second nature. Understanding and applying the correct combinations can mean distinguishing between a good and an excellent weld. Below, we delve into the expected wire speed and voltage settings that are vital for a wide range of projects.
Chart Explanation
A MIG welding wire speed and voltage chart provide a starting point for setting up your welding machine. It is crucial because it helps to apply the right amount of heat and filler material for different welding jobs. Let’s take a closer look at the elements you’ll find in most charts:
- Wire Speed: Measured in inches per minute (IPM), this determines how fast the wire is fed from the machine into the weld joint.
- Voltage: This controls the arc’s length and heat, contributing to the penetration and bead profile.
- Material Thickness: Listed in gauge or inches, suggesting suitable settings for varying metal thickness.
Interpretation For Different Materials And Thicknesses
Interpreting the chart for different materials and thicknesses is a critical skill. Different welding scenarios will require adjustments to either the wire speed or the voltage – sometimes both – to compensate for various materials’ conductivity and melting points. Here is a simplified interpretation guide:
Remember that these are just starting points. Perfecting your settings comes from practice and experimenting with different combinations of wire speed and voltage. Observe the weld bead and adjust if necessary—aiming for a smooth, even bead with proper penetration.
Tips For Using Wire Speed And Voltage Chart
Understanding the relationship between wire speed and voltage in MIG welding is pivotal to mastering welding. An adept welder knows that the right combination can mean the difference between a robust and clean weld and a weak, messy one. The MIG Welding Wire Speed and Voltage Chart is an essential tool that guides you through this harmony. Below are some valuable tips for effectively interpreting and utilizing this chart to improve your MIG welding results.
Maintaining Consistency
Consistency is the backbone of high-quality MIG welding. The wire speed and voltage chart is your roadmap to maintaining a uniform weld. It is crucial to:
- Verify the baseline settings: Start with the recommended settings on the chart based on the wire size and material thickness you are working with.
- Monitor the arc: It should be steady and smooth. Any sputtering or popping indicates a need for adjustment.
- Check for proper penetration and bead profile: Adjust the voltage and wire speed if necessary.
- Document any changes: Keeping track of what settings worked for you will help maintain consistency in future projects.
Fine-tuning Settings For Specific Projects
Each MIG welding project might require subtle changes to the standard settings provided by the chart. To fine-tune these settings:
- Identify the type of metal and its thickness. This determines your starting parameters.
- Adjust the wire speed and voltage incrementally to cater to the nuances of the project.
- Carry out test welds on scrap material of the same type and thickness to ensure the settings produce the desired result.
- Consider external factors such as welding position and draft presence, which might necessitate slight deviations from the chart values.
Remember, the wire speed affects how much metal is fed into the weld pool, whereas voltage governs the arc length and heat input. Balancing these factors will affect the weld’s appearance and, more importantly, its structural integrity.
Inserting a table could be an excellent way to present ideal starting settings visually. Still, as the specifics vary greatly depending on welding equipment, material type, and thickness, such a table isn’t included in this example.
Mastering MIG welding is as much about skill as it is about understanding the science behind it. Use the Wire Speed and Voltage Chart as your guide, and with practice, you’ll be able to make informed adjustments that produce strong, clean welds every time.
Practical Applications And Case Studies
The MIG welding process, which stands for Metal Inert Gas welding, often hinges on two critical settings: wire speed and voltage . Finding the right balance between these parameters transforms a good weld into a great one. To help welders master this technique, professionals often rely on a MIG welding wire speed and voltage chart. However, practical applications and real-world case studies provide further insight into the nuances of these settings, offering a hands-on understanding that charts alone cannot convey.
Real-world Examples
Across industries, from automotive fabrication to construction, MIG welding stands as a cornerstone technique. For instance, in automobile assembly, precise wire speed and voltage are essential for welding car frames, where strength and durability are paramount. One memorable case involved a custom car builder who managed to reduce waste and improve joint quality by making slight adjustments to the MIG settings as suggested by their welding wire speed and voltage chart. The outcome was an exemplary model of efficiency and reliability that other builders strive to replicate.
Challenges And Solutions
However, mastering MIG welding settings is not without its challenges. In one case, a welding workshop experienced frequent issues with spatter and poor penetration until they analyzed their welding technique. By consulting a comprehensive MIG welding wire speed and voltage chart, they recognized that their voltage was too low and wire speed too high for the metal’s thickness. After correcting these settings, the quality of their welds improved dramatically. This is just one demonstration of how understanding and applying the correct settings can dramatically enhance welding outcomes.
Representing a standard case study in tabular format
These case studies highlight the importance of fine-tuning MIG welding techniques. Identifying the correct voltage and wire speed mix streamlines the welding process and ensures high-quality results . By building on the foundation that a MIG welding wire speed and voltage chart provide and adapting it to real-world scenarios, welders can achieve more consistent, durable welds that stand up to the rigors of their intended use.
Exploring Advanced Techniques
MIG welding , or Metal Inert Gas welding, is the go-to for many professionals due to its efficiency and versatility. As you master the basics and move on to advanced welding techniques, you’ll find understanding the intricacies of wire speed and voltage even more crucial. Achieving the perfect weld requires fine-tuning your equipment to match the task. Here, we’ll delve into two advanced MIG welding techniques— Pulse and Dual-shield welding —and how adjusting wire speed and voltage impacts these processes. Let’s decode these sophisticated methods to elevate your welding prowess.
Pulse Welding
Pulse welding is an evolved form of MIG welding alternating between a high peak current and a lower background current. This pulsing action offers greater control over heat input, decreasing the likelihood of warping and allowing for welding on thinner materials.
How do wire speed and voltage come into play with pulse welding? Here’s a brief overview:
- Peak Current: This should align with the wire speed to ensure adequate weld penetration.
- Background Current: It is significantly reduced to cool the weld puddle and prevent burn-through.
Dual-shield Welding
Dual-shield or flux-cored arc welding (FCAW) uses a tubular wire filled with flux and an external shielding gas. It’s a sophisticated technique that combines the benefits of MIG and stick welding and is known for its out-of-position welding proficiency.
Wire-speed and voltage must be synchronized to ensure stable arc characteristics and proper slag coverage, affecting bead shape and quality. Critical factors in dual-shield welding:
In summary, advanced MIG welding techniques like pulse and dual-shield welding demand a precise balance between wire speed and voltage for optimal results. Understanding these relationships paves the way for higher-quality welds and broadens your capabilities as a skilled welder.
Impact Of Incorrect Wire Speed And Voltage
Mastering MIG (Metal Inert Gas) welding requires precise control of wire speed and voltage, two crucial parameters that determine the quality of the weld. Dialing in the correct settings can distinguish between a perfect weld and one that fails to meet standards. Using a MIG welding wire speed and voltage chart is essential, but understanding the consequences of straying from these guidelines is equally important. In this section, let’s delve into the potentially negative impacts and preventive measures one should know while MIG welding.
Weld Defects
Inaccurate wire speed and voltage settings can result in a variety of weld defects:
- Porosity: Pockets of trapped gas in the weld can lead to weak spots.
- Spatter: Excessive spatter causes loss of material and additional cleanup time.
- Lack of Fusion: Incorrect settings may prevent the weld from adequately melting into the base metals, creating weak joints.
- Burn Through: High wire speed or voltage can burn through the material.
- Cold Lapping: On the contrary, low settings might not allow enough penetration, resulting in a bead on top of the metal.
These defects not only compromise the integrity of the weld but can also contribute to further problems like material wastage or the need for rework, ultimately affecting project timelines and costs.
Safety Concerns And Precautions
Incorrect wire speed and voltage settings increase the risk of accidents and hazards:
- A high wire speed coupled with low voltage can lead to wire jamming or ‘bird-nesting,’ which can cause unexpected machine kickback, potentially injuring the operator.
- Excessive spatter from incorrect settings creates more post-weld cleanup and can cause burns or fires if hot metal fragments land on flammable materials or skin.
- Settings that lead to shallow penetration or weak welds could result in structural failure of the welded assembly, posing serious safety risks.
- Adhere to the recommended MIG welding wire speed and voltage chart based on the welded material and thickness.
- Wear appropriate personal protective equipment (PPE), including gloves, a welding helmet with proper shade, and flame-resistant clothing.
- Ensure the work area is clean and free from flammable materials to prevent fires.
- Maintain the welding equipment regularly to avoid malfunctions.
Correct wire speed and voltage are critical for achieving high-quality welds and maintaining a safe welding environment. Well-tuned equipment, along with the proper wire speed and voltage settings from a reliable chart, are indispensable for any welder seeking to produce solid and defect-free welds and to ensure the safety of both the operator and the workplace.
Frequently Asked Questions For Mig Welding Wire Speed And Voltage Chart
What is mig welding wire speed.
MIG welding wire speed refers to how fast the wire is fed through the welder’s gun. The correct rate is crucial for a stable arc and proper penetration. It varies based on material thickness and welding position.
How Does Voltage Affect Mig Welding?
Voltage in MIG welding influences the arc length and the heat input. A higher voltage means a longer arc and more heat, suitable for thicker materials. Correct voltage ensures good bead appearance and penetration.
Can You Adjust Wire Speed And Voltage During Welding?
Yes, wire speed and voltage adjustments can be made during welding to adapt to the workpiece or correct issues. However, significant changes should be avoided to maintain stability.
Why Use A Mig Welding Chart?
A MIG welding chart guides setting the correct wire speed and voltage. It ensures optimal penetration and bead quality by matching settings to material thickness and welding position.
Mastering MIG welding necessitates precision with wire speed and voltage settings. This chart simplifies your path to achieving quality welds. Embrace it as a foundation, experiment, and refine your technique. Keep safety first and quality consistent; your welding projects will reflect your expertise and attention to detail.
Happy welding!
Leave a Comment Cancel reply
Save my name, email, and website in this browser for the next time I comment.

Mig Welder Settings [We Explain The Ones You Need]

Whether you’re new to welding or an experienced welder looking to refine your skills, understanding your MIG welders settings is crucial. In this article, we’ll break down the key factors that govern MIG welding—a process that joins metal with precision and skill.
What are the most important mig welder settings? The most important MIG welder settings are voltage, wire feed speed, and shielding gas flow rate. These settings determine the heat, wire deposition rate, and protection from atmospheric contamination, respectively, crucial for producing strong and clean welds.
As we go along, you’ll learn how to balance voltage and wire feed speed for consistent, strong welds. We’ll also explain the significance of shielding gas flow rates and how they protect your welds.
Additionally, we’ll discuss how material thickness, welding position, and the type of welding wire impact your MIG welder settings.
Don’t worry if it sounds complex right now; we’ll guide you step by step. So, let’s dive into the practical world of MIG Welder Settings. By the end of this article, you’ll have the knowledge to confidently configure your MIG welder for various projects, creating reliable and professional-quality welds.

Understanding Your Mig Welder
When it comes to Mig welding, familiarity with your welding machine is the first step towards success.
A typical Mig welder consists of several crucial components that work in harmony to create those strong, precise welds you’re aiming for.
Understanding these components will provide you with a solid foundation for adjusting your Mig welder settings effectively.
- Power Source: This is the heart of your Mig welder, supplying the electrical energy needed for welding. It’s usually connected to a standard power outlet, and its output can be adjusted to suit your welding needs.
- Wire Feeder: The wire feeder is responsible for feeding the welding wire through the welding gun. It ensures a constant, controlled flow of wire during welding, a key factor in maintaining a stable arc.
- Welding Gun: The welding gun is your point of control, where you direct the arc to create the weld. It houses the contact tip, which makes contact with the workpiece and initiates the electrical arc.
- Gas Regulator and Flowmeter: If you’re using shielding gas for your Mig welding, you’ll find these components crucial. The gas regulator controls the pressure of the shielding gas, while the flowmeter lets you monitor and adjust the gas flow rate.
Understanding certain key terms is essential for making informed decisions about your Mig welder settings.
Let’s break down three fundamental terms you’ll encounter:
- Voltage: Voltage, measured in volts (V), determines the electrical potential difference between the welding electrode (wire) and the workpiece. It plays a significant role in controlling the heat generated during welding. Higher voltage settings create a hotter, more penetrating arc, while lower voltage settings produce a cooler, shallower arc.
- Amperage: Amperage, measured in amperes (A), refers to the amount of electrical current flowing through the welding circuit. It directly affects the size and strength of the weld bead. Higher amperage settings result in a larger, more robust weld, while lower amperage settings create smaller, more delicate welds.
- Wire Feed Speed: Wire feed speed, measured in inches per minute (IPM) or centimeters per minute (CPM), controls the rate at which the welding wire is fed into the arc. This setting influences the size and consistency of the weld puddle. Increasing the wire feed speed increases the rate of deposition, while decreasing it reduces the rate.
How to identify and locate these settings on your welder
Now that you’re acquainted with the terminology, let’s get practical. Finding and identifying these critical settings on your Mig welder is vital before you can start adjusting them with confidence.
- Refer to the Manual: The first step should always be consulting your Mig welder’s user manual. It’s a treasure trove of information specific to your machine. It will guide you to the location of voltage, amperage, and wire feed speed controls.
- Control Panel: Most Mig welders feature a control panel, often located on the front or top of the machine. On this panel, you’ll typically find knobs or digital displays for adjusting voltage and wire feed speed. Amperage settings may also be present here or on a separate panel.
- Wire Feeder: As the wire feeder is directly linked to wire feed speed, you’ll often find wire feed speed adjustments integrated into the wire feeder itself. Look for knobs or dials that allow you to fine-tune the wire feed speed.
- Gas Regulator and Flowmeter: If you’re using shielding gas, the gas regulator and flowmeter are usually connected to the gas cylinder. These components have clear pressure and flow rate adjustment mechanisms .
Voltage Settings
Voltage is a pivotal factor in Mig welding, influencing the heat generated by the electrical arc. Understanding its role is crucial for achieving the desired weld quality:
How to Choose the Right Voltage Setting
Selecting the correct voltage setting is a skill that develops with experience. Here’s a step-by-step process to help you make informed choices:
Real-World Examples of When to Adjust Voltage
To put voltage adjustments into perspective, here are some real-world scenarios where modifying the voltage setting can improve your welds:
Troubleshooting Common Voltage-Related Issues
While mastering voltage settings, you might encounter some common issues. Here’s how to troubleshoot and address them:
Amperage Settings
The Significance of Amperage in Mig Welding
Amperage, measured in amperes (A), is a critical parameter in Mig welding, directly impacting the size, strength, and quality of your welds. Understanding its significance is essential for achieving optimal results:
Selecting the Appropriate Amperage for Your Project
Choosing the right amperage setting is crucial for the success of your Mig welding project. Here’s a systematic approach to help you make the best selection:
Demonstrating Amperage Adjustments with Practical Scenarios
To better grasp the impact of amperage adjustments, let’s explore some practical scenarios where modifying the amperage setting can enhance your welding outcomes:
Addressing Amperage-Related Challenges and Solutions
As you gain experience in adjusting amperage settings, you may encounter common issues. Here’s a troubleshooting guide to help you resolve amperage-related challenges:
Wire Feed Speed Settings
The Importance of Wire Feed Speed for Weld Quality
Wire feed speed is a crucial parameter in Mig welding, directly influencing the quality and consistency of your welds. Understanding its importance is essential for achieving desired results:
How to Determine the Correct Wire Feed Speed
Selecting the appropriate wire feed speed is crucial for achieving optimal weld quality. Here’s a systematic approach to help you determine the correct setting:
Hands-On Examples of Adjusting Wire Feed Speed
To better understand how wire feed speed adjustments impact your welding, let’s explore some hands-on examples in various welding scenarios:
Dealing with Common Wire Feed Speed Problems
As you become more adept at adjusting wire feed speed, you may encounter some common issues. Here are solutions to address wire feed speed-related challenges:
Shielding Gas Settings
Shielding gases play a vital role in Mig welding, serving to protect the weld pool from atmospheric contamination. An introduction to these gases will help you understand their importance:
Types of Shielding Gases and Their Applications
There are various types of shielding gases available for Mig welding, each with its own set of characteristics and applications:
Guidelines for Choosing the Right Shielding Gas
Selecting the appropriate shielding gas is essential for achieving quality welds. Here are some guidelines to help you make an informed choice:
Troubleshooting Gas-Related Issues
While working with shielding gases, you may encounter some common issues. Here’s how to troubleshoot and resolve gas-related problems:
MUST READ: Do you have to use gas to weld!?
Welding Technique and Settings Interaction
Explaining the Relationship Between Settings and Welding Technique
Understanding how welding technique and settings interact is crucial for achieving precise and consistent results in Mig welding. Let’s delve into the intricacies of this relationship:
- Arc Length: The distance between the welding gun’s contact tip and the workpiece affects the arc’s stability. Longer arcs require higher voltage settings, while shorter arcs demand lower voltage settings.
- Travel Speed: The rate at which you move the welding gun along the joint influences the weld’s appearance and penetration. Slower travel speeds often require higher wire feed speed settings for proper deposition.
- Work Angle: The angle at which you hold the welding gun relative to the joint affects the heat input and penetration. A slight push angle might necessitate higher amperage settings for deeper penetration.
- Welding Position: Different positions (flat, horizontal, vertical, overhead) influence the direction of heat and molten metal. Adjust settings accordingly to maintain control and prevent weld defects.
How to Fine-Tune Settings Based on Your Welding Style
Adapting settings to your welding style is a skill that evolves with experience. Here’s how to fine-tune settings to match your technique:
- Experiment and Observe: Begin with recommended settings and gradually make small adjustments while closely observing the results. Keep notes on what works best for your style.
- Practice Welding Techniques: Practice various welding techniques such as stringer beads, weave beads, and circles to understand how settings affect each method differently.
- Learn from Others: Seek guidance from experienced welders or mentors who can provide insights into fine-tuning settings based on your specific style and project requirements.
- Stay Consistent: Consistency in your welding technique is key. Aim to replicate successful welds by maintaining a consistent approach to settings and motion.
Troubleshooting Common Mig Welder Setting Issues
Mig welding is a versatile process, but even with the right settings, issues can arise.
Understanding the potential causes is the first step in troubleshooting:
Practical Solutions for Issues Such as Spatter, Poor Penetration, and Irregular Bead Formation
Troubleshooting common Mig welding issues involves practical solutions that address both the symptoms and underlying causes:
As we wrap up our look into MIG Welder Settings, you now have the know-how to confidently navigate this essential territory.
From controlling voltage to adjusting wire feed speed and managing shielding gas flow rates, you’ve uncovered the fundamental elements for top-notch welding. These settings, sometimes seen as technical, are your tools to craft clean, strong welds.
As you embark on your welding projects armed with this newfound knowledge, remember that practice and experience are your best teachers.
Experimentation and fine-tuning will help you master your MIG welder. Whether you’re welding for structural strength, artistic expression, or industrial needs, your ability to configure your MIG welder settings will make all the difference.
So, as you stand ready for your welding journey, welder in hand, let your passion for the craft and your commitment to professionalism guide you. The world of welding is yours to explore, and your expertise in MIG Welder Settings will ensure the structures you create endure and impress.
Frequently Asked Questions
How often should i calibrate my mig welder settings.
Calibration frequency can vary depending on usage, but a monthly calibration check is a good starting point. Regularly inspect your welder, and if you notice inconsistencies in your welds, perform calibration checks as needed.
What should I do if I encounter excessive spatter during welding?
To reduce spatter, slightly lower your wire feed speed and adjust voltage and amperage settings for a smoother arc. Additionally, ensure your work surface is clean, and replace worn contact tips or liners if necessary.
What can I do to improve poor penetration in my welds?
If you’re experiencing poor penetration, increase the amperage setting for more heat and penetration depth. Adjust the wire feed speed to provide sufficient filler metal, maintain a consistent travel speed and angle, and ensure proper joint preparation and material cleanliness.
Similar Posts

MIG Welding Gas Pressure: What You Need To Know
One critical element in welding is the gas pressure you employ during MIG welding. Gas pressure plays a pivotal role in MIG welding as it directly affects the quality and strength of the weld. But, why is gas pressure important in MIG welding? Gas pressure plays a pivotal role in MIG welding as it directly…

MIG Welding Titanium: A How-To Guide!
MIG welding, a widely-used technique for its efficiency, takes on a more complex dimension when applied to titanium. In this guide, we’ll focus on the essentials of MIG welding with this metal, known for its high strength and light weight properties. Titanium presents unique challenges due to its high melting point and sensitivity to atmospheric…

MIG Welding Safety: Essential Tips for Aspiring Welders
If you’re here, it’s because you understand the vital importance of working safely when dealing with the heat and molten metal involved in welding. So, let’s address a fundamental question: Why should you prioritize MIG welding safety? The answer is plain and simple: Safety ensures that you, your fellow welders, and your workspace stay protected…
![mig welding travel speed chart How to MIG Weld Stainless Steel? [Explained]](https://weldingwatch.com/wp-content/uploads/2023/12/how-to-weld-stainless-steel-768x384.jpg)
How to MIG Weld Stainless Steel? [Explained]
MIG welding is a popular welding process that is used to join metals together. It is a relatively easy process to learn and is commonly used in many industries. However, welding stainless steel with MIG can be a bit more challenging than welding other metals due to its unique properties. One of the most important…
![mig welding travel speed chart How to MIG Weld Aluminium? [Explained]](https://weldingwatch.com/wp-content/uploads/2023/12/mig-welding-aluminium-768x384.jpg)
How to MIG Weld Aluminium? [Explained]
Aluminum, a metal known for its lightweight and high strength, plays a vital role in various industries, from aerospace to automotive. It’s a go-to material for many applications, but working with it requires a distinct approach compared to other metals like steel or iron. Why? Aluminum has a unique set of physical properties – it’s…

How to Reduce Spatter When MIG Welding
When it comes to welding, spatter is a common adversary. It’s those tiny molten metal droplets that spray out during the welding process, often landing where you least want them—on your workpiece, your workspace, or even yourself. The importance of spatter reduction cannot be overstated. Excessive spatter not only mars the appearance of your welds…
Leave a Reply Cancel reply
Your email address will not be published. Required fields are marked *
Save my name, email, and website in this browser for the next time I comment.

"The Business of Metal Manufacturing"
- Additive Manufacturing Systems
- Automation/Robotics
- CAD/CAM Software
- Coil Handling Equipment
- Cut-To-Length Lines
- Deburring Machines
- Heat Treating
- Ironworkers
- Laser Cutting Systems
- Oxyfuel Cutting Systems
- Plasma Cutting Systems
- Press Brakes, Panel Benders
- Punch Presses
- Sawing Systems
- Stamping Presses
- Tube & Pipe Fabrication
- Turret Presses
- Engine Driven Welders
- Filler Metals/Electrodes
- Inverter Welders
- MIG Welders
- Plasma Cutters
- Power Sources
- Resistance Welders
- TIG Welders
- Welding Gloves
- Welding Guns/Torches
- Welding Helmets
- Wire Feeders
- Drilling Machines
- Gear Cutting Machines
- Grinding Machines
- Honing Machines
- Horizontal Machining Centers
- Laser Cutting
- Machine Controls
- Milling Machines
- Multitasking Machines
- Ram EDM Machines
- Turning Centers
- Vertical Machining Centers
- Wire EDM Machines
- Cutting Tools
- Drilling Tools
- Fixturing Systems
- Abrasives, Belts, Brushes, Grinding Wheels
- Positioners
- Punches and Dies
- Threading Tools
- Vises and Vise Jaws
- Ballbar Systems
- Bore Gauges
- Calibration
- Coordinate Measuring Machines
- Dial Indicators
- Go/No Go Gauges
- Laser Scanners
- Non-Destructive Testing
- Other Gauges and Gauging Equipment
- Surface Roughness/Finish
- Compressed Air
- Computerized Maintenance Management Systems
- Indoor Air Quality
- Industrial Cleaning/Waste Removal
- Lubricants, Coolants, Metalworking Fluids
- Machine Tool Repair and Rebuilds
- Roof Systems
- Spindle Repair and Rebuilds
- Adjustable Guards
- Body Protection
- Eye and Face Protection
- Fixed Guards
- Foot and Leg Protection
- Hand and Arm Protection
- Head Protection
- Hearing Protection
- Interlocked Guards
- Moveable Barriers and Gates
- Presence Sensing Devices
- Pullbacks/Restraints
- Regulatory Compliance
- Safety Mats
- Safety Trip Controls
- Self-Adjusting Guards
- Two Hand Controls
- General Lifts
- Hand Lift Trucks
- Other Material Handling Equipment
- Racks and Storage Equipment
- White Papers
- Supplier Directory
Category Menu

Pre-Calculating Wire-Feed Speed, Travel Speed and Voltage
It is possible for manufacturers that are welding with solid wire or flux-cored wire to calculate the starting wire-feed speed and travel speed? These calculations will get you close, but some tweaking may have to be done to achieve your desired weld.
Posted: December 1, 2010

A shop would like to decrease the development time for new MIG welds. Is there a way to pre-calculate wire-feed speed, travel speed and voltage, to get them close before they strike the first weld?
Yes, it is possible to calculate starting wire-feed speed and travel speed. This is a very common question from manufacturers welding with solid wire or flux-cored wire. Most welding professionals know the wire-feed speed (WFS), where a process runs well based on their experience, or can quickly get WFS from the manufacturer’s recommended procedures.
However, determining how fast to travel for a particular size weld bead ends up being an iterative, time-consuming process. By understanding a few concepts and doing some math with a few simple formulas, we can determine at least a good starting point for a welding procedure that produces the desired weld.
DEPOSITION RATE It is essential to recall that Deposition Rate is directly proportional to the speed at which a particular wire diameter emerges from a welding gun during welding. Deposition rate has nothing to do with how fast the gun is traveling, nor the voltage setting on the machine. Deposition rate is simply a measure of how many pounds of wire come from the welding gun in a certain amount of time, typically measured in lb/hr.
If wire-feed speed increases, deposition rate increases. We also understand that if we maintain the wire-feed speed and change to a larger diameter wire, deposition rate will increase as well. Armed with this understanding, calculating deposition rate ends up being a very powerful exercise that gives you a number that can be used to calculate key welding parameters. Let’s look at the formula and an example:
Deposition Rate Calculation Deposition rate (lb/hr) = 13.1 × (Wire diameter) 2 × (Wire-feed speed) × (Efficiency) — Wire diameter in inches (in) — Wire-feed speed in inches per minute (ipm) — Efficiency (1.0 for solid wire, 0.85 for cored wire) — This calculation is for steel only — e.g. : Wire diameter = 0.045 in (1.2 mm) solid wire, WFS = 300 ipm
Deposition rate = 13.1 × (0.045) 2 × (300) × (1.0) = 7.96 lb/hr
Calculating Travel Speed With Deposition Rate Knowing the deposition rate, we can calculate the travel speed in inches per minute (ipm) for a particular weld. Let’s say we want to make a 3/8 in steel fillet weld (assume 10 percent reinforcement or 0.4125 in leg) using 0.045 in solid wire at 300 ipm, the weight of weld metal per foot can be calculated by multiplying the density of steel (0.283 lb/in 3 ) by the volume of weld metal per foot as follows:
Weld Weight Per Foot Calculation Volume of weld metal/ft = 1/2 × b × h × 12 in = 1/2 × 0.4125 in × 0.4125 in × 12 in = 1.02 in 3
Weight of weld metal/ft of 3/8 in fillet weld = (0.283 lb/in 3 ) × (1.02 in 3 ) = 0.2887 lb/ft
From the calculation below, we see that the travel speed for a one-pass, 3/8 in fillet weld would be 5.52 ipm, 11.03 ipm for a two-pass fillet weld, or 16.55 ipm for a three-pass weld.
Travel Speed Calculation Travel speed = (deposition rate) × (# of passes)/5 × (weight of weld metal per foot {lb/ft}) = Travel speed = {7.96 x 1} / {5 x 0.2887} = 5.52 ipm
CALCULATING WIRE-FEED SPEED WITH DEPOSITION RATE Let’s assume a requirement to make fillet welds at a rate of 12 lb/hr using 0.045 in welding wire. We can calculate the WFS using the formulas below and Weight of Weld Wire per foot in Table 1 .
Wire-Feed Speed Calculation Wire-feed Speed = (deposition rate)/5 × (weight of wire per foot {lb/ft}) = (12)/5 × (0.0054) = 444.4 ipm
Of course, the travel speed for a one-pass 3/8 in fillet weld at a 12 lb/hr deposition rate would be 8.31 ipm as calculated below: Travel Speed = (deposition rate) × (# of passes)/5 × (weight of weld metal {lb./ft}) = (12) × (1)/5 × (0.2887) = 8.31 ipm
MAKING IT EASIER The Bartonian Conversion Factor (see Table 2 ) makes things a bit easier for fillet welds. The example below uses the conversion factor to calculate travel speed at 5.57 ipm for that same 3/8 in fillet weld using a 0.045 in solid wire.
Travel Speed = 7.96 × 0.7 = 5.57 ipm (.2887)
Weight of weld metal per foot can be calculated for any joint type by calculating the volume and multiplying by the density of the weld metal (eg. 0.283 lb/in 3 for steel). However, the values shown in Table 3 through Table 6 eliminate the need to do the calculation. These values are taken from Table 12-1 in The Procedure Handbook of Arc Welding by the Lincoln Electric Co., and show the Weight of Weld Metal per Foot for several common joint types welded with steel. The following sample calculations use Tables 3 through 6 .
SAMPLE CALCULATION NO.1 1/2 in plate Vee groove weld with 90 deg included angle and 1/8 in reinforcement using 0.052 in solid wire, 90%Ar/10%CO 2 shielding gas. Manufacturer recommends WFS at 325 ipm and 30 volts.
Deposition Rate (lb/hr) = 13.1 × (0.052) 2 × (325) × (1.0) = 11.51 lb/hr
Travel Speed for fill and cap passes = (11.51) × (6)/5 × (0.849 + 0.199) = 13.18 ipm
SAMPLE CALCULATION NO.2 3/8 in plate square butt weld into a backing, with a 3/16 in gap and 1/8 in reinforcement using 1/16 in cored wire, 75%Ar/25%CO 2 shielding gas. Our process runs great with WFS at 285 ipm and 26 volts.
Deposition rate (lb./hr) = 13.1 × (1/16 in) 2 × (285) × (.85) = 12.39 lb/hr
Travel speed for fill and cap passes = (12.39) × (1)/5 × (0.239 + 0.053) = 8.49 ipm
SAMPLE CALCULATION NO.3 What should my wire-feed speed be if I want to make a fat, 1/4 in fillet weld at 20 ipm travel speed using 0.045 in solid wire and 90%Ar/10%CO 2 shielding gas?
Re-arranging the Travel Speed calculation above to solve for Deposition Rate we get: Deposition rate = 5 × Travel speed × (Weight of weld metal {lb/ft})/(# of passes) = 5 × 20 ipm × (0.165)/1 = 16.5 lb/hr
Re-arranging the Deposition Rate calculation above to solve for Wire-feed Speed we get: Wire-feed speed = Deposition rate/13.1 × (Wire diameter) 2 × (Efficiency) = 16.5/13.1 × (.045 in.) 2 × (1) = 622 ipm
SUMMARY Using math and these simple formulas can reduce your weld-development time, and improve your pre-WPS documentation. These calculations will get you close, but some tweaking may have to be done to achieve your desired weld. Having a good starting point for welding procedure development will decrease time and guesswork on the shop floor.
Subscribe to learn the latest in manufacturing.
Industry news.

IMTS 2024 Conference Registration and Visitor Housing Now Open
Registering in advance provides a discount and includes full access to the IMTS exhibit halls. IMTS is being held September 9-12 in Chicago.

Industrial Magnetics Expands East Coast Presence with New Regional Manager
Bill Dunlap has been named IMI’s regional manager of North Carolina, South Carolina and Virginia.

HAIMER’s Tool Room now with WinTool and Toolbase System
HAIMER acquires 25% of WinTool AG and agrees on a global strategic partnership with the TCM Group.
Sign Up For e-Newsletter
Calendar & events, design-2-part show, international manufacturing technology show (imts), fabtech 2024.

- Where to buy
- Partner Login
- Construction & Fabrication
- Heavy Equipment
- Manufacturing
- Transportation
- Marine & Shipbuilding
- Home, Farm & Ranch
- Oil & Gas
- Education & Training
- Carbon Steel, All Position
- Carbon Steel, Flat and Horizontal
- Low Alloy, All Position
- MEGAFIL® : Seamless Technology
- Build-Up Electrodes
- Overlay Electrodes
- Build-Up Wires
- Overlay Wires
- Gas-Shielded Wires, Carbon Steel
- Gas-Shielded Wires, Low Alloy
- Solid Wires
- Stainless Steel Electrodes
- Stainless Steel Solid Wires
- Stainless Cored Wires
- Mild Steel Electrodes
- Low Hydrogen Electrodes
- Low Alloy Electrodes
- Submerged Arc Flux
- Submerged Arc Cored Wires
- Submerged Arc Solid Wire
- Submerged Arc Hardfacing
- Product Search
- Base Material Cross Reference
- Hardfacing Product Cross Reference
- Selection Guide
- Alloy Surcharges (U.S. Dollars)
- Literature Request
- Case Studies
- Flyers & Brochures
- Handling, Storage & Packaging
- Posters & Charts
- Video Stories
- Part & Lot Numbers Guide
- Actual Cert. Search
- Technical Articles
- Technical Guides
- Product Approvals Guide
- HBC Safety Quick-Guide
- Safety Data Sheets
- Proposed Change to the Threshold Limit Value for Manganese
- Chromium (VI) Bulletin
- OSHA Chromium (VI) Standard
- OSHA Shipyard Employment on Chromium (VI) Standard
- OSHA Occupational Safety and Health Regulations for Construction on Chromium (VI)
- OSHA Compliance Guide for Small Entities on Chromium (VI)
- OSHA Chromium (VI) Information
- AWS/ANSI Z49.1 Safety in Welding, Cutting, and Allied
- AIHA Consultant Listing
- History of Hobart
- Team Member Stories
- Hobart Facilities Map
- Customer Support Team
- Regional Offices
- Company Store
- News & Events
- Welding Group Partners
- Job Opportunities
- Terms & Conditions – Sale
- Terms & Conditions of Site Use
- Privacy Policy
- ISO 9001:2015
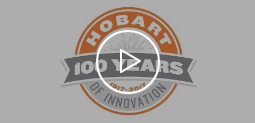
- Hobart Brothers LLC 101 Trade Square East Troy, OH 45373 (937) 332-4000 [email protected]

Home > Resources > Technical Articles > Tips for Setting MIG Welding Parameters for Thin Materials
Technical Article
View Case Studies, Video Stories, Technical Articles for guidance on welding various metals and what filler metals to use in your industry.
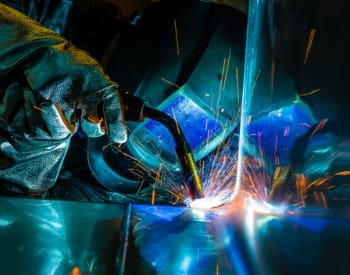
Tips for Setting MIG Welding Parameters for Thin Materials
By: Hobart Brothers Comments (0) -->
Material thicknesses in fabrication and manufacturing can vary widely according to the application — and each has its own intricacies when it comes to MIG welding it.
Thinner materials, in particular, pose some unique challenges. From the potential for distortion to the risk of burnthrough and more, it’s easy to make mistakes. That’s why it’s important to have a solid understanding of proper welding parameters to ensure good weld quality and productivity.
So, what is considered thin material and where is it used most?
The American Welding Society (AWS) defines it as 3/16 inch or thinner in its AWS D1.3/D1.3M: 2018 Structural Welding Code – Sheet Steel.
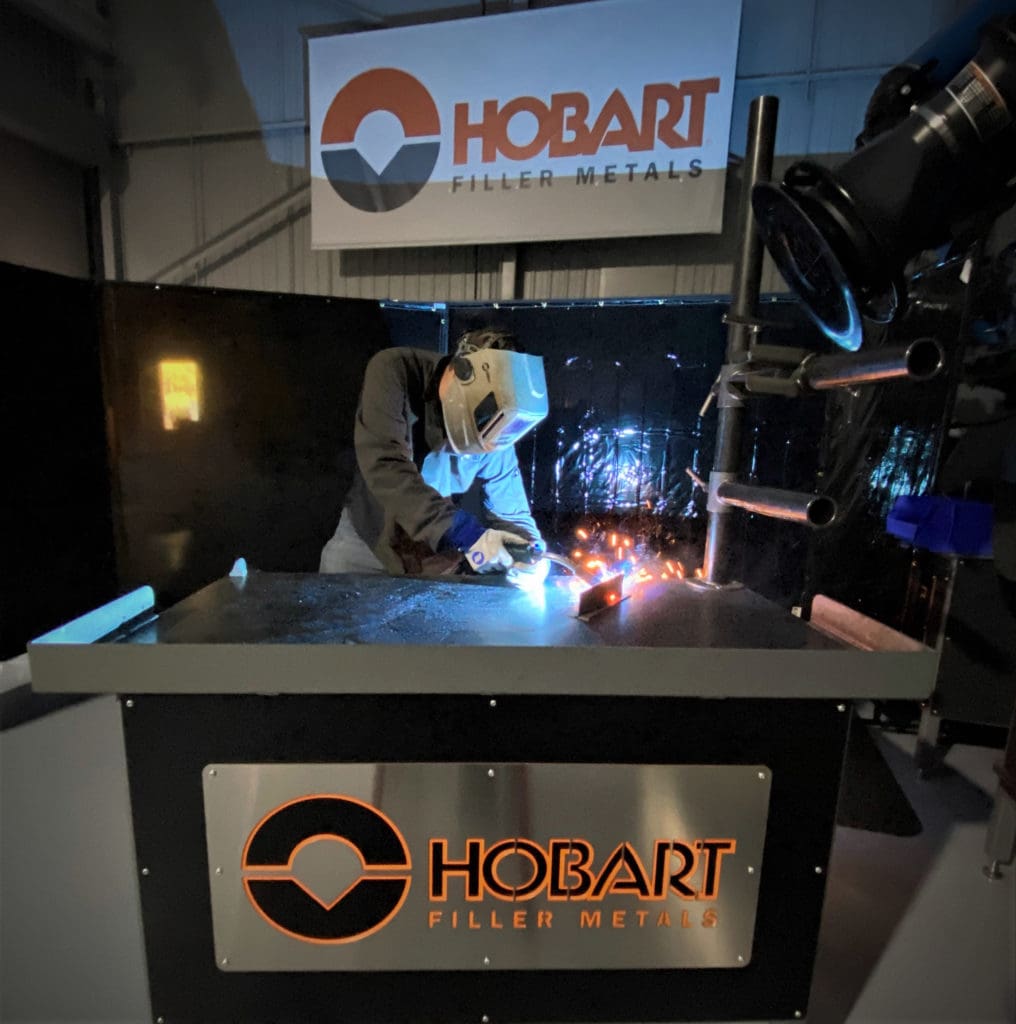
Thin materials, such as basic carbon steel, are often used in automotive frames and panels, consumer goods, light structural components and ancillary connections.
As when welding other materials, getting the best results with thin materials depends on correct voltage, amperage and travel speed — along with other factors.
Common mistakes and consequences Improper heat input is among the biggest culprits when it comes to problems with welding thin materials. High heat input can be caused by an excessive voltage or amperage setting, too slow a travel speed and/or needlessly long welds — and each can lead to burnthrough. Distortion, which occurs when the material expands and contracts as a result of welding and subsequent cooling, can also be amplified by high heat input. With distortion comes issues such as poor fit-up between joints that may lead to downtime for rework.
Setting the voltage and amperage lower reduces heat input but can cause a ropey weld bead appearance. It can also lead to lack of penetration and, potentially, spatter. Conversely, if a welding operator sets the voltage too high, it may lead to undercut and a concave weld bead shape.
With all these potential pitfalls, it’s important to employ welding parameters (including voltage) that can balance heat to gain the best weld quality.
Best practices When welding any type or thickness of material, it is always a good idea to reference weld procedure specifications (WPS) when they are available. Thin material welding is no exception. These documents can provide the welding parameters necessary to complete a weld correctly and consistently for a given application and joint design. A WPS offers the recommended operating window — or maximum and minimum voltage and amperage settings — that will help yield the best results.
Consulting the product data sheet for the filler metal being used is also recommended. These provide key information, such as the welding positions the filler metal can be used in, shielding gas options, welding current, and optimal voltage and wire feed speed ranges for a given wire diameter.
A combination of small-diameter solid welding wires — 0.024-, 0.030- and 0.035-inch — with a power source offering a short-circuit transfer mode is well suited for welding thin materials. Small-diameter wires are ideal since they don’t require as much amperage and voltage to melt off the wire into the molten weld pool. The same holds true for the short circuit transfer mode. It operates at lower welding parameters than other modes of transfer, specifically wire feed speed and voltages. Together, these factors keep heat input lower. Short circuit transfer is slower than other methods but is versatile since it allows welding operators to weld in all positions when using solid wires with or without pulsed waveforms.
The welding parameters vary for each of the recommended wire diameters and also depend on how thin the material is.
For example, both 0.024- and 0.30-inch solid wires can be used to weld 24-gauge material using a welding current of 30 to 50 amps and travel speeds of 10 to 20 inches per minute (ipm). The voltage and wire feed speed vary though. A 0.024-inch wire would operate at 13 to 15 volts (electrode positive) with a wire feed speed of 130 to 160 ipm, whereas the 0.30-inch solid wire would require 15 to 17 volts and 75 to 100 ipm wire feed speed. These parameters would work well for single-pass flat and horizontal fillet welds.
The wire diameter used will necessarily increase as the material thickness increases. The same holds true for the welding parameters, which will run hotter. For instance, a 3/16-inch piece of material could be welded with a solid wire (0.035-inch diameter) at 140 to 175 amps and 19 to 22 volts. A recommended wire feed speed would fall in the range of 240 to 290 ipm with travel speeds between 14 and 19 ipm.
A good rule of thumb is to keep the welding wire stickout at 5/8 inch or shorter for small diameter wires. It helps control amperage and with it, heat input and more. Too long of a stickout lowers the amperage, which reduces penetration but fights against the voltage setting used. This prevents the weld from wetting out and filling the toes of the weld. Poor weld bead wetting leads to quality issues such as cold lap. A long stickout can also prevent proper shielding gas coverage, which causes contaminated welds and rework.
Regardless of the diameter of solid wire used in conjunction with a short circuit process, the shielding gas recommendations are the same. Using a mixture of 75% argon and 25% CO 2 is common. Some welding operations may opt for a mixture of 90% argon with 10% CO 2 if there are spray transfer or pulsed-spray transfer welding applications, along with short circuit ones. This allows for standardizing on one shielding gas mixture. When using higher levels of argon on a short circuit application, the welding operator should lower voltage settings since this gas runs hot and can increase heat input.
Putting it all together Welding thin materials doesn’t have to be intimidating. Following a WPS and filler metal spec sheets are a good basis for success. For welding operators who are newer to the process or those who don’t weld on a regular basis, it may take some time to tune in the welding parameters and technique. Remember to consult with a trusted welding distributor, filler metal manufacturer or equipment manufacturer with any questions about welding thin materials. They often have dedicated personnel who can help.
Don't forget to share!
Privacy overview.

Need help finding the right product?
- MULTI-PROCESS WELDERS
- MIG WELDERS
- TIG WELDERS
- STICK WELDERS
- PLASMA CUTTERS
- PULSE MIG WELDERS
- SPOT WELDERS
- FUME EXTRACTION
- WELDING HELMETS
- PROTECTIVE APPAREL
- WORKSHOP SAFETY
- PROFESSIONAL GAS KITS
- GAS CUTTING MACHINES
- GAS EQUIPMENT ACCESSORIES
- MIG TORCH CONSUMABLES
- TIG TORCH CONSUMABLES
- TIG TUNGSTEN ELECTRODES
- PLASMA TORCH CONSUMABLES
- REGULATORS & FLOWMETERS
- MIG TORCHES
- TIG TORCHES
- PLASMA TORCHES
- STICK WELDING ACCESSORIES
- MIG WELDING ACCESSORIES
- TIG WELDING ACCESSORIES
- AIR FILTERS
- WELDING TROLLEYS AND WATER COOLERS
- MIG WELDING WIRE
- TIG WELDING RODS
- STICK WELDING ELECTRODES
- PRIVACY POLICY
- WARRANTY TERMS
- WARRANTY REGISTRATION
- BATCH CERTIFICATE
- Material Data Safety Sheets (MSDS)
- VIDEO SETUP GUIDES & TUTORIALS
- DISCONTINUED PRODUCT MANUALS
The Ultimate Guide to MIG Welding
March 2, 2021
There are a few factors that will influence the type of welding that will work best for you. How big is the job? Are you welding indoors or outdoors? How thick is the metal you want to weld? What’s your budget? These are all things to consider when deciding which type of welder you’ll need.
Quick Navigation
Machine setup.
- Torch Setup
- Weld Preparation
Making the Weld
What is mig welding.
Metal Inert Gas (MIG) welding is an arc welding process in which a solid wire (the filler metal) is continuously fed through the welding machine and into the weld pool that’s created by the arc to form a weld.
The process of MIG welding is semi-automatic, as the machine does all the wire feeding for you. This is why MIG welding is considered one of the easiest types of welding to learn and a great place to start for beginners.
- Gas vs gasless
- Voltage/wire speed setup
1. Gas vs Gasless
There are two ways to MIG weld. The first (and most common) is with gas. The gas is used to shield the weld metal from any outside contaminants when welding. The second is gasless, and the filler metal used has a flux core, which protects the weld instead of gas.
If you’re using a shielding gas for your weld, there are a few to choose from, as different metals require different shields. The best gas to use for mild steel and stainless steel is a mixture of argon and carbon dioxide (75% Ar/25% CO2); however, straight carbon dioxide works as well. You can also add a small amount of oxygen to the ArCO2 mix. If you’re welding with aluminium, then you’ll need pure argon for your shielding gas.
When you’re using gas, all you need to do is attach the regulator to the tank, attach the gas hose from the welding machine to the regulator and set your gas flow. Every UNIMIG machine (except the VIPER 135) comes with a gas regulator, so don’t worry about having to buy your own.
The regulator comes with two dials. One shows how much gas is still in the tank, and the second shows your gas flow rate. Twist the regulator valve to set how much gas flow you want for the weld. UNIMIG recommends an 8-12L per minute gas flow rate for all MIG welding, and these recommended settings can be found on the guide table inside each machine.
If you’re welding outdoors with gas, you’ll find you may need to turn up the gas flow or set up a cover, as the breeze can affect how much gas is reaching the weld pool. If you’re shielding gas is being blown away, then the weld will be prone to defects like porosity (the Swiss cheese look).
The polarities will also require different setups depending on whether you have chosen gas or gasless welding. Gas welding with aluminium, stainless steel, and mild steel all require an electrode positive polarity. This means that you need to insert the polarity cable into the Positive (+) panel mount and the earth clamp (which comes provided) into the Negative (–) panel mount.
If you are using gasless wire, then the polarity is switched; the polarity cable would go into the Negative (–) and the earth clamp into the Positive (+) . While some machines are limited to gas or gasless only, at UNIMIG, all of our MIG welders are capable of both processes . A good example is the VIPER 185 MIG/TIG/Stick Welder , a multi-process machine made specifically for home welders, which will let you trial every type of welding you can think of (except AC TIG).
Regardless of whether you are using gas or gasless wire, your earth clamp will need to be attached to your workpiece (the metal you’re welding) or something metal that will conduct to your workpiece nearby; otherwise, the machine won’t weld.
Each roller comes with two grooves; these are the wire sizes (e.g. 0.6mm & 0.8mm). You’ll need to make sure the roller groove size is the same as the wire you are using. To replace a roller, unscrew the retaining cap and take the old roller off. Place the new roller on (lining up the keyway on the roller with the key on the machine) and re-screw the retaining nut.
MIG welding torches come with a Euro connection that plugs directly into the front of the machine.
3 types of MIG torches
- Binzel style
- Tweco style
- Bernard style
The main difference between these three torch types is that they were initially made by different manufacturers. Though the consumables for each look the same, you have to match your consumable type to the torch type; otherwise, they won’t fit.
Every UNIMIG MIG machine comes with a Binzel style torch, but all three are available for purchase.
A liner guides your wire inside the torch lead, and this liner ensures the wire makes it out of the torch tip. You may need to change your liner before you feed your wire through, as these liners – much like the rollers – will only fit specific sizes.
Let’s use an example. The RAZOR MULTI 220 has a wire size range of 0.6mm-1.2mm. If you started with a weld that only needed 0.6mm wire and then changed to a weld that needed 1mm wire, you’d need to change liners.
To change a liner:
- Remove MIG torch front end parts.
- Remove the liner retaining nut.
- Carefully pull out and completely remove the existing liner. Ensure MIG torch is completely unravelled until setup is complete.
- Carefully feed in the new liner down the torch lead all the way to exit the torch neck.
- Fit the liner retaining nut and screw only 1/2 way down.
- Snip the excess liner off, about the length of the where tip holder sits past the end of the torch neck.
- Replace the front end parts.
- Fully screw down the liner retaining nut and nip it up tight. This compresses the liner inside the torch cable assembly preventing it from moving during use and ensures good wire feed.

When you’re changing your liner, it’s best to keep the torch entirely straight and go slowly, as you don’t want to kink the liner itself.
There are separate liners for steel wires and aluminium wires. If you’re going to use a standard MIG torch for an aluminium wire, you’ll need an aluminium specific liner (in the correct size).
This liner goes in and out the same way as steel liners, but you have to attach a neck spring on the top of the liner before inserting it. The neck spring keeps the liner ridged so it can be fed into the torch with no issues and keeps the wire from kinking.
When you’re welding, try to keep the torch hose as loosely looped (or straight) as possible because it will minimise the chance of kinking the wire inside.

As well as your standard MIG torches, you can also get an aluminium specific torch, called a ‘spool gun’. Spool guns are set up slightly differently than the MIG torches, as the wire spool is not connected in the machine but in the gun itself.
The spool holder can only hold 1kg rolls, so if you’re doing a lot of aluminium welding , it’ll run out faster than in a machine, and the gun is going to fatigue your hands faster.
The benefits of a spool gun for aluminium are worth it, though. Aluminium is a softer metal than steel, so it has its own roller grooves and specific torch liners. The softness of aluminium means that it’ll kink way easier than steel will in a 4m torch despite all that. There’s no stopping it; it’s just a more difficult metal.
This is where your spool gun comes in. Because the wire is loaded into the gun (and then fed through the engine on the gun the same way the wire is fed through a machine’s roller mechanism), it has less distance to travel and less chance to kink.
Aluminium and soft wires are best for spool guns, though you can still run steel through them, as there are rollers available for both.
Most machines will include a switch inside them that is labelled ‘standard/spool gun’. Make sure this is flipped to the type of torch you have connected; the torch won’t run if the switch is on the wrong setting.
Note : If you have a water-cooling torch, you will also need to attach the blue and red water cables to the welding machine and the water cooler so that the water can flow through the torch.
4. Wire Spool
Before you begin, it’s essential that the filler metal you purchase matches the metal you plan to weld (your parent metal). Thanks to chemical compounds, mismatched metals won’t weld together properly unless you are using a filler metal capable of doing this, and the weld will be terrible quality.
The wire spool is like a loaded spring, so when you first undo the wire, don’t place it straight down onto a table or other surface as it will unravel, and you’ll have to clip off everything that has unwound.
Unfortunately, you won’t be able to rewind it because it’ll no longer be precision wound, and there’ll be a much higher chance that the wire will birdnest inside the wire feed mechanism, halting your weld.
The spool attaches inside the machine on the spool holder, which consists of a shaft and a nut. There is a locating lug on the back plastic plate of the spool holder that you need to line up with the locating hole on the wire spool. These look like a small round bump and dent, respectively. Once you’ve lined them up, slide your spool onto the shaft and screw your nut back in to lock the spool into place.
You’ll need to feed the first part of the wire into the inlet guide, over the roller and into the beginning of the guide tube before you let go of it to stop it from unravelling.
Now that the wire spool is attached inside the machine, feed it through the torch until it sticks out of the torch nozzle. You can feed the wire through in two ways; hold down the trigger on the torch or press the feed wire button inside the machine.
When feeding through a new spool of wire, it’s a good idea to remove the nozzle and contact tip from the end of the torch so that the wire doesn’t catch on them and birdnest inside the machine. Both parts screw on and off with ease, so there’s no hassle.
With a new spool, you’ll also need to adjust the tension on the wire. Feed your wire until about 50mm (5cm) hangs out of the torch tip.
Lock the tension lever and decrease the tension by rotating counter-clockwise so that the wire slips (the rollers are spinning, but the wire doesn’t move) when the trigger is pulled. Now turn your tension lever clockwise 180° to increase your tension and grip the exposed wire between your thumb and forefinger (in gloves, the wire gets hot) with light pressure.
Pull the trigger again while holding the wire. If the wire slips again, repeat the process, rotating the tension lever clockwise by 180° each time, until you can’t stop it with your fingers, and it feeds smoothly. Be careful though, too much tension can flatten your wire.
Once you’ve sorted your tension, trim any excess wire hanging out of the tip. You want your wire to stick out of the torch nozzle by roughly 1cm. If the wire sticks out too far, trim it back. If you start with too much wire, it will just burn off. Some machines have a burnback function that allows you to determine the wire’s burnback after your finish welding as well.

5. Voltage and Wire Speed
Every UNIMIG welding machine comes with a User Manual and Setup Guide, which provides a good starting point for your machine settings. It gives a detailed description of which wire speed and voltage you’ll need for a range of metal types, wire sizes and parent metal thicknesses. It also includes the gas flow rate that is recommended for each of these.

Metal Preparation
Unfortunately, MIG isn’t as forgiving as stick welding, so you’ll need to either wire brush or grind your workpiece so that it’s clean. Otherwise, you won’t get a quality weld.

Starting Your Weld
Now that your machine and workpiece are set up, you’re ready for the next step: starting the weld. With the voltage and wire speed set, the rest of the welding is up to you.
There are three main factors to consider when doing a weld:
- Travel angle & distance
- Travel speed
This is true regardless of whether you are TIG, MIG or stick welding.
1. Work Angle
Your work angle is your torch in relation to the angle of the joint. There are a few different joint types, and several positions these joints can be found.
(These angles do not include your travel angle, which we’ll talk about next.)
The main thing that your weld’s position will affect is whether or not you’ll be fighting against gravity as you go. You’ll usually need to increase your travel speed and lower your amps to keep the molten metal from dripping, so while you’re learning, flat positions are best.
2. Travel Angle & Distance
When MIG welding, you can travel at a pushing or a pulling angle, though it does depend on which wire is in the machine.
If you’re using mild steel, stainless steel or aluminium, you’ll want to travel at a pushing angle (torch over the weld pool pushing towards the metal).
If you’re using flux-cored wire (gasless), you’ll want to travel at a pulling angle (torch in front of the weld pool and dragging towards the metal).
Whether you’re pushing or pulling, you want to keep your torch at a 10° to 15° angle. If your angle becomes too deep or parallel with the metal you’re welding, you increase the spatter amount, decrease penetration, and create more mess that you’ll have to clean up later.

For example, say you’re welding in a fillet joint (a corner join) with a standard steel wire. Your torch will be angled into it at a 45° angle, and then you’ll angle slightly to the side (in a push direction) so that your gas can cover the weld pool and in front of the weld as you go.
The other important thing to watch is the distance of your wire ‘stickout’. You want to maintain the 1cm of stickout throughout the joint for the best weld. If your wire is sticking out too far as it’s feeding and your torch nozzle is getting further away from your workpiece, it will cause a few problems.

The first problem is that your feeding wire acts as a resistor, so the longer it is coming out of the torch and into the weld pool, the lower your machine will drop the amps, so it won’t run as well. The second problem is that your shielding gas will no longer be able to reach your weld pool, and you’ll increase the number of defects – like porosity – in your weld.
3. Travel Speed
Travel speed is how fast you are moving the torch along the weld. This is separate from the wire speed, but the two do impact each other.
If you’re moving too fast for your set wire speed, then there’ll be nothing being fed into the weld pool to create a proper weld.
On the other hand, if you’re moving too slowly or you have too much wire being fed through, you’re going to have a fat weld join that will need to be ground back, causing a lack of fusion on the toes (edges of the weld).
You want to move at a speed that corresponds with your settings. Keep your travel speed consistent across the entire weld for the best quality result.

Place your cleaned workpiece in front of you in a way that when you begin welding, your hands can move freely and steadily all the way along the joint. It’s a good idea to have something to steady your hands against as they go along the weld so that you can maintain your angle and distance.
Check that your earth clamp has been attached to a metal surface, such as a (clean) metal workbench or the workpiece, because if your earth clamp isn’t grounded, your machine won’t start.
If you’re making a fillet join, you can use a magnetic welding clamp to hold your two pieces of metal together. Aluminium isn’t magnetic, however, so a manual clamp will be needed.
The kind of wire you are using will determine the technique required when welding.
Push Technique (Gas-shielded Wires)
The wire is located at the leading edge of the weld pool and pushed towards the un-melted work surface. This technique offers a better view of the weld joint and direction of the wire into the weld joint.
The push technique directs the heat away from the weld puddle, allowing faster travel speeds and providing a flatter weld profile with light penetration – useful for welding thin materials. The welds are wider and flatter, allowing for minimal clean up/grinding time.
Pull Technique (Gasless Wires)
The gun and wire are pulled away from the weld bead. The arc and heat are concentrated on the weld pool. The base metal receives more heat, deeper melting, more penetration and the weld profile is higher with more build-up

Start with your tacks. Remember to flip your welding helmet down before you ignite your arc. Tacks are used to fuse the metals together at the edges, so you don’t have to hold them together while you’re trying to weld.
Line your torch tip and wire up with where you want to make your tacks (usually on the edges of the piece) and press the trigger of your torch. You’ll need to hold it continuously to maintain the arc. Hold it for a second or two until a small weld has formed, and then let go.
These won’t take more than a few seconds each to make; they only need to hold your joint together so you can make the proper weld without needing a clamp.
MIG welding itself is relatively easy once you’ve got the hang of your angles and speed; all you need to do is press the trigger and start pushing or pulling your weld along the joint.
A good way to tell if it’s going well is by how it sounds and how it looks while you’re doing it. A proper weld should sound like crackling bacon. Being able to identify this is something that takes a bit of experience, but if something is really wrong, you’ll notice pretty fast.
If you’re trying to weld thicker pieces of metal together, adjust your volts and wire speed accordingly.
Once you’ve run your weld along the joint, you’re done. You’ve made your first weld!
Because MIG welds do make spatter, and if you use a gasless wire with a flux core, some post weld work needs to be done. If you’ve used a flux wire, you’ll need to use a chipping hammer to take off the slag that formed its protective layer over the top of the weld.
If there is spatter everywhere, you can grind this off for a cleaner looking weld or, alternatively, you can use an anti-spatter spray before welding. If the weld is just for practice, it doesn’t matter how good it looks.
Just remember that dry runs and scrap metal are your friends. Practice running your welding torch across a piece of metal, maintaining your travel angle, distance and speed until you’re confident that you can keep all three of them consistent.
Once you’re happy with your performance on a dry run, try it again on some scrap metal before you move on to the piece you’re planning on welding. If you don’t get it the first attempt, that’s fine; no one’s expecting you to be a welding expert on your first go. Practice makes perfect.
← See all articles

Hobby MIG Welding Calculator
This calculator is intended as a guide to initial power and wire feed settings for people new to welding. The settings in the calculator suit me (a DIY welder).
Take it as a starting point but use other pages on this tutorial (such as the page about setting wire speed and the one about finding the right voltage setting ) and play around on some scrap to find settings that suit your own welding speed and technique.
How to use the calculator
These figures can be found from manufacturer or retailers' specs.
For example a Sip Migmate 130 has a minimum output current of 25 amps, maximum of 130 amps, and has 6 power settings.
Use the links below to fill in the form with data for the following welders:
Clarke 90EN
SIP Migmate 130
Clarke 160TE
Portamig 181
The estimates will appear in a table (above) after you have filled in the form.
Wire speed Reference
The 0.6mm wire size figures have been tested to 2mm and the figures are extrapolated. The 0.8mm figures have been extrapolated from the 0.6mm results so will be less reliable, but they are at least a starting point. Where the figures are against a grey background the wire size isn't really suitable for the material thickness.
The markings on welder wire feed controls do not represent speed in metres per minute. Measure the speed using a stopwatch and tape measure. It might be useful to mark positions around the wire feed knob for future use.
How it was done
The estimates are based on experimental results from a Clarke 90EN, a Clarke 155T, and a Portamig 181, and gaps have been filled in by extrapolation. The method is un-scientific, but the results seem quite accurate for my own welding technique and at the very least should be good for a starting point.
The settings are only intended as a starting point. The wire speed and power settings pages should help fine tune the settings for your welder and welding technique.
Do post on the forum with any feedback or problems you may have with the calculator or my suggested settings.
Installing the wire
Power and wire speed calculator
Torch position and laying welds
Setting the wire speed
Finding the right power setting
Butt welding
Welding safety

- How to & Guides , Welding
Mig Welding Wire Speed And Voltage Chart
- January 18, 2023
- By chaitanya
MIG welding is definitely one of the most popular metal joining processes in the industry right now and it is widely used for a wide range of applications. MIG welding is currently popular for professional as well as personal applications. A lot of DIY enthusiasts also prefer using MIG welding for their projects since this welding method produces strong and reliable joints.
However, you won’t get satisfying results with the process if all the parameters are not set up correctly. While the MIG welding process is definitely easier compared to other welding methods, you will need a core understanding of the process as well as the importance of some crucial factors to get the results that you desire. A lot of MIG welders have trouble with the wire speed and voltage regulation of the machine, both of which can greatly impact the end results.
So, we will be discussing the importance of welding wire feed speed and voltage regulation in detail in today’s guide. Here, you will also find a reference chart that can guide you with perfect values for both feed speed as well as voltage levels for your project. So, make sure you refer to our MIG welding wire speed and voltage chart provided here. We will also discuss some more important factors regarding the same in this guide, so make sure you don’t miss that.
MIG Welding Wire Speed & Voltage Chart
In these charts, we will be comparing the appropriate voltage and wire speed needed for the job. So, you can get a pretty good deal about the setup needed for your project and expect good results by using these wire speed and voltage settings.
But before that, you should make sure that you have the correct welding wire according to the amperage of the machine. Otherwise, changing the voltage or feed speed wouldn’t offer much of a difference. Here’s a basic table for reference according to the usual thickness of the wire.
Now that you have a basic idea about the appropriate wire size for the job, check out this chart to get an idea about the correct voltage level according to the thickness.
You can also get an idea about the suitable wire feed speed based on the comparison presented in the following table. For that, you will also have to consider the voltage and amperage of the setup along with the thickness.
How To Determine MIG Welding Wire Feed Speed?
Even though you can get an approximate idea about the appropriate wire feed speed for your job from the reference table provided above, you can easily calculate the exact wire feed speed that will be perfect for your job. By applying a simple formula and basic multiplication, you can find out the correct wire feed speed to get flawless welds on your job.
To do that, simply multiply the required current of the welding machine by the flame rate by which the wire is being fed to the job. This will give you direct value for appropriate feed speed in inches per minute, or meters per minute based on your unit system.
Ex. Consider that you are working with a 100 amps welding setup and it offers 3 inches flame rate. So to determine the welding speed, simply multiply the 2 units, which will give you 300 inches per minute, the ideal wire feed speed for the job.
Formula For MIG Welding Efficiency
In case you are wondering how long it will take you to finish a certain job based on your wire feed speed, you can do that by applying another simple formula. This formula will basically tell you about the efficiency of your process, based on the welding length and possible length welded per minute.
It is a pretty simple calculation as you only need to count the approximate time taken to finish an inch of the weld and divide it by the total welding length. So if the welding rate is about 4 inches per minute and you are willing to cover about 40 inches of weld, it will take you around 10 minutes to finish the job.
However, keep in mind that this is an approximate calculation and the actual time needed for the job may vary based on many different factors. The time needed to cover an inch of the weld will not be constant throughout the length. Also, you need to consider the duty cycle of the MIG welder for larger jobs in order to get a better idea of the total time required to finish the job.
How To Set Up Wire Feed Speed & Welding Voltage?
Setting up the wire feed speed and the voltage level of the machine is pretty easy. Almost all modern MIG welders have a digital meter to offer precise settings for both the voltage level as well as the wire feed rate. But as for how to select the correct values, it will take you a little bit of experience and understanding of the machine. You can follow some helpful tips that will surely help you along the way.
- Select a common amperage for all welding wires.
- Make sure that the thickness of the workpiece is below 8 inches.
- As for the welding time, consider managing all the settings to get 250 inches per minute feed speed.
- Once you start the welding process, set the voltage level according to the requirement.
- Keep an eye on the tension nuts before starting the process.
- Start the welding again with the right parameters.
- Now, you can easily set up the wire feed speed and voltage based on the results.
Voltage Requirement For MIG Welding
There are many different schools of thought on this particular matter. While a lot of users will suggest that 220 or 230 Volts are required for MIG welding, there are some that believe 240 Volts to be the right voltage level for this job. To be on the safe side, we will also recommend you use 240 Volts for MIG welding on a single-phase connection.
With that being said, you don’t actively need to look out for a MIG welder that specifically says 240 Volts. Technically, 220, 230, and 240 Volts are pretty much the same thing. So, you can buy a 220 or a 2230 Volts MIG welder without any worries and then convert it later to a 240 Volts to get better welding results.
Supported Thickness For 180 Amp MIG Welder
Right now, the most popular MIG welders on the market are 180 Amps MIG welders. If you have also recently purchased a 180 Amps MIG welder, you must be wondering the capabilities of the machine and whether it is suitable for your task or not. In the majority of cases, the compatibility issue is regarding the supported workpiece thickness.
If you have a 180 Amps MIG welder, you should know that these machines are capable of welding up to 3/16 inch or 4.7 mm thick workpiece. The thickness of the weld on the other hand would be around 0.035 inch.
Impact Of Voltage On MIG Welding
The voltage is one of the most crucial factors of MIG welding and it has a drastic effect on the end results, whether it is the reliability of the weld or the compatibility of the given job. The voltage level of the welding process will alter the length of the arc. The arc is basically the gap between the filler wire and the welding surface. As you increase the voltage level, the MIG welding ball will also grow and have an increasing effect on the ratio of width to depth of the weld.
We hope that you have found all the necessary information about MIG welding voltage level and wire feed speed in this guide. Here, we have discussed the importance of both of these factors along with some helpful tips which will surely come in handy for a beginner. You can also refer to our charts for MIG welding wire speed and voltage and get an idea about the suitable parameters for your job. But, you should know that the best way to get a hang of the process is to experiment with different settings around the approximate values to find out the perfect options according to your workpiece material, thickness, and welding length.
Related Posts:
- Cold Welding - Applications, Differences & Variations
- Plug Weld - Welding Process, Symbols, Advantages & Uses
- GMAW Vs SMAW
- Welding Transfer Modes
- Stick Vs Mig Welding
- MIG Wire Sizes
Leave a Reply Cancel reply
Your email address will not be published. Required fields are marked *
Get our Latest Newletters
Get great content that you love. No ads or spams, we promise.

Tutorials Symbols Courses Calculator Deals
Electrical Electronics Embedded Power Robotics ARM IOT
Mini projects Microcontroller Arduino Solar Free circuits Home Automation Seminar Topics Electronics Questions
Capacitors Resistors Filters Diodes Transistors Amplifiers IO Devices Thyristors DC Circuits Number System
Your Privacy is important to us
Tutorials Symbols Courses Calculator
- Affiliate Disclosure
- Terms and Conditions
- Privacy Policy
Copyright © 2024 Electronicshub.org

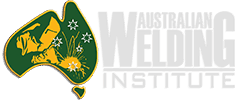
Travel Speed Calculator
Heat input calculator.
To use the Travel Speed calculator, insert the the time taken to complete the weld and the weld length into boxes of formula 1
Next, input your recorded welding Amps and Volts into formula 2 and it will calculate the Heat Input
- 1.TRAVEL SPEED CALCULATOR [Input the time taken & the length of weld]
- Weld time * sec
- Weld length * mm
- Calculated Travel Speed mm/min
- 2.HEAT INPUT CALCULATOR [Input Amps, Volts]
- KiloJoules kJ/mm
Settings Lab
Mig welding wire speed and voltage chart.
Recently, many people have decided to take up welding. Even though they might not have formal training, these individuals might offer decent projects.
If these jobs require the use of the MIG welding machine, the amateur welder should know how to adjust the item. For this reason, it would help if they used a wire speed and welding chart to get things sorted.
Are you looking for the ideal ways of adjusting your MIG welding? If yes, here are some of the recommended settings for the task.

MIG Welding Wire Speed and Voltage Settings Chart
Here is a chart showing the wire speed and voltage speed settings required for various tasks. But before using these values, we suggest that you have a decent understanding of your preferred metal. Also, consider the amperage settings and the task at hand.
MIG Welding Wire Speed and Voltage Speed Chart for E71T-GS + Flux Core + Tubular
Mig welding wire speed and voltage speed chart for er70s-6 + 75% ar/25% co2+20cfh , mig welding wire speed and voltage speed chart for er70s-6 + co2+20cfh , mig welding wire speed and voltage speed chart for e71t-gs + flux core + tubular ( 0.30 wire size).
- 9.5 mm material thickness : 20 ( Voltage), 375 ( Wire Speed)
- 8 mm material thickness: 20.5 ( Voltage), 335 ( Wire Speed)
- 6.4mm material thickness : 20 ( Voltage), 280 ( Wire Speed)
- 4.8mm material thickness : 19 ( Voltage), 240 ( Wire Speed)
- 2.8mm material thickness : 19 ( Voltage), 200 ( Wire Speed)
MIG Welding Wire Speed and Voltage Speed Chart for ER70S-6 + 75% AR/25% CO2+20CFH ( 0.30 Wire Size)
- 9.5 mm material thickness : 20 ( Voltage), 390 ( Wire Speed)
- 8 mm material thickness: 19.5 ( Voltage), 335 ( Wire Speed)
- 4.8mm material thickness : 18 ( Voltage), 240 ( Wire Speed)
- 2.8mm material thickness : 18 ( Voltage), 200 ( Wire Speed)
MIG Welding Wire Speed and Voltage Speed Chart for ER70S-6 + CO2+20CFH ( 0.30 Wire Size)
- 9.5 mm material thickness : 22 ( Voltage), 390 ( Wire Speed)
MIG Welding Wire Speed and Voltage Speed Chart for E71T-GS + Flux Core + Tubular
If you want to work with this combo, you will have to use different settings based on the thickness of the wire and material. Let’s say you are working with 0.030″ wire thickness with a 9.5mm material thickness, you will have to use a voltage and wire speed of 20 and 375. But if you are using the same wire thickness with a 8mm material thickness, you can leave the voltage and wire speed on 19 and 340.
As expected, these settings can make your task easier. On top of that, it can also provide interesting effects on the job at hand.
MIG Welding Wire Speed and Voltage Speed Chart for ER70S-6 + 75% AR/25% CO2+20CFH
Are you looking for the MIG wire speed and voltage speed for working with these conditions? Supposing you are dealing with 0.035″ wire thickness and material thickness of 9.5mm, set the machine with a voltage and wire speed of 21 and 310.
As for using the same wire thickness for a material that is 8mm thick, adjust the voltage and wire speed to 20.5 and 285. Normally, these settings can provide positive results.
MIG Welding Wire Speed and Voltage Speed Chart for ER70S-6 +CO2+20CFH
If you have a welding project that involves these conditions, it would help if you got the right settings. For working with a wire thickness of 0.045″ and material thickness of 9.5, stick with a voltage and wire speed of 23 and 240. But if the task requires a material and wire thickness of 8, you can work with 22 and 280.
Supposing you are working with a 0.035 wire thickness and a material of 9.5mm thickness, it would help if you adjusted the device to 23 ( voltage) and 240 ( wire speed). As expected, these settings should offer good results.
Related Posts

Milorganite Spreader Settings Guide

Groundwork Spreader Settings Guide

Azomite Spreader Settings Guide

Sta-Green Spreader Settings Guide

Brinly Spreader Settings Guide

Spray Transfer Welding Settings Guide

IMAGES
VIDEO
COMMENTS
Here are the most-used wire sizes in MIG welding. Notice that these sizes overlap through each current range. This gives you some choice about what works best for your welder and your technique. 0.023 - 30-130 amps. 0.030 - 40-145 amps. 0.035 - 50-180 amps. 0.045 - 75-250 amps.
Using Simple Methods For Calculating Starting Wire Feed Speed, Voltage, and Travel Speed. The Bartonian Conversion Factor (Table 2) makes things a bit easier for fillet welds. The example below uses the conversion factor to calculate travel speed at 5.57 IPM for that same 3/8 in. fillet weld using a 0.045 in. solid wire.
Good equipment makes MIG welding easier, while poor equipment can cost you dearly in frustration and weld quality. ... If a manual or weld specification sheet is not available, use the multipliers in the following chart to find a good starting point for wire feed speed. For example, for .030-inch wire, multiply by 2 inches per amp to find the ...
Consult your MIG welder's chart for a rough guide on wire feed speed and voltage settings according to material thickness. From there, it's fine-tuning based on your specific scenario and welder's feel. A too slow wire speed might result in a weak weld, while a too fast speed may cause the wire to burn back towards the contact tip.
If there are no guidelines, you can use our chart to serve as a starting point. For example, for .030-inch wire, multiply by 2 inches per amp, while for .023, multiply it 3.5 times. For wire size multiply by Ex. using 1/8 inch (125 amps) .023 inch. 3.5 inches per amp. 3.5 x 125 = 437.5 ipm.
The formula for travel speed in welding can be determined by dividing the length traveled (l) by the time taken (t) to travel that length. In this case, with a length (l) of 150 mm and a time (t) of 68 s, the travel speed can be calculated as 150 mm / 68 s = ~2.2 mm/s or 132 mm/min. Therefore, the formula for travel speed in welding is l / t.
NOTICE - Each welding application is unique. Although certain Miller Electric products are designed to determine and default to certain typical welding parameters and settings based upon specific and relatively limited application variables input by the end user, such default settings are for reference purposes only; and final weld results can be affected by other variables and application ...
Part 1 in our GMAW series, Gas Metal Arc Welding Basics, Part 1: Welding Current and Voltage, discussed how variations in both welding current and welding voltage affect the penetration profile and bead profile of a weld. In this installment, the variables of travel speed and contact tip to work distance (CTWD) will be discussed in the same fashion.
Once you click the calculate button, the required travel speed will be displayed in inches per minute. The deposition rate will also be displayed below the travel speed in lbs. per hour. The tool can be used to quickly setup automated or semi-automated GMAW / MIG welding equipment. Fillet Weld Size 3/16" 1/4" 5/16". Steel Stainless Aluminum.
MIG (GMAW) Welding 154557D 2018−01 Guidelines For Gas Metal Arc Welding (GMAW) For product information, Owner's Manual translations, ... Typical GMAW Semiautomatic Setup With Constant Speed Feeder 6..... 2-2. Typical GMAW Semiautomatic Setup With Voltage-Sensing Feeder 7..... 2-3. Typical GMAW Process Control Settings 8.....
A MIG welding wire speed and voltage chart provide essential settings based on material thickness and wire diameter. Adjusting them optimizes welding performance and quality. Navigating the complexities of MIG welding requires a deep understanding of its two pivotal parameters: wire speed and voltage. These settings can significantly impact ...
The most important MIG welder settings are voltage, wire feed speed, and shielding gas flow rate. These settings determine the heat, wire deposition rate, and protection from atmospheric contamination, respectively, crucial for producing strong and clean welds. As we go along, you'll learn how to balance voltage and wire feed speed for ...
Travel Speed Calculation Travel speed = (deposition rate) × (# of passes)/5 × (weight of weld metal per foot {lb/ft}) = Travel speed = {7.96 x 1} / {5 x 0.2887} = 5.52 ipm. CALCULATING WIRE-FEED SPEED WITH DEPOSITION RATE Let's assume a requirement to make fillet welds at a rate of 12 lb/hr using 0.045 in welding wire.
The welding parameters vary for each of the recommended wire diameters and also depend on how thin the material is. For example, both 0.024- and .30-inch solid wires can be used to weld 24-gauge material using a welding current of 30 to 50 amps and travel speeds of 10 to 20 inches per minute (ipm). The voltage and wire feed speed vary though.
Ensure MIG torch is completely unravelled until setup is complete. Carefully feed in the new liner down the torch lead all the way to exit the torch neck. Fit the liner retaining nut and screw only 1/2 way down. Snip the excess liner off, about the length of the where tip holder sits past the end of the torch neck.
In this episode of #MIGMonday we are showing you the effects of travel speed on your weld profile. Travel speed is one of the biggest mistakes people make wh...
Browse suggested weld parameter settings for Stick Welding, TIG Welding, MIG (Solid-Wire) Welding and MIG (Flux-Core) Welding.
Hobby MIG Welding Calculator. This calculator is intended as a guide to initial power and wire feed settings for people new to welding. The settings in the calculator suit me (a DIY welder). Take it as a starting point but use other pages on this tutorial (such as the page about setting wire speed and the one about finding the right voltage ...
40 to 145 Amps. 0.030 inch. 50 to 180 Amps. 0.035 inch. 75 to 250 Amps. 0.045 inch. Now that you have a basic idea about the appropriate wire size for the job, check out this chart to get an idea about the correct voltage level according to the thickness. Thickness. Suitable Wire Voltage for 0.045 Volts.
MIG welding is a common welding process for beginners. Learn the basics for MIG welding mild steel with your Millermatic® MIG welder. ... A convenient reference chart, located on the inside of the door housing the wire feed system ... Note that travel speed — the rate at which you move the gun along the joint — influences the shape and ...
To use the Travel Speed calculator, insert the the time taken to complete the weld and the weld length into boxes of formula 1. Next, input your recorded welding Amps and Volts into formula 2 and it will calculate the Heat Input. 1.TRAVEL SPEED CALCULATOR [Input the time taken & the length of weld]
MIG Welding Wire Speed and Voltage Speed Chart for ER70S-6 +CO2+20CFH. If you have a welding project that involves these conditions, it would help if you got the right settings. For working with a wire thickness of 0.045″ and material thickness of 9.5, stick with a voltage and wire speed of 23 and 240. But if the task requires a material and ...